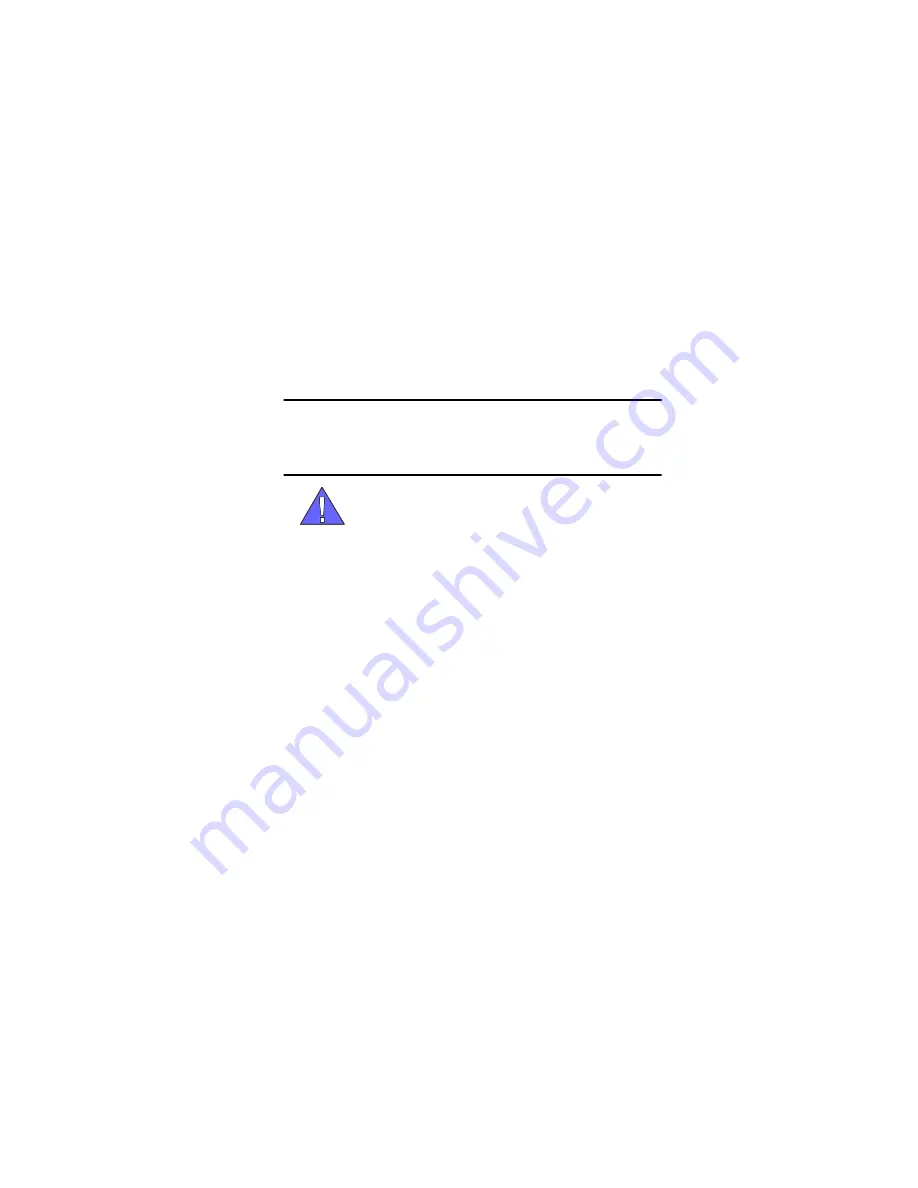
Wood-Mizer
®
Sawmill
Safety, Setup, Operation
& Maintenance Manual
LT35
rev. A6.11
Safety is our #1 concern!
Read and understand
all safety information and instructions before oper-
ating, setting up or maintaining this machine.
Form #1773
Wood-Mizer
®
Sawmill
Safety, Setup, Operation
& Maintenance Manual
LT35
rev. A6.11
Safety is our #1 concern!
Read and understand
all safety information and instructions before oper-
ating, setting up or maintaining this machine.
Form #1773