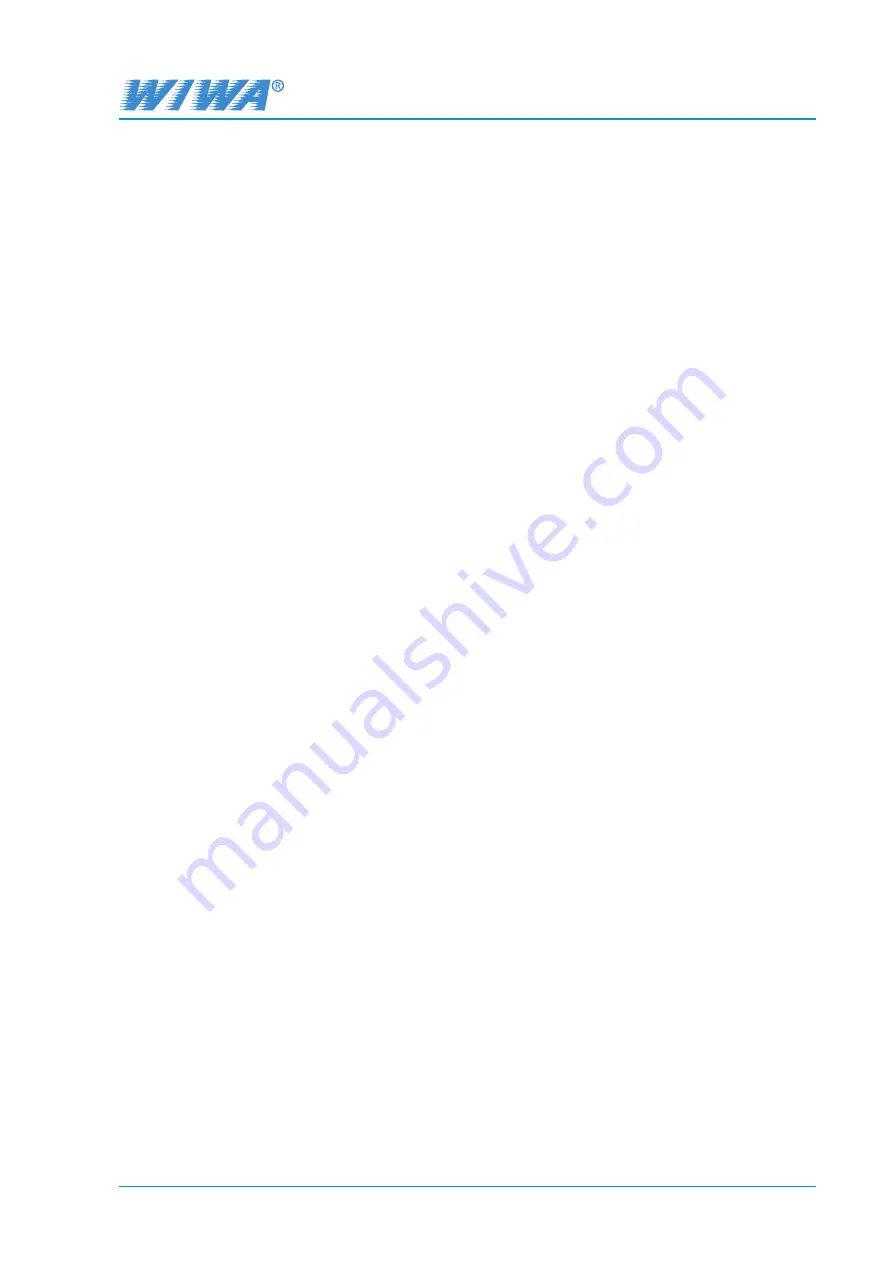
Translation of the original operating instructions
DUO
MIX
270
3
DM270_BAoDB_en_1507 • rs
Contents
Contents
1 Foreword
........................................................................................................6
2 Safety
.............................................................................................................7
2.1 Explanation of symbols ................................................................................7
2.2 Safety information ........................................................................................9
2.2.1 Operating pressure ............................................................................9
2.2.2 Risks due to the spray jet ..................................................................9
2.2.3 Risks due to electrostatic charging ..................................................10
2.2.4 Risks due to hot or cold surfaces .....................................................10
2.2.5 Explosion protection ........................................................................ 11
2.2.6 Health risks ...................................................................................... 11
2.3 Information signs on the machine ..............................................................12
2.4 Safety equipment .......................................................................................12
2.4.1 Safety valves ...................................................................................13
2.4.2 Compressed air shut-off valve .........................................................14
2.4.3 Ground cables .................................................................................14
2.5 Operating and maintenance personnel ......................................................15
2.5.1 Obligations of the machine owner ...................................................15
2.5.2 Personnel qualifications ...................................................................15
2.5.3 Authorised operator .........................................................................15
2.5.4 Personal protective equipment ........................................................15
2.6 Guarantee information ...............................................................................16
2.6.1 Conversions and alterations ............................................................16
2.6.2 Spare parts ......................................................................................16
2.6.3 Accessories ......................................................................................16
2.7 Behaviour in an emergency .......................................................................17
2.7.1 Bring the machine to a standstill and relieve the pressure ..............17
2.7.2 Leaks ...............................................................................................17
2.7.3 Injuries .............................................................................................17
3 Machine description
...................................................................................18
3.1 Intended use ..............................................................................................18
3.2 Erroneous use............................................................................................18
3.3 Machine configuration ................................................................................19
3.4 Compressed air regulation unit ..................................................................21
3.5 Pressure and metering monitoring .............................................................21
3.6 Temperature displays .................................................................................22
3.7 Proportioning pump....................................................................................22
3.8 Mixing unit ..................................................................................................23
3.9 Flushing pump ...........................................................................................24