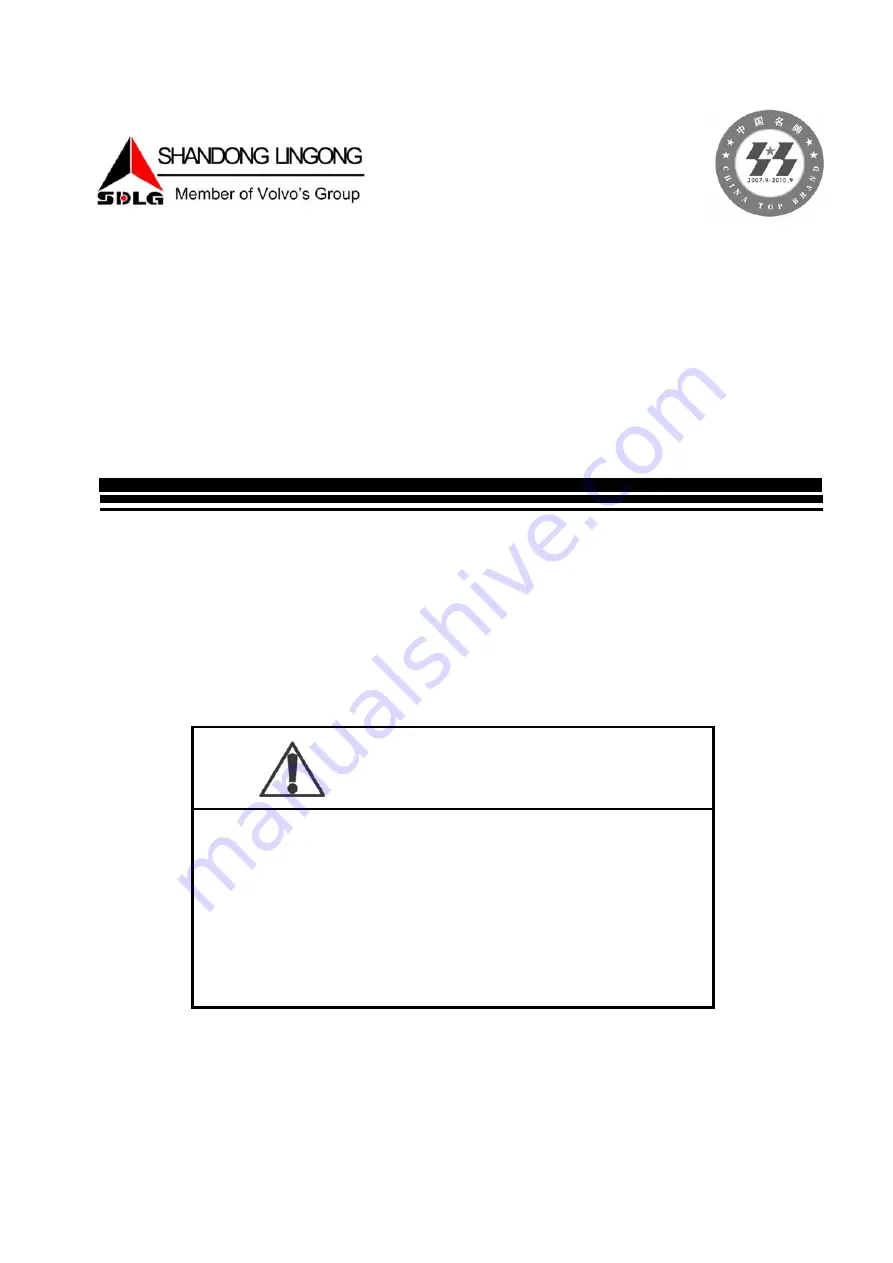
WARNING
Operators and maintenance persons should read this manual
carefully and understand these instructions before use to
avoid serious accident. For the convenience of relevant
people using this manual, it should be easily accessable and
kept in readable condition.
Operation & Maintenance Manual
LG936L
WHEEL LOADER
SHANDONG LINGONG CONSTRUCTION MACHINERY CO.
,
LTD