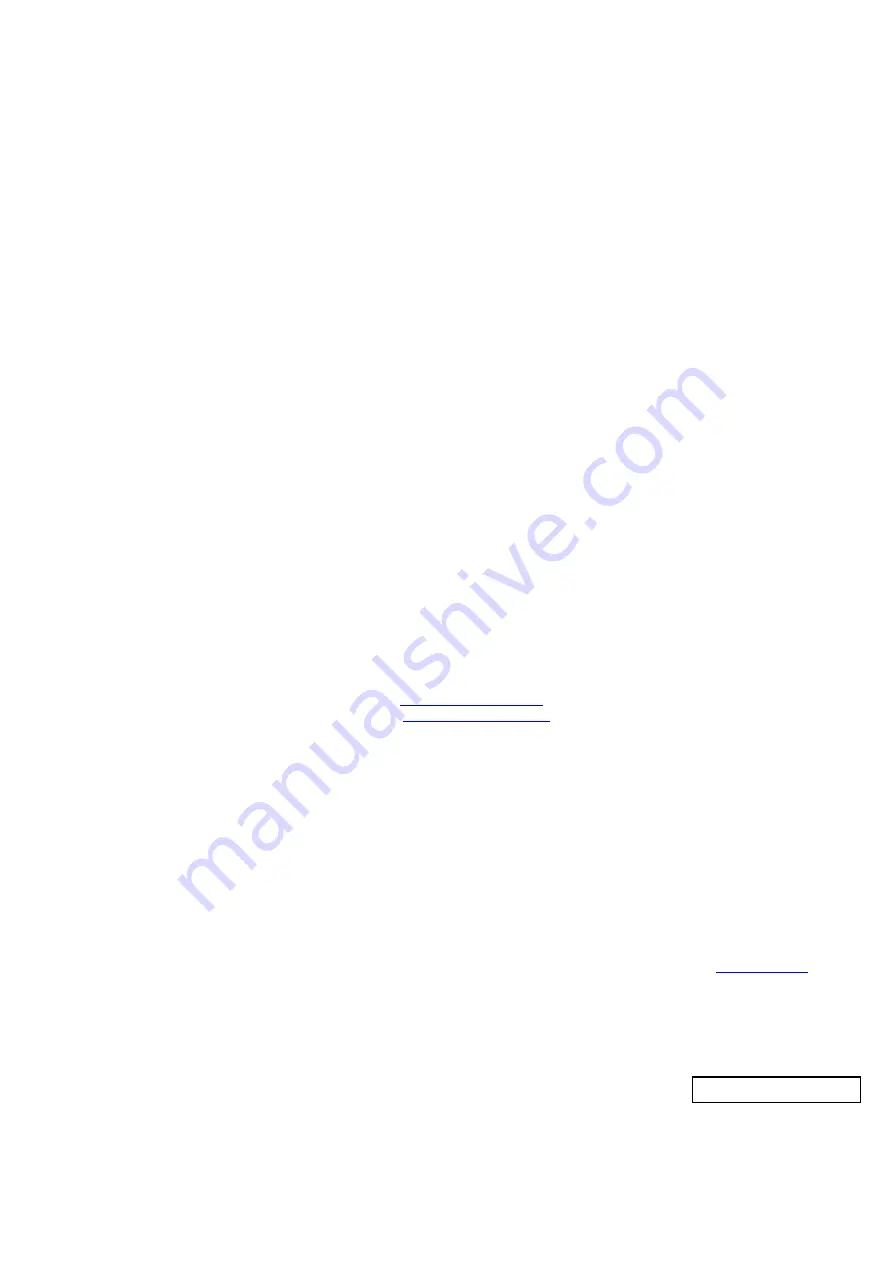
3022CS AUTOMATIC UNIT
1
INSTRUCTIONS FOR “VIBEMAC 3022WB406” AUTOMATIC UNIT WITH
LS01PMG DIGITAL PANEL
INTRODUCTION
Thank you for buying this industrial sewing machine of
VI.BE.MAC. S.p.A.
Before starting to operate with this automatic unit, please read carefully the following instructions so as to help you to
understand the working of the machine.
These will explain you the working system that must be followed according to the current regulations.
•
Any part of this manual can be copied or transcribed without forwarding the application to
VI.BE.MAC. S.p.A.
•
The content of this handbook can be subject to alterations without notice.
To ask for a new manual or have explanations on every information or technical note presented in this volume, please
contact:
VI.BE.MAC. S.p.A.
TECHNICAL DEPARTMENT
Via Monte Pastello 7/ I
37057 S. GIOVANNI LUPATOTO
(VERONA) - ITALIA
Phone +39 045 8778151
Fax +39 045 8779024
E-mail:
Web site:
http://www.vibemac.com
In case of followings improvements, some incongruities on technical notes might appear in this manual. Therefore, we
suggest You always to contact our Tech. Dept. to check if new version of this manual or new deepening are available.
“Suggestions on possible mistakes and signalling to improve this handbook will always be welcomed”
Morandin Dario
3022 406 001 A Version
Summary of Contents for 3022 Series
Page 60: ...3022CS AUTOMATIC UNIT 60...
Page 61: ...3022CS AUTOMATIC UNIT 61...