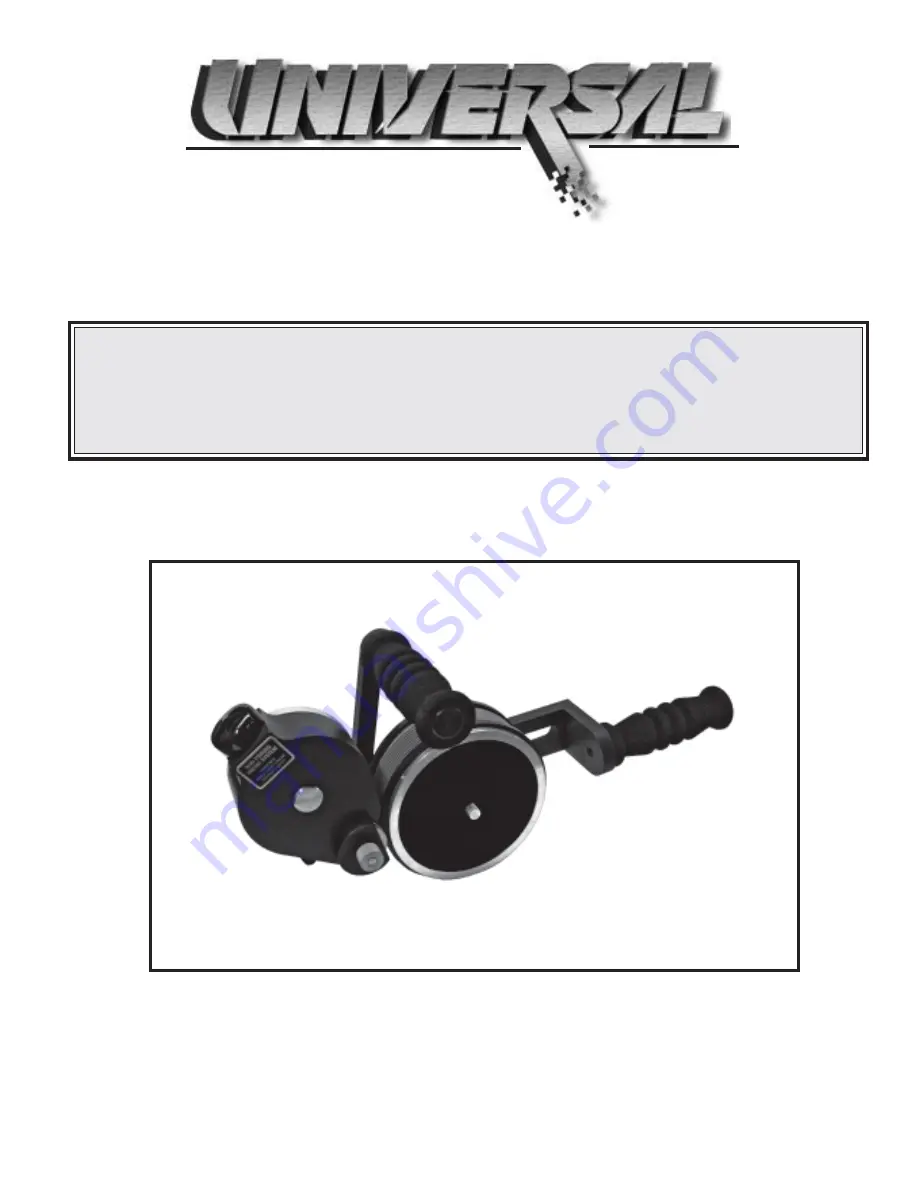
1
NON-POROUS
LARGE CAPACITY HAND PRINTERS
ALL MODELS
UNIVERSAL STENCILING & MARKING SYSTEMS, INC.
P.O. BOX 871 - ST. PETERSBURG, FLORIDA 33731 USA
PH: (727) 894-3027 FAX: (727) 821-7944
E-Mail: [email protected] Website: www.universal-marking.com
STENCILING & MARKING SYSTEMS
HPLNP-22115
OWNER’S MANUAL
INSTALLATION - OPERATION - MAINTENANCE