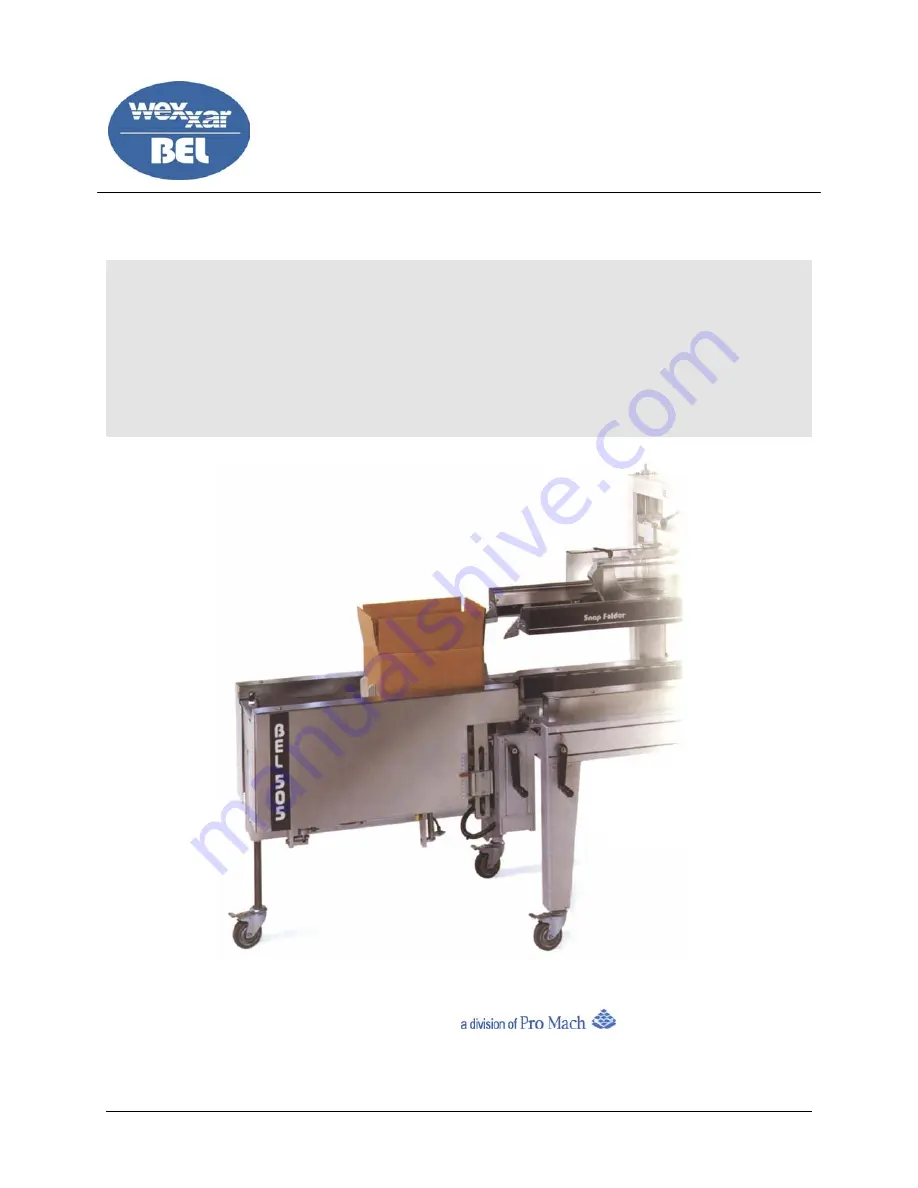
O
PERATION
& S
ERVICE
M
ANUAL
65-11-7
BEL 505 / BEL 505S
S
EMI
-A
UTOMATIC
C
ASE
F
ORMER
AND
P
ACKING
S
TATION
Wexxar Packaging Inc
.
E-mail: [email protected]
Phone (604) 270-0811 • Fax (604) 270-7897
65-11-07 2/5/2007