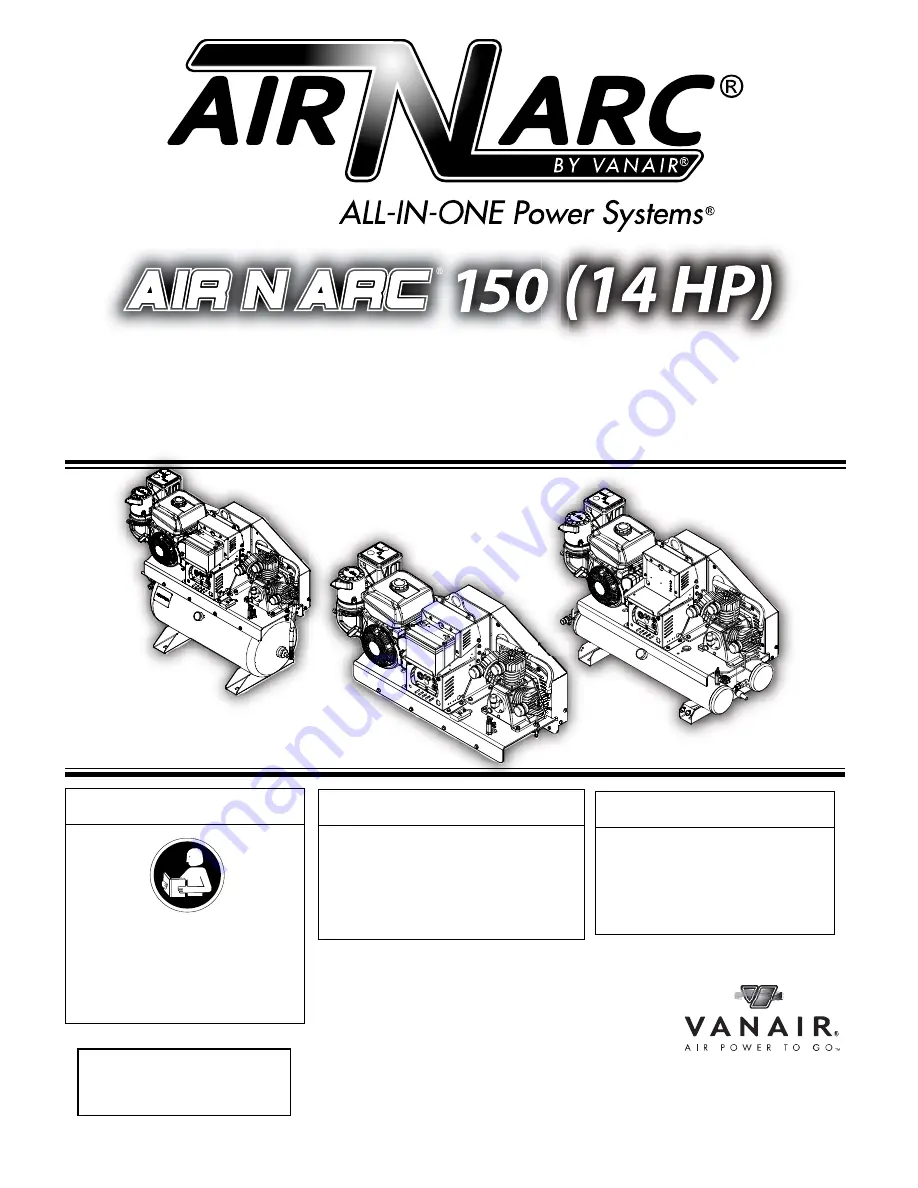
ALL-IN-ONE POWER SYSTEMS
®
WELDER • GENERATOR • AIR COMPRESSOR • BATTERY BOOSTER
OPERATION MANUAL & PARTS LIST
©2014 Vanair Manufacturing, Inc.
All rights reserved
090051-OP_r0
Effective Date:
2-2014
NOTE
Read this manual before installing,
operating or servicing this
equipment. Failure to comply with
the operation and maintenance
instructions in this manual WILL
VOID THE EQUIPMENT WARRANTY.
NOTE
Use only Genuine Vanair Parts.
Inspect and replace damaged
components before operation.
Substituting non-Vanair
components WILL VOID THE
COMPRESSOR WARRANTY!
Vanair Manufacturing, Inc.
10896 West 300 North
Michigan City, IN 46360
Phone: (219) 879-5100
(800) 526-8817
Service Fax: (219) 879-5335
Parts Fax: (219) 879-5340
Sales Fax: (219) 879-5800
www.vanair.com
NOTE
Making unauthorized modifications to
the system components WILL VOID THE
WARRANTY!
Always inform Vanair Manufacturing,
Inc. before beginning any changes to the
Air N Arc system.
KEEP THE MANUAL
WITH THE VEHICLE