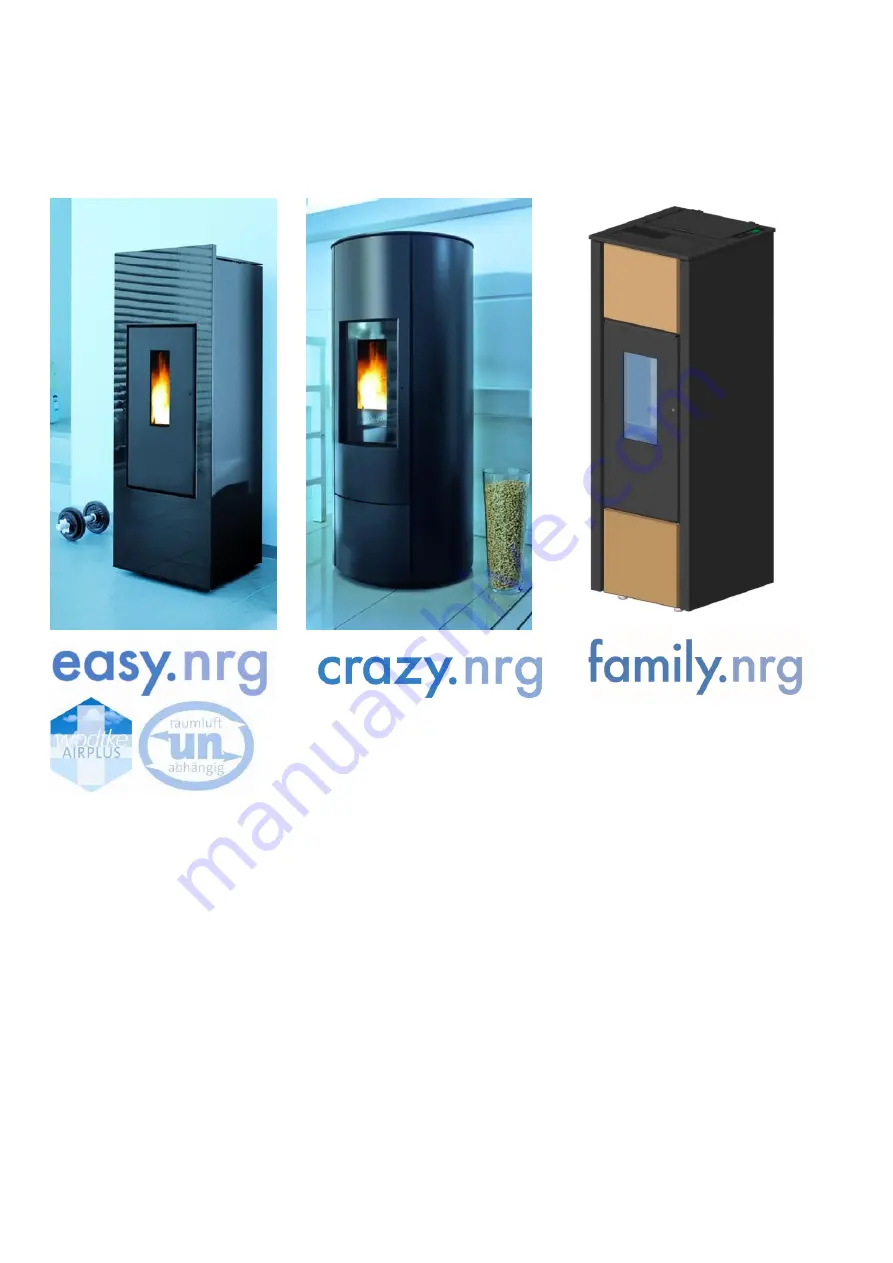
wodtke
Pellet
Primärofen
®
- Technology
Assembly and Operating Instructions
Control S5
Ofentyp PO 03-2 "easy.nrg
®
", PO 03-5 "crazy.nrg" and PO 03-7 "family.nrg
", Airplus from software S5 007
Thank you for deciding to purchase our product. Please be sure to read the instructions before
installing and commissioning your furnace. By doing so, you will prevent damages which can be
caused by improper installation or operation. Your furnace will reward you and the environment
with optimal functionality.
We wish you cozy warmth and many comfortable hours with your wodtke Pellet Primärofen fur-
nace.
Sincerely, wodtke GmbH