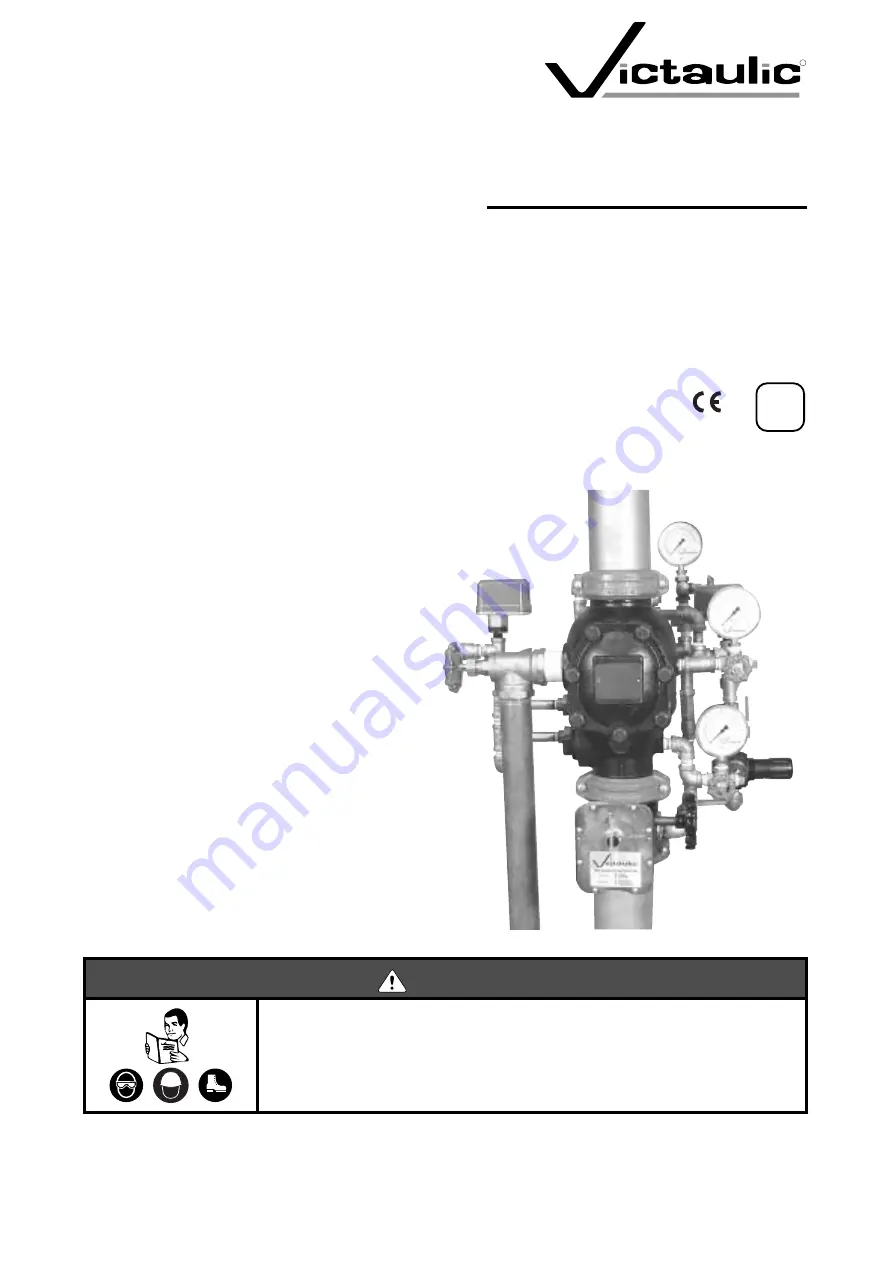
R
Installation,
Maintenance, & Testing Manual
Series 756
FireLock
®
European
Dry Valve Stations
Hang these instructions on the
installed valve for easy future reference.
WARNING
Failure to follow instructions and warnings could cause product failure, resulting in serious personal injury and/or property
damage.
• Read and understand all instructions before attempting to install, maintain, or test any Victaulic piping products.
• Wear safety glasses, hardhat, and foot protection.
If you need additional copies of any literature, or if you have any questions about the safe installation and operation of this
product, contact Victaulic Company of Europe, Prijkelstraat 36, 9810 Nazareth, Belgium, Phone: 32-9-381-1500.
VdS
0786