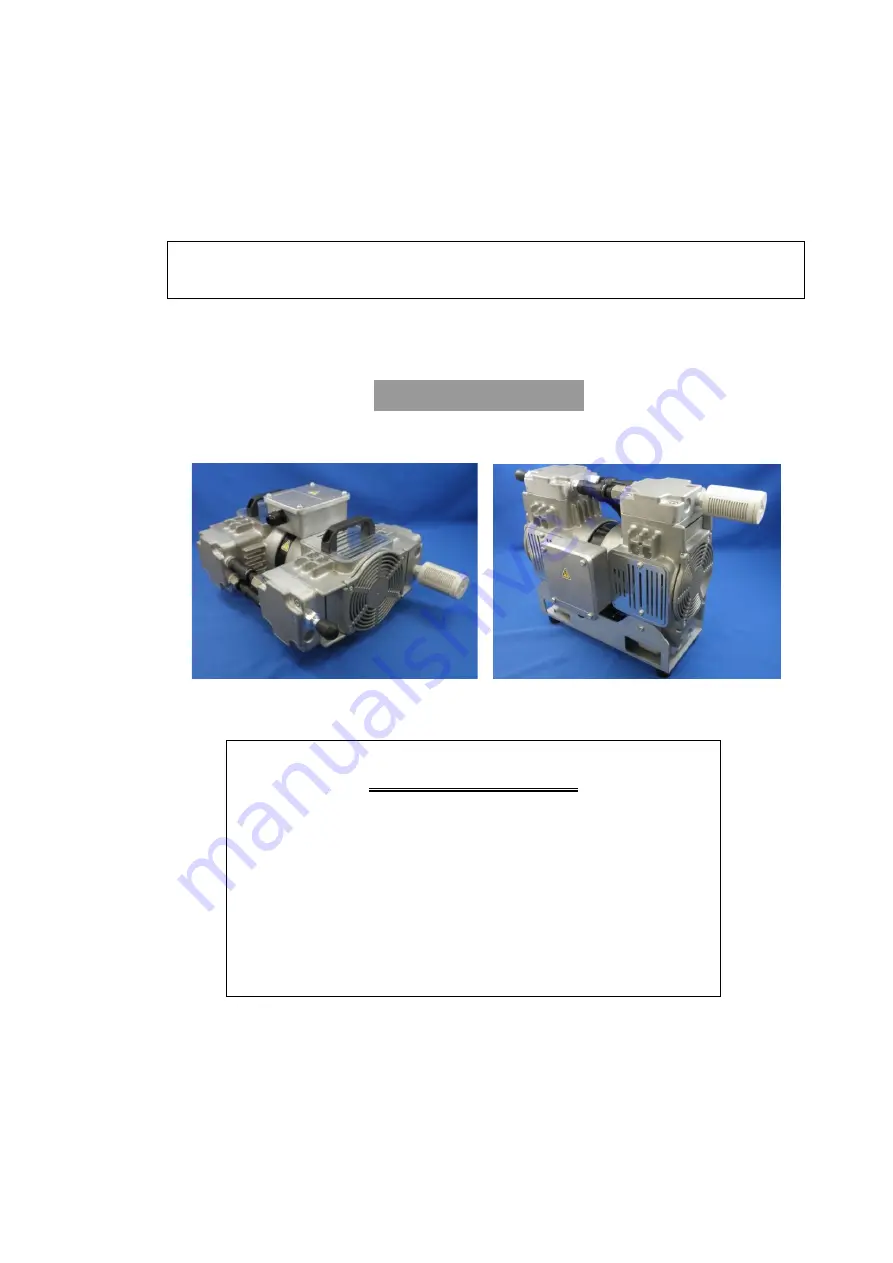
No. 20D00-2-01-3
Original instructions
INSTRUCTION MANUAL
Oscillating Piston Dry Vacuum Pump
DOP-301SB/SVB
Request to Users
Please read this manual thoroughly to ensure safe and
effective use of the equipment.
Keep this manual in a safe place.
Due to periodic improvements in performance, the
equipment described in this manual is subject to changes
in dimensions and specifications without prior notice.
ULVAC
KIKO, Inc.
DOP-301SB
DOP-301SVB