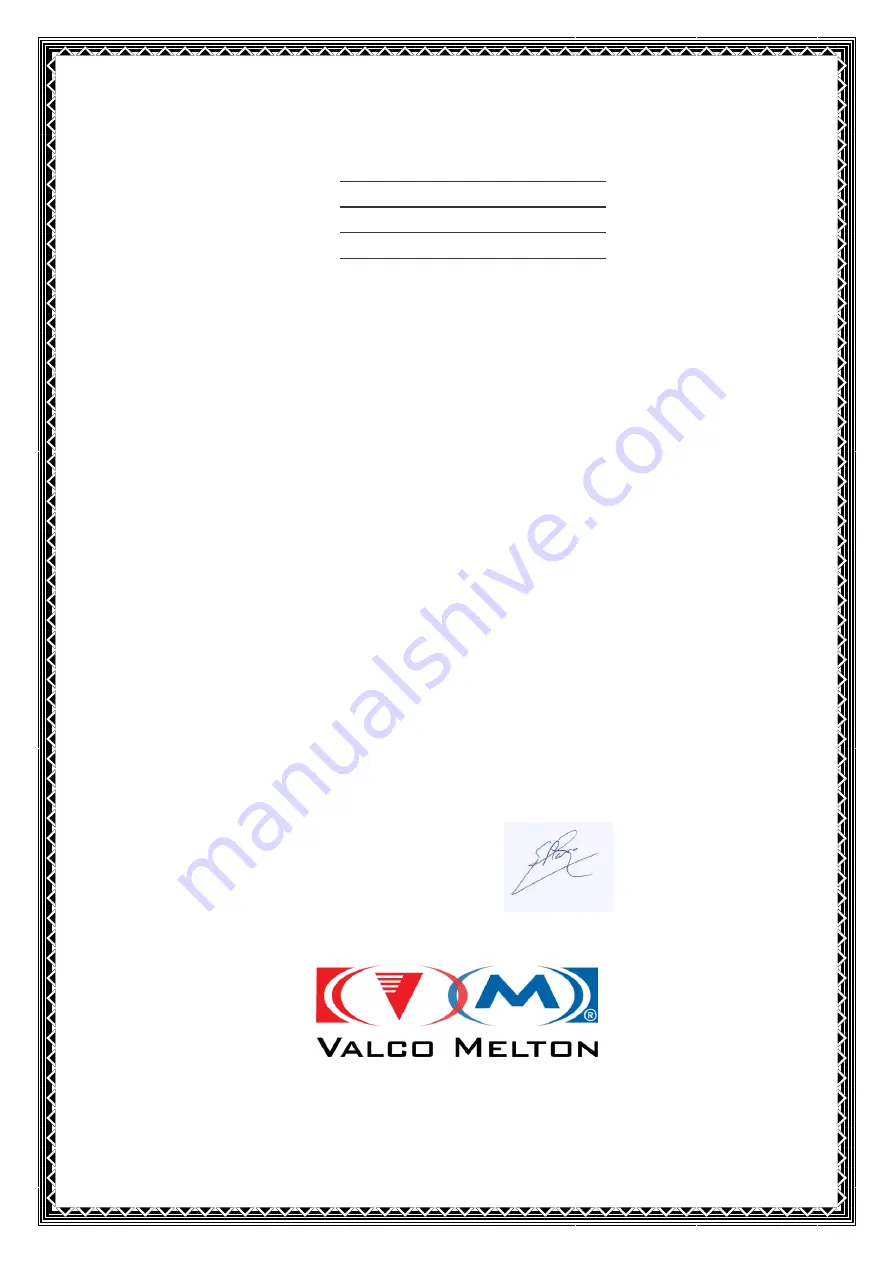
Declaration of conformity
The product
:
Model nº:
Serial nº:
Year of manufacture
:
Described in the enclosed documentation is in conformity with:
Directive 2006/42/EC of 29 December 2009 which replaces Directive
98/37/EC of 22 June 1998 on
the approximation of the laws of the
Member States relating to machinery
, which regroups Directives
89/392/EEC of 14 June 1989, 91/368/EEC of 20 June 1991, 93/44/EEC of
14 June 1993 and 93/68/EEC of 22 July 1993. Directive applicable to
standard EN ISO 12100-1 and EN ISO 12100-2, related to
safety of
machinery
; standard EN ISO 14121-1 and EN ISO 14121-2, related to
safety of machinery. Risk assessment
; standard UNE-EN 60204-1, related
to
safety of machinery. Electrical equipment of machines
; standard UNE-
EN 61310-1, UNE-EN 61310-2 and UNE-EN 61310-3, related to
safety of
machinery. Indication, marking and actuation.
Directive 2006/95/CE of 12 December 2006 which replaces Directive
73/23/EEC of 19 February 1973 on electrical equipment.
Directive 2004/108/EC of 20 July 2007 which replaces Directive
89/336/EEC of 3 May 1989 on Electromagnetic Compatibility.
Directive 93/68/EEC of 22 July 1993 which modifies 73/23/EEC and
Directive 89/336/EEC.
Hoses are factory tested at 100 bars and at 220ºC.
within the scope of the specifications indicated in the chapter describing the equipment
with a B1 risk level. Since it is intended to form part of a set of machines which, to obtain
a result, are arranged and connected to perform together, it cannot be operated until the
set of machines has been declared in conformity with the applicable Directives by the
person responsible for the final assembly.
Orcoyen, on : / /
Signed.:______________________
Gonzalo Marco, Managing director.
Polígono Industrial Agustinos, calle G, nave D-34
Tel.: +34.948.321.580 Fax: +34.948.326.584
31160 ORCOYEN (Navarra) SPAIN