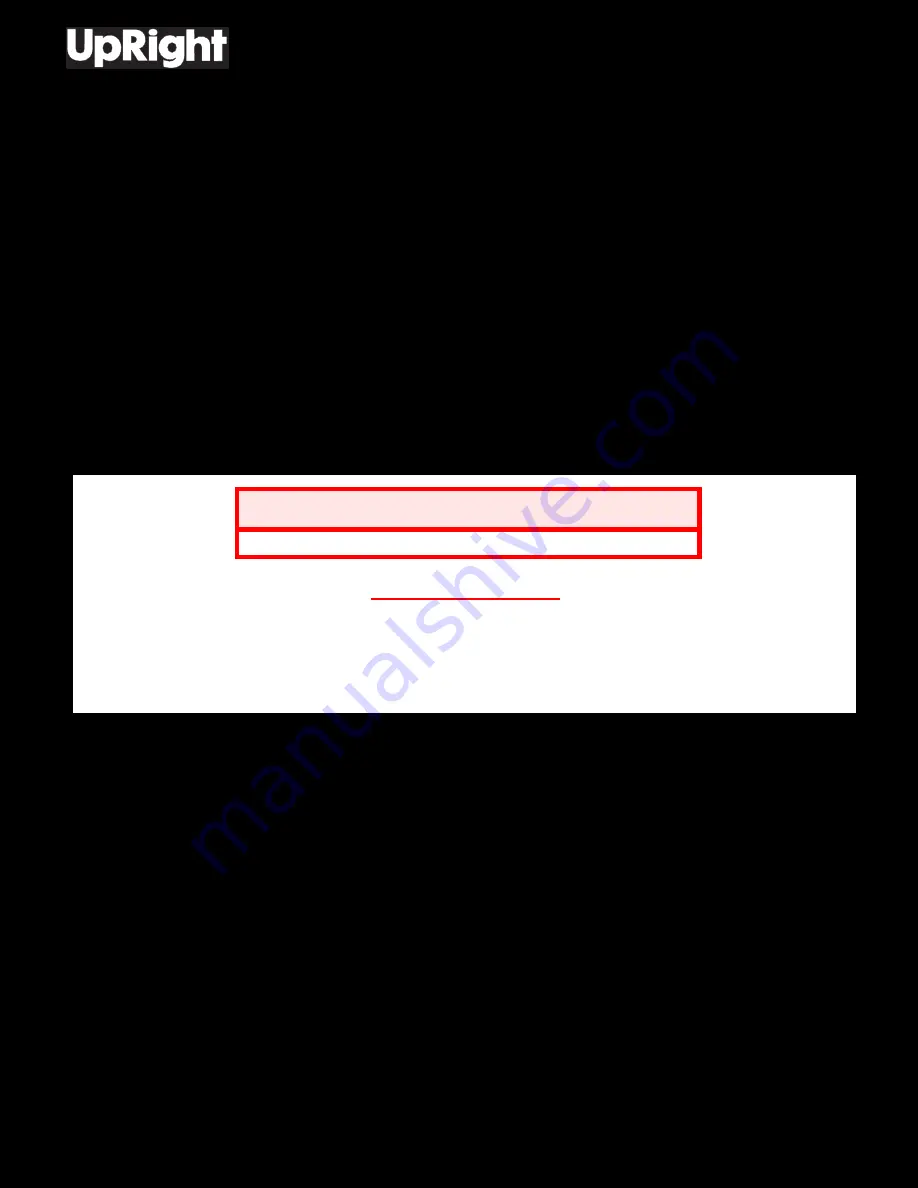
Operator Manual
X-Series
SERIAL NO. 20000 to Current
WARNING
All personnel shall carefully read, understand and follow all safety rules,
operating instructions, and the Scaffold Industry Association’s
MANUAL OF RESPONSIBILITIES of ANSI A92.6-1999 before performing
maintenance on or operating any UpRight Aerial Work Platform.
P/N 114110-000