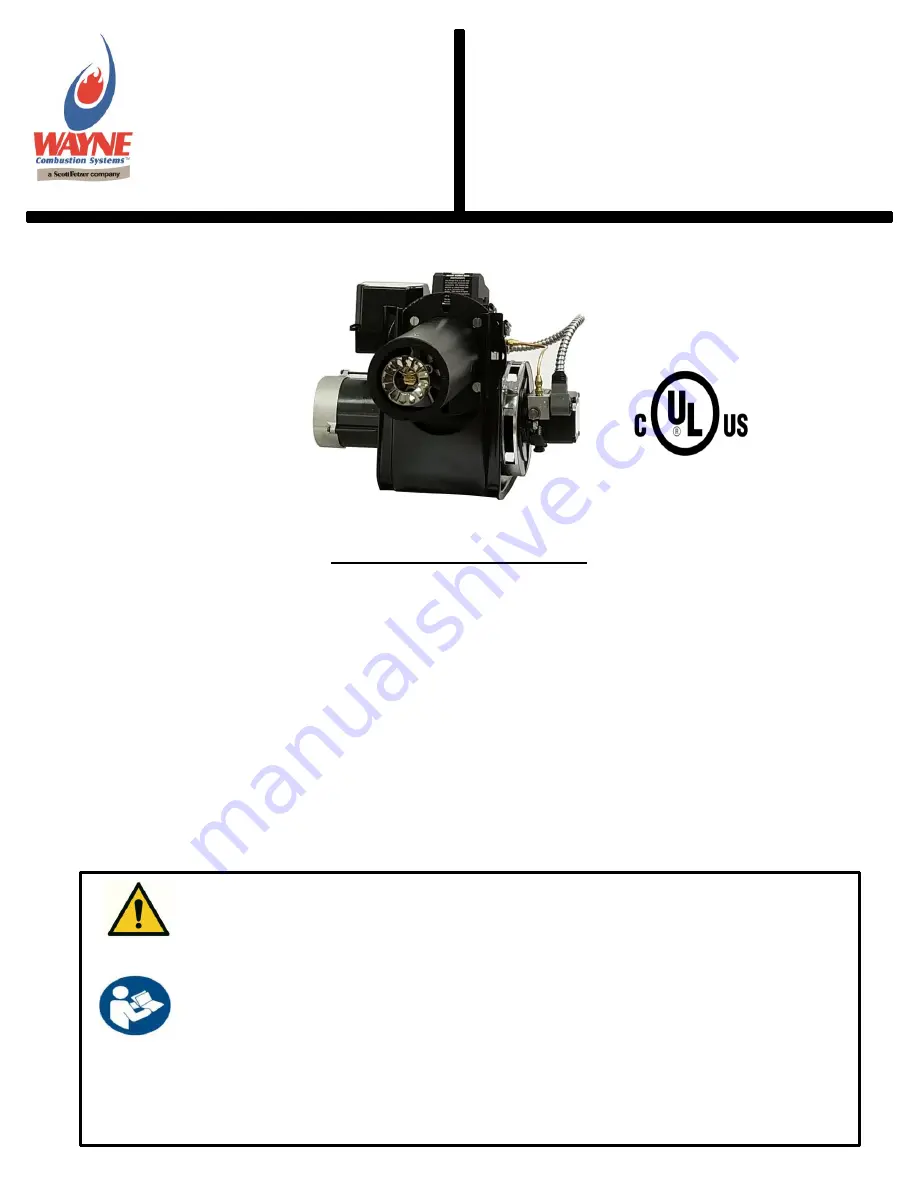
1
Manual 21530 | Revision 10 | Publication Date: 9/14/18
UL File Number: MP-98
SPECIFICATIONS
Firing Capacities:
Model EHA & EHASR
0.75
– 3.00 gal/hr
105,000
– 420,000 Btu/hr Input
Model EH
3.00
– 6.00 gal/hr
420,000
– 840,000 Btu/hr Input
Fuel Pumps
Single Stage Standard
Electrical
Power Supply ……….120 Vac 60Hz, 230 Vac 60 Hz 1 Phase; optional 230 Vac 50 Hz 1 Phase
Motor ………………...3450 rpm, Automatic Reset Overload Protection
Ignition ……………….14,000 V secondary, Continuous Duty or Interrupted Duty
WAYNE COMBUSTION SYSTEMS
801 GLASGOW AVE.
FORT WAYNE, IN 46803
PHONE: (260) 425-9200
(855) WAYNECS
(800) 443-4625
FAX: (260) 424-0904
www.waynecombustion.com
MODEL
EH, EHA &
EHASR
OIL BURNERS
Fuels:
Use No.1 or No.2 heating oil (ASTM D-396),
Kerosene, Diesel (ASTM D975-18), JP8
Dimensions (
Standard
):
Height ……………………….…..…..12 1/2”
Width ……………………….…..……15 1/2”
Depth ………………………….…….. 8 1/4”
Center Line of Tube to Floor .........
8 1/16”
Mounting:
Rigid Flange, Adjustable Flange, or Pedestal
Mount
READ THIS MANUAL BEFORE USING THIS PRODUCT. FAILURE TO FOLLOW THE
INSTRUCTIONS AND SAFETY PRECAUTIONS IN THIS MANUAL CAN RESULT IN
SERIOUS INJURY OR DEATH. KEEP THIS MANUAL FOR FUTURE REFERENCE.
INSTALLER: LEAVE THIS MANUAL WITH THE END USER.
INSTALLATION OF THE BURNER MUST BE DONE BY A QUALIFIED INSTALLER IN
ACCORDANCE WITH REGULATIONS OF THE NATIONAL FIRE PROTECTION
AGENCY, NFPA NO. 31, AND IN COMPLETE ACCORDANCE WITH ALL LOCAL
CODES AND AUTHORITIES HAVING JURISDICTION.
A QUALIFIED INSTALLER IS THE PERSON WHO IS RESPONSIBLE FOR THE
INSTALLATION AND ADJUSTMENT OF THE EQUIPMENT AND WHO IS LICENSED TO
INSTALL OIL-BURNING EQUIPMENT IN ACCORDANCE WITH ALL CODES AND
ORDINANCES.