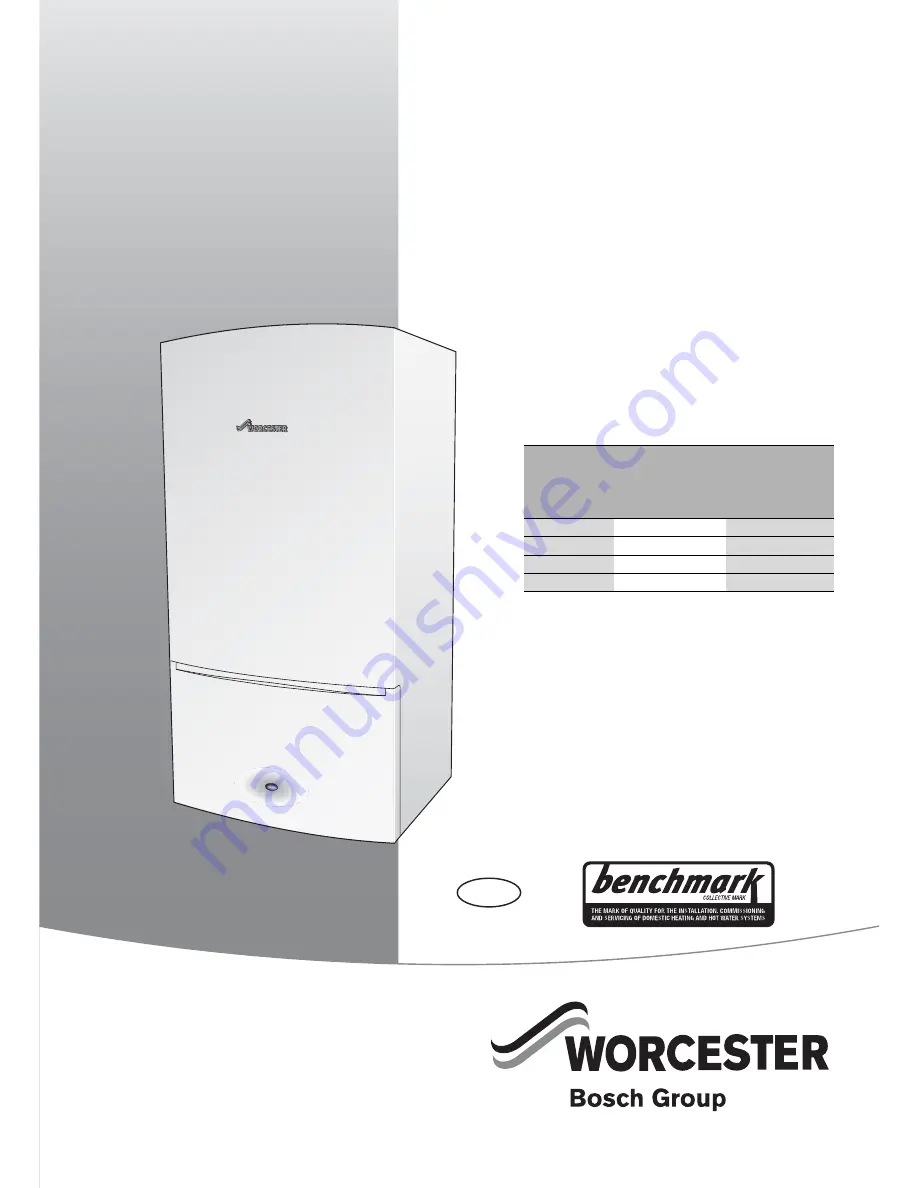
UK/IE
INSTALLATION, COMMISSIONING AND SERVICING INSTRUCTIONS
WALL HUNG RSF GAS FIRED CONDENSING SYSTEM BOILER
Greenstar i System Compact
6720646608-00.1W
o
FOR SEALED CENTRAL HEATING SYSTEMS AND INDIRECT MAINS FED DOMESTIC HOT WATER
6 72
0 807 726 (2013/05)
These appliances are for use with:
Natural Gas or L.P.G.
(Cat. II 2H 3P type C13, C33 & C53)
Model
GC Number
Natural Gas
27i System Compact 41-406-13
30i System Compact 41-406-15
L.P.G.
27i System Compact 41-406-14
30i System Compact 41-406-16