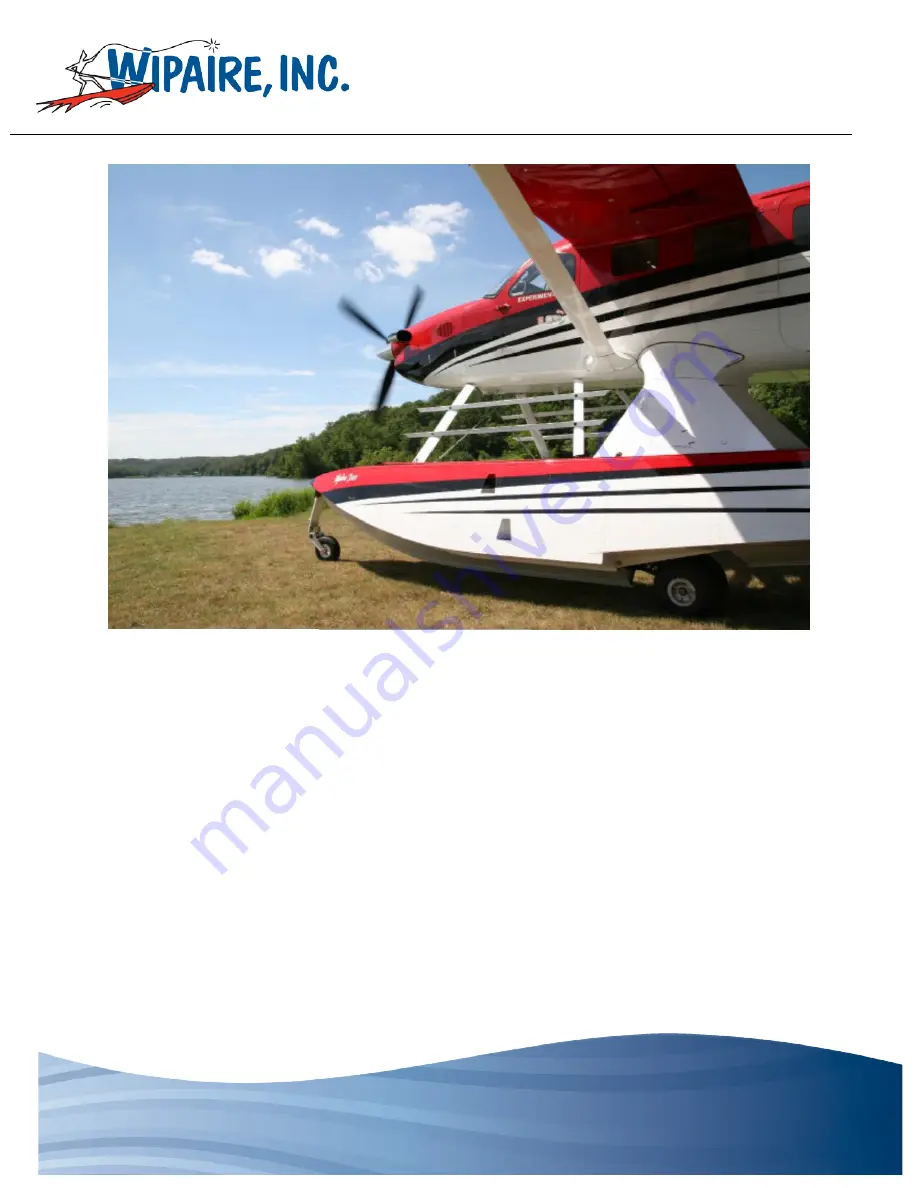
WIPLINE FLOATS • SKIS • MODIFICATIONS • AIRCRAFT SALES
AVIONICS • INTERIOR • MAINTENANCE • PAINT REFINISHING
1700 Henry Ave – Fleming Field (KSGS), South St. Paul, MN 55075
Ph: 651.451.1205 Fax: 651.457.7858
www.wipaire.com
SERVICE MANUAL & ICA
for the
WIPLINE 7000 AMPHIBIAN FLOAT
on the
QUEST MODEL 100 KODIAK