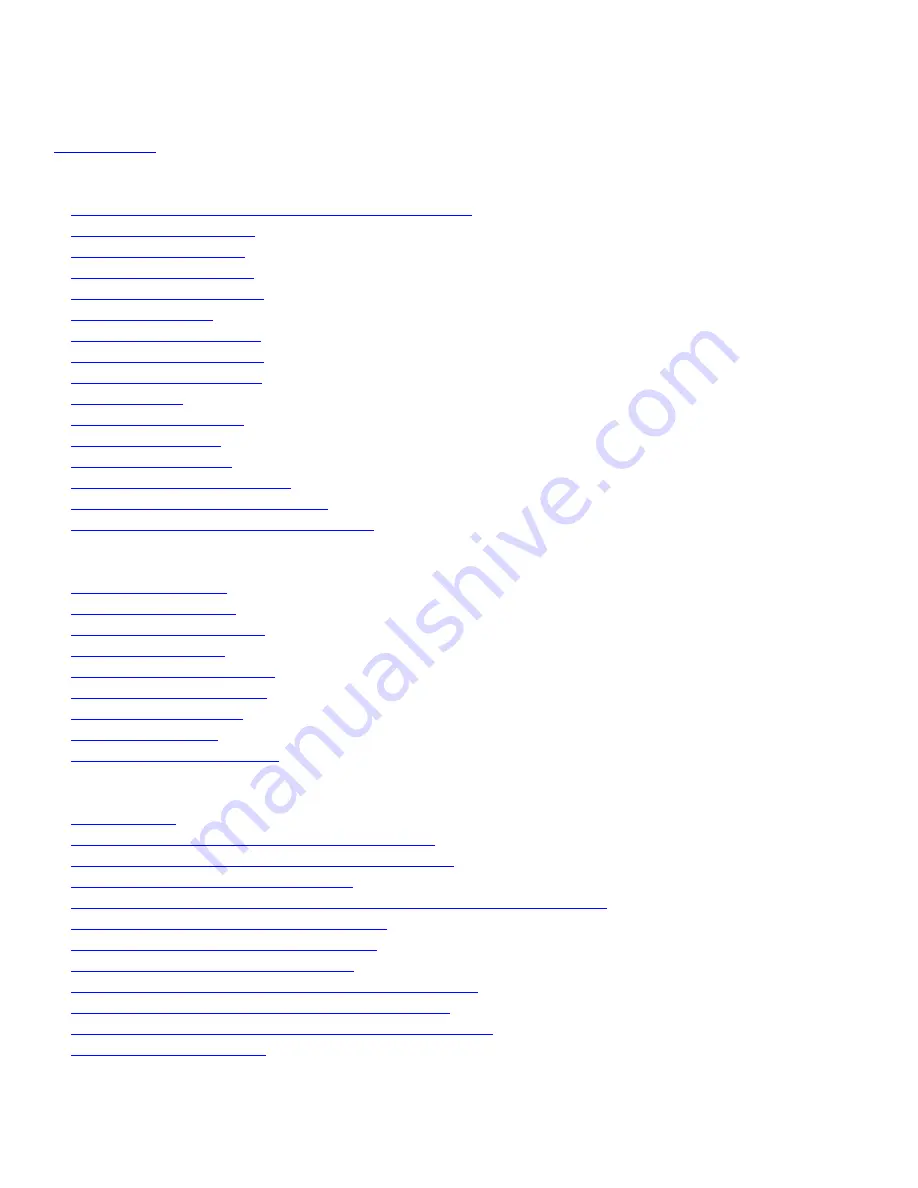
D-250 REPAIR MANUAL
Table of Contents – Page 1 of 5
CHAPTER 1: PRE-DELIVERY SERVICE
REMOVE THE TRACTOR FROM THE SHIPPING CARTON
ATTACH OWNER'S MANUAL TO TRACTOR
CHAPTER 2: GENERAL MAINTENANCE
CHAPTER 3: TUNE-UP
DISTRIBUTOR MAINTENANCE - DISTRIBUTOR CAP
DISTRIBUTOR MAINTENANCE - DISTRIBUTOR WIRES
DISTRIBUTOR MAINTENANCE - ROTOR
DISTRIBUTOR MAINTENANCE - POINTS AND CONDENSER REPLACEMENT
ENGINE TIMING - MARKING THE FLYWHEEL
ENGINE TIMING - STROBE LIGHT METHOD
ENGINE TIMING - TEST LIGHT METHOD
CARBURETOR ADJUSTMENT - ADJUSTING ENGINE IDLE
CARBURETOR ADJUSTMENT - ADJUSTING AIR/FUEL