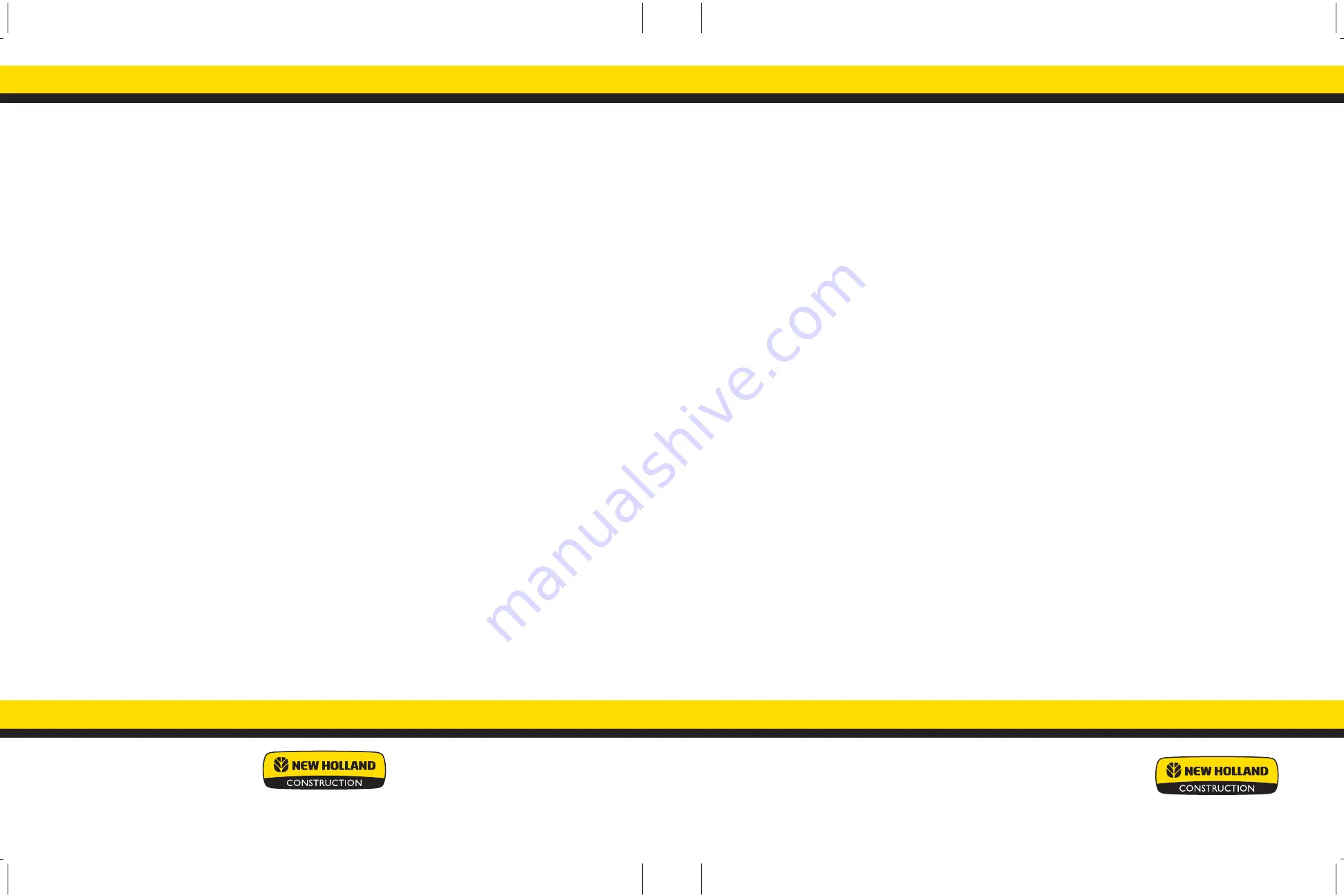
Part number 47851950
English
May 2015
Replaces part number 47712047
SERVICE MANUAL
Printed
in U.S.A.
© 2015 CNH Industrial America LLC. All Rights Reserved.
New
Holland is a trademark registered in the United States and many other countries,
owned by or licensed to CNH Industrial N.V., its subsidiaries or affiliates.
L221 / L228
Tier 4B (final)
200 Series Skid Steer Loader
L221 PIN NEM479941 and above; L228 PIN NFM401546 and above
C227 / C232
Tier 4B (final)
200 Series Compact Track Loader
C227 PIN NDM471836 and above; C232 PIN NFM402195 and above
Summary of Contents for 200 Series
Page 6: ...47851950 14 05 2015 Find manuals at https best manuals com ...
Page 7: ...INTRODUCTION 47851950 14 05 2015 1 Find manuals at https best manuals com ...
Page 12: ...INTRODUCTION Safety rules C227 NA C232 NA L221 NA L228 BT09A213 1 47851950 14 05 2015 6 ...
Page 51: ...This as a preview PDF file from best manuals com Download full PDF manual at best manuals com ...