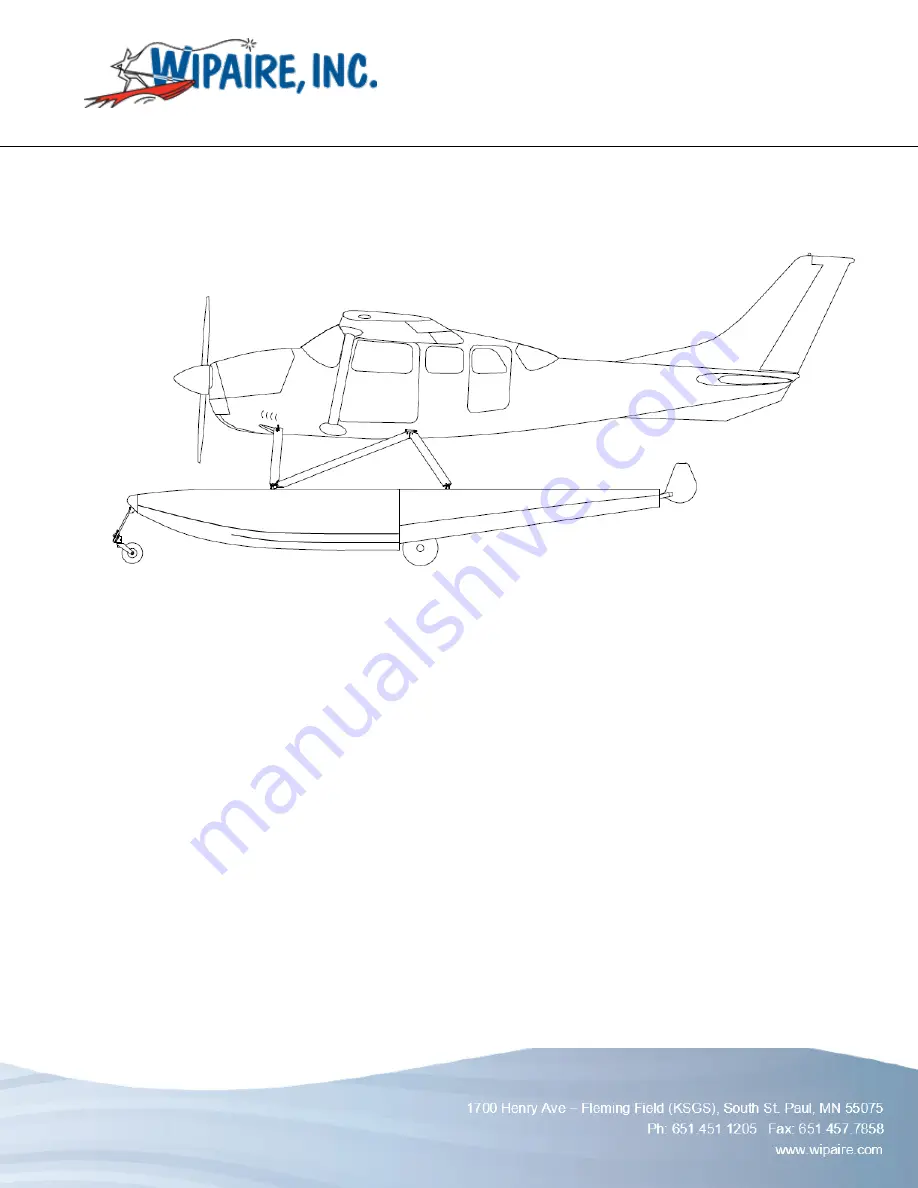
SERVICE MANUAL & ICA
WIPLINE 3730 & 3900 FLOATS
P/N 1002551
Revision K
Page 1
SERVICE MANUAL AND
INSTRUCTIONS FOR CONTINUED AIRWORTHINESS
FOR WIPLINE MODEL 3730/3900
AMPHIBIOUS AND SEAPLANE FLOATS
Revision K
WIPLINE FLOATS • SKIS • MODIFICATIONS • AIRCRAFT SALES
AVIONICS • INTERIOR • MAINTENANCE • PAINT REFINISHING