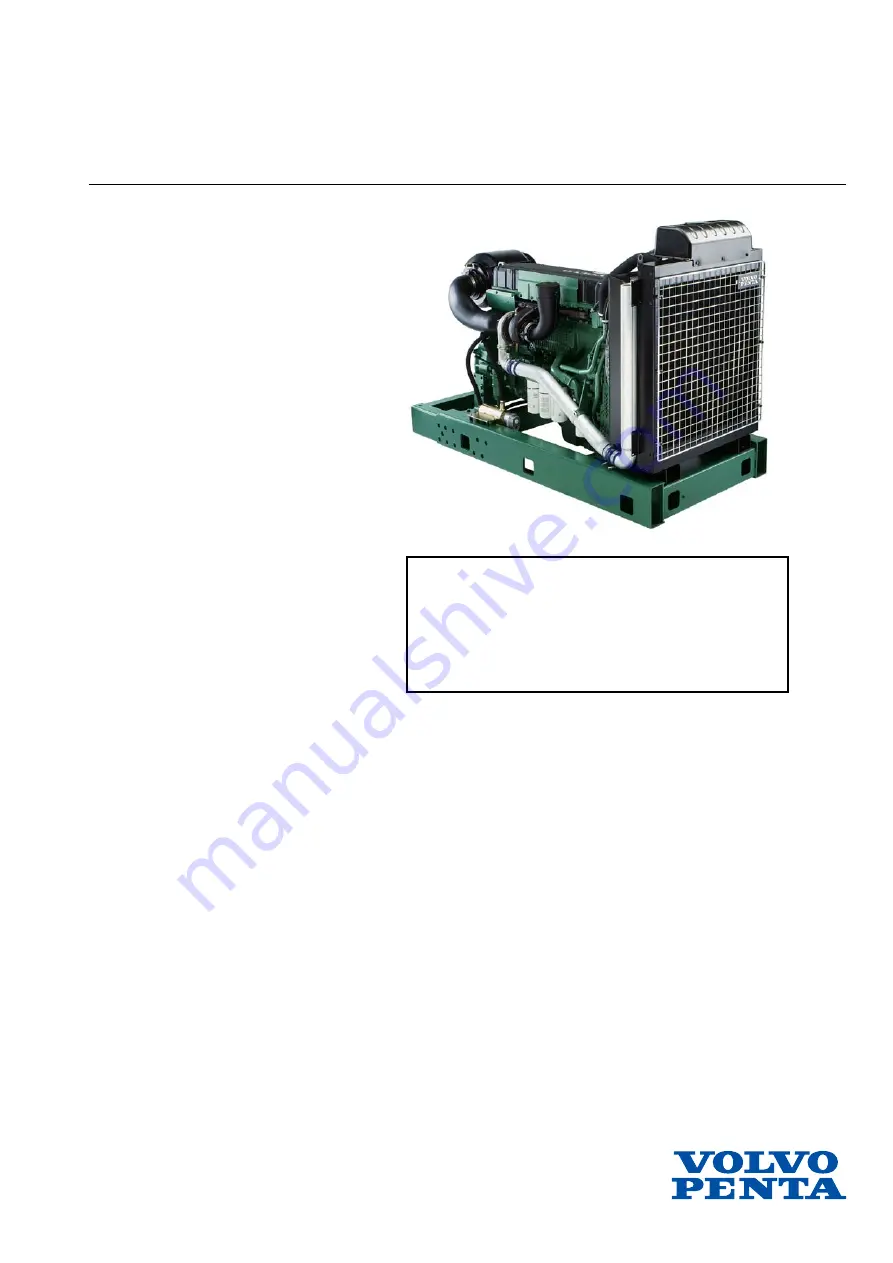
The TAD1242GE is a powerful, reliable
and economical Generating Set Diesel
Engine built on the dependable in-line six
design.
Durability & low noise
Designed for easiest, fastest and most
economical installation. Well-balanced to
produce smooth and vibration-free opera-
tion with low noise level.
To maintain a controlled working tem-
perature in cylinders and combustion
chambers, the engine is equipped with
piston cooling. The engine is also fitted
with replaceable cylinder liners and valve
seats/guides to ensure maximum durabil-
ity and service life of the engine.
Low exhaust emission
The state of the art, high-tech injection
and charging system with low internal
losses contributes to excellent combus-
tion and low fuel consumption.
The TAD1242GE complies with EU
Stage 2 and TA-Luft -50% exhaust emis-
sion regulations.
Easy service & maintenance
Easily accessible service and mainte-
nance points contribute to the ease of
service of the engine.
Technical description:
Engine and block
– Optimized cast iron cylinder block with opti-
mum distribution of forces without the block
being unnessarily heavy.
– Wet, replaceable cylinder liners
– Piston cooling for low piston temperature
and reduced ring temperature
– Tapered connecting rods for reduce risk of
piston cracking
– Crankshaft induction hardened bearing
surfaces and fillets with seven bearings for
moderate load on main and high-end bear-
ings
– Case hardened and Nitrocarburized trans-
mission gears for heavy duty operation
– Keystone top compression rings for long
service life
– Viscous type crankshaft vibration dampers to
withstand single bearing alternator torsional
vibrations
– Replaceable valve guides and valve seats
– Over head camshaft and four valves per cyl-
inder
Lubrication system
– Full flow oil cooler
– Full flow disposable spin-on oil filter, for ex-
tra high filtration
– The lubricating oil level can be measured
during operation
– Gear type lubricating oil pump, gear driven
by the transmission
Fuel system
– Non-return fuel valve
– Electronic Unit Injectors
– Fuel prefilter with water separator and water-
in-fuel indicator / alarm
– Gear driven low-pressure fuel pump
– Fine fuel filter with manual feed pump and
fuel pressure switch
– Fuel shut-off valve, electrically operated
Cooling system
– Efficient cooling with accurate coolant con-
trol through a water distribution duct in the
cylinder block. Reliable sleeve thermostat
with minimum pressure drop
– Gear driven, maintenance-free coolant pump
with high degree of efficiency
– Coolant filter as standard
Turbo charger
– Efficient and reliable turbo charger
– Extra oil filter for the turbo charger
Electrical system
– Electronical Diesel Control III (EDCIII), an
electronically controlled processing system
which optimizes engine performance. It also
includes advanced facilities for diagnostics
and fault tracing
– Three different ways for the customer to
connect his controls and instrument to the
engine. CAN SAE J1939 interface, CIU
(Control interface unit) and Stand alone
connections.
– Sensors for oil pressure, oil temp, boost
pressure, boost temp, coolant temp, fuel
temp, water in fuel, fuel pressure and two
speed sensors.
Features
– Maintained performance, air temp 40°C
– Cooling system (55°C)
– Fully electronic with Volvo Penta EDC III
– Dual frequency switch (between 1500 rpm and 1800 rpm)
– High power density
– Emission compliant
– Low noise levels
– Gen Pac configuration
VOLVO PENTA GENSET ENGINE
TAD1242GE
1500 rpm, 387 kW (526 hp) – 1800 rpm, 430 kW (585 hp)