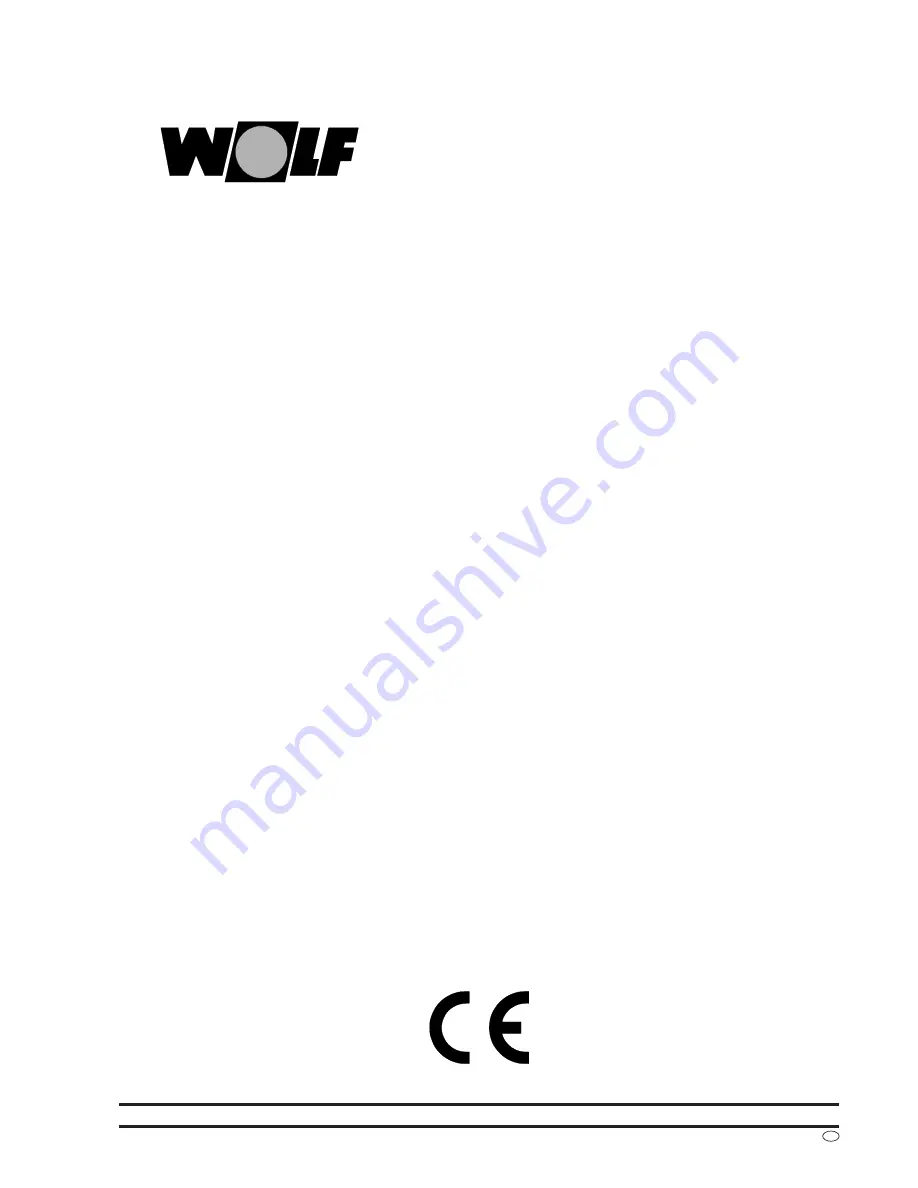
1
Technical Guide
and
Installation Instructions
MKS / MUS Steel boiler
70 - 550 kW
The installation instructions for the Unit pressure jet oil burner is included in the pressure
jet oil burner pack.
The control unit installation and service instructions
included in the control unit pack.
Wolf GmbH · 84048 Mainburg · Postfach 1380 · Tel49-8751/74-0 · Fax +49-8751/741600
Part no. 30 48 034
03/03 TV
GB
Summary of Contents for MKS 140
Page 18: ...18 Notes ...
Page 19: ...19 Notes ...