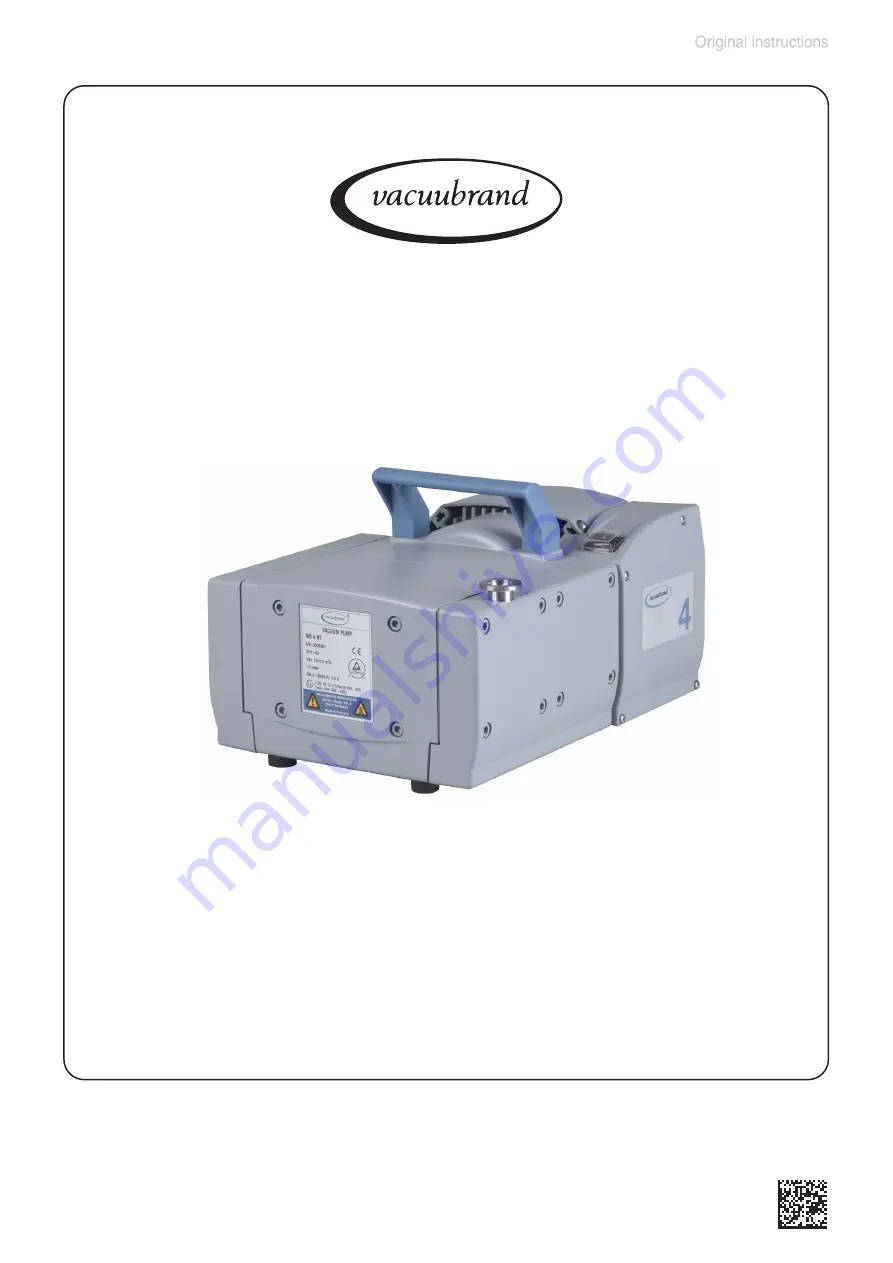
page 1 of 88
Instructions for use
Technology for Vacuum Systems
Diaphragm pumps
ME 2 NT - ME 4 NT - ME 4S NT
MZ 2 NT - MZ 2D NT - MZ 2S NT
ME 8 NT - ME 8S NT - MD 4 NT - MD 4S NT - MV 2 NT
ME 4R NT
MD 4CRL NT
Summary of Contents for ME 2 NT
Page 34: ...page 34 of 88 ME 4 NT 1 5 3 2 6 4 ME 4 NT ME 4S NT 1 5 3 2 6 4 fig ME 4 NT ...
Page 35: ...page 35 of 88 ME 4R NT 9 5 3 6 12 8 10 11 10 4 13 MZ 2 NT MZ 2S NT fig MZ 2 NT 5 3 2 6 4 1 ...
Page 36: ...page 36 of 88 MZ 2D NT 5 3 2 6 4 ME 8 NT ME 8S NT 2 5 3 2 6 4 1 1 ...
Page 37: ...page 37 of 88 6 MD 4 NT MV 2 NT fig MD 4 NT 1 5 3 4 2 7 MV 2 NT 1 5 3 4 2 7 6 14 MD 4S NT ...
Page 38: ...page 38 of 88 MD 4CRL NT 5 3 2 7 6 14 4 1 ...
Page 61: ...page 61 of 88 4 5 6 Clean 20696877 20696860 20696861 20696862 20696868 20696859 20696870 ...
Page 62: ...page 62 of 88 7 8 9 1 2 ...
Page 64: ...page 64 of 88 12 13 14 Pay attention to washers Assemble same number and thick ness ...
Page 66: ...page 66 of 88 18 19 20 23120788 ME 8 NT MD 4 NT MV 2 NT ...
Page 67: ...page 67 of 88 21 22 23 ...
Page 70: ...page 70 of 88 1 20 17 2 3 Checking diaphragms and valves MZ 2D NT 5 4x 17 mm 20 mm ...
Page 74: ...page 74 of 88 10 size 2 1x Replacing the valves and assembling the pump heads MZ 2D NT 11 12 ...
Page 75: ...page 75 of 88 13 14 15 ...