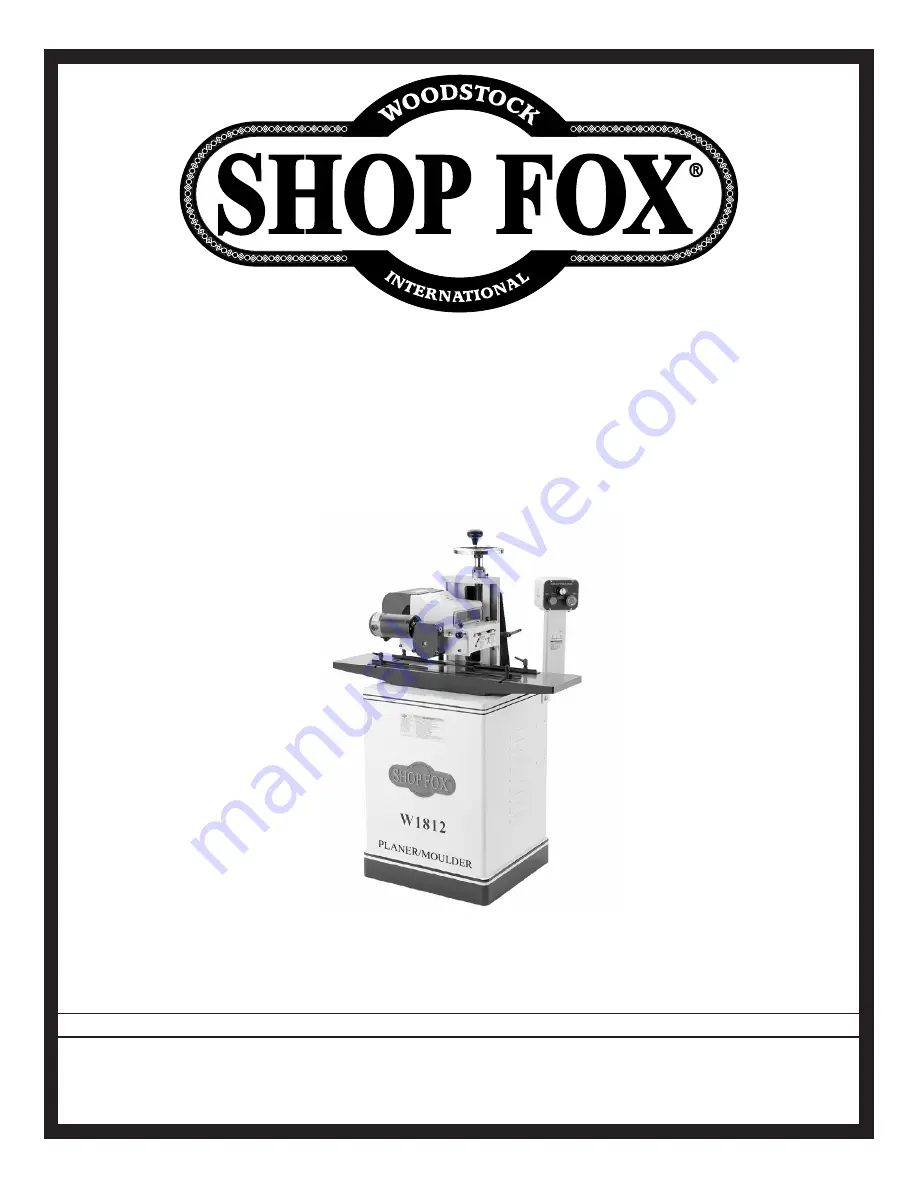
DLC:GHB6CJ6A
E]dcZ/(+%,()"()-'Dca^cZIZX]c^XVaHjeedgi/iZX]"hjeedgi5h]de[dm#W^o
8DENG><=IB6G8=!'%%.7NLDD9HID8@>CI:GC6I>DC6A!>C8#G:K>H:96J<JHI!'%%.IG
L6GC>C</CDEDGI>DCD;I=>HB6CJ6AB6N7:G:EGD9J8:9>C6CNH=6E:DG;DGBL>I=DJI
I=:LG>II:C6EEGDK6AD;LDD9HID8@>CI:GC6I>DC6A!>C8#
Eg^ciZY^cIV^lVc
&&(..8G
BD9:AL&-&'
K6G>67A:HE::9EA6C:G$
BDJA9:GL>I=HI6C9
;DGBD9:AHB6CJ;68IJG:9H>C8:($%.