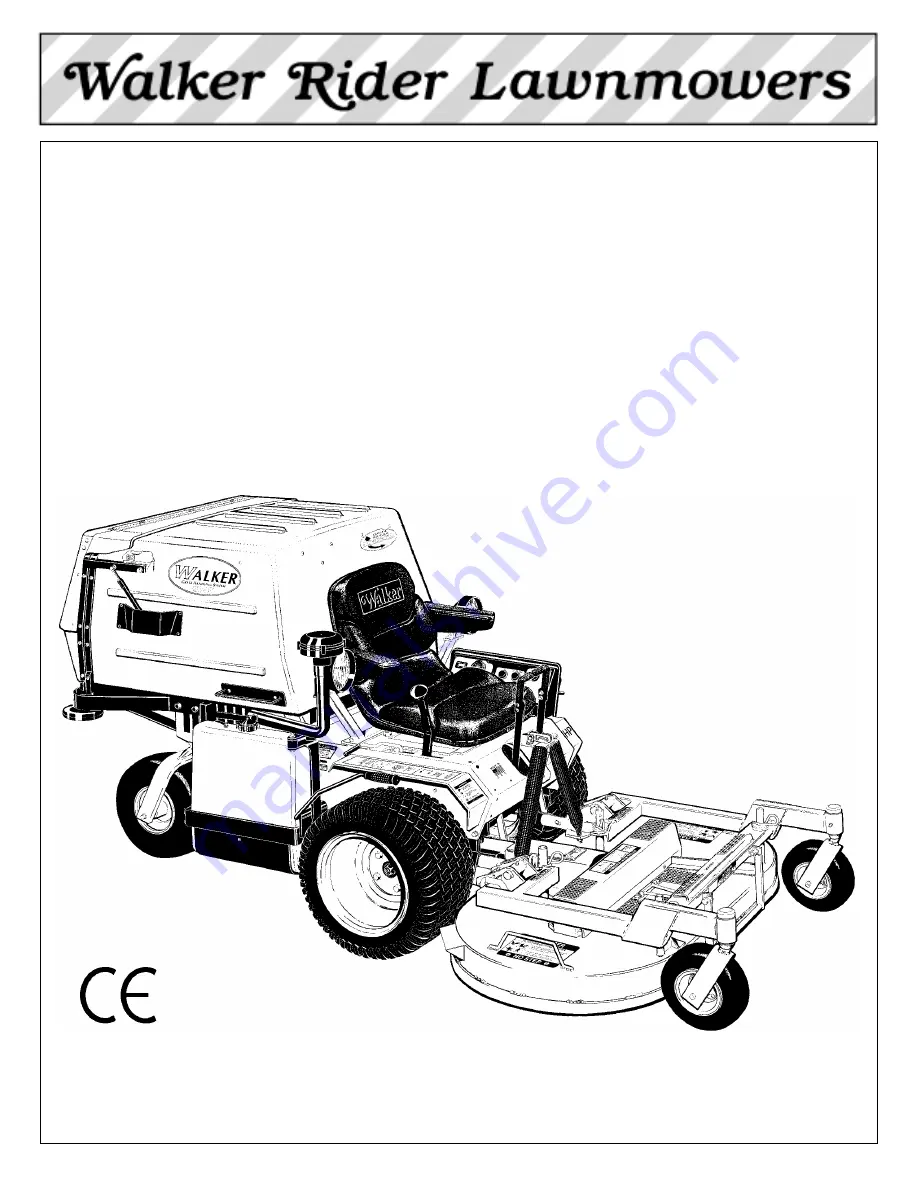
OWNER’S MANUAL
Safety, Assembly, Operating, and Maintenance Instructions
Model MT (20.0 HP)
Model MTL (25.0 HP)
Model MTEFI (26.0 HP)
(Covers 2004 Production)
Please Read and Save These Instructions
Effective Date: 01-01-04
For Safety, Read All Safety and Operation
P/N 8000-9
Instructions Prior to Operating Machine
Price $5.00
™