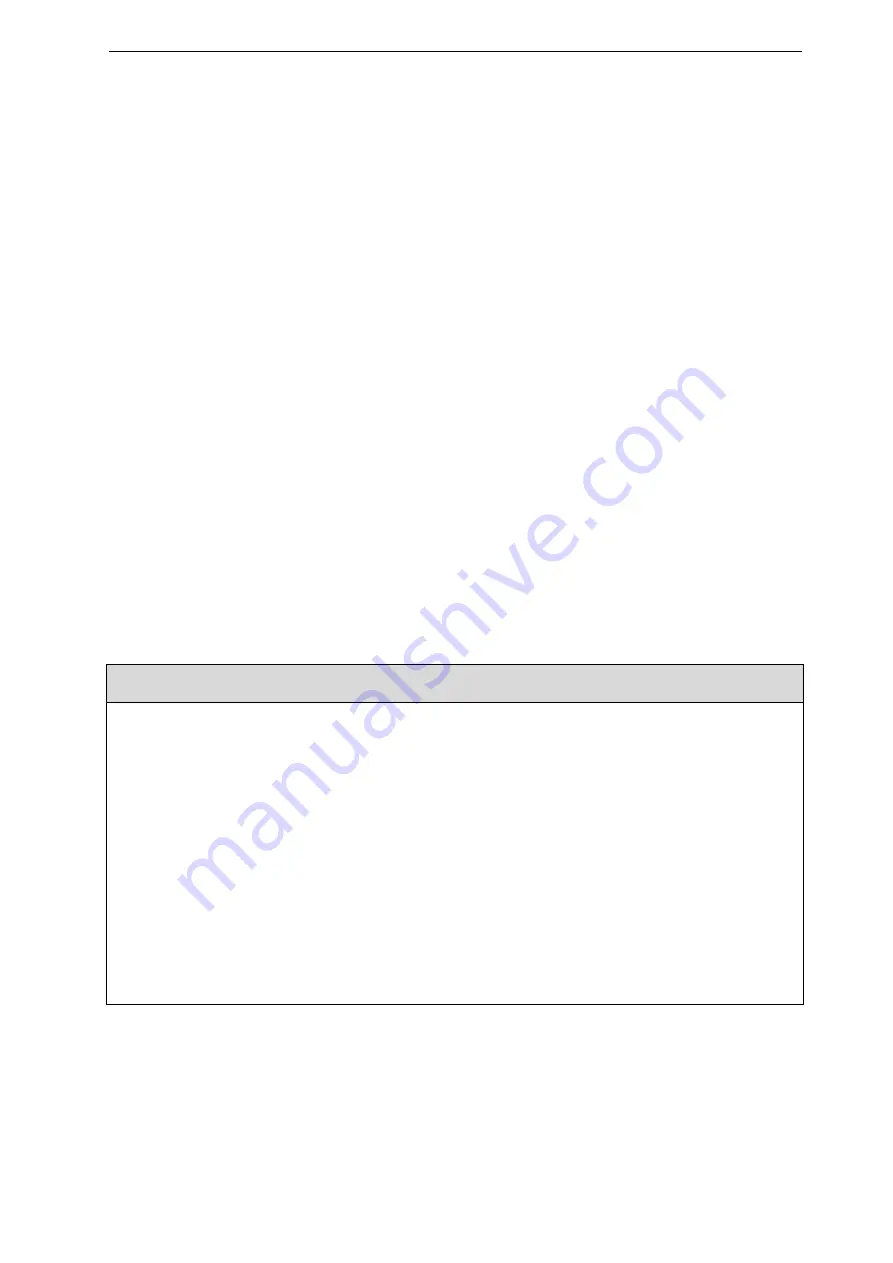
Preface
Thank you for purchasing the IR610 series high performance vector and torque control frequency
inverter
IR610 series with advanced functions, such as high performance vector control of induction motor,
user-programmable function and backstage monitoring software, variable communication and
supporting multiple PG cards etc. It is applicable to textile, papermaking, tension control, wire drawing
fans and pumps, machine tools, packaging, food and all kinds of automatic production equipment.Its
excellent performance is equivalent and competitive to most of international brand AC drives
This manual introduces functional characteristics and usage of IR610 series inverter, includes product
model selection, parameter settings, running and debugging, maintenance, checking, and so on. Please
be sure to read this manual carefully before operation. For equipment matching manufacturers, please
send this manual to your end user together with your devices, in order to facilitate the usage.
PRECAUTIONS
To describe the product details, the illustrations in the manual sometimes are under the state of
removing the outer housing or security covering. While using the product, please be sure to
mount the housing or covering as required, and operate in accordance with the contents of
manual.
The illustrations in this manual is only for explanation, may be different from the products you
ordered.
Committed to constantly improving the products and features will continue to upgrade, the
information provided is subject to change without notice.
Please contact with the regional agent or client service center directly of factory if there is any
questions during usage.
Summary of Contents for IR610 Series
Page 4: ......