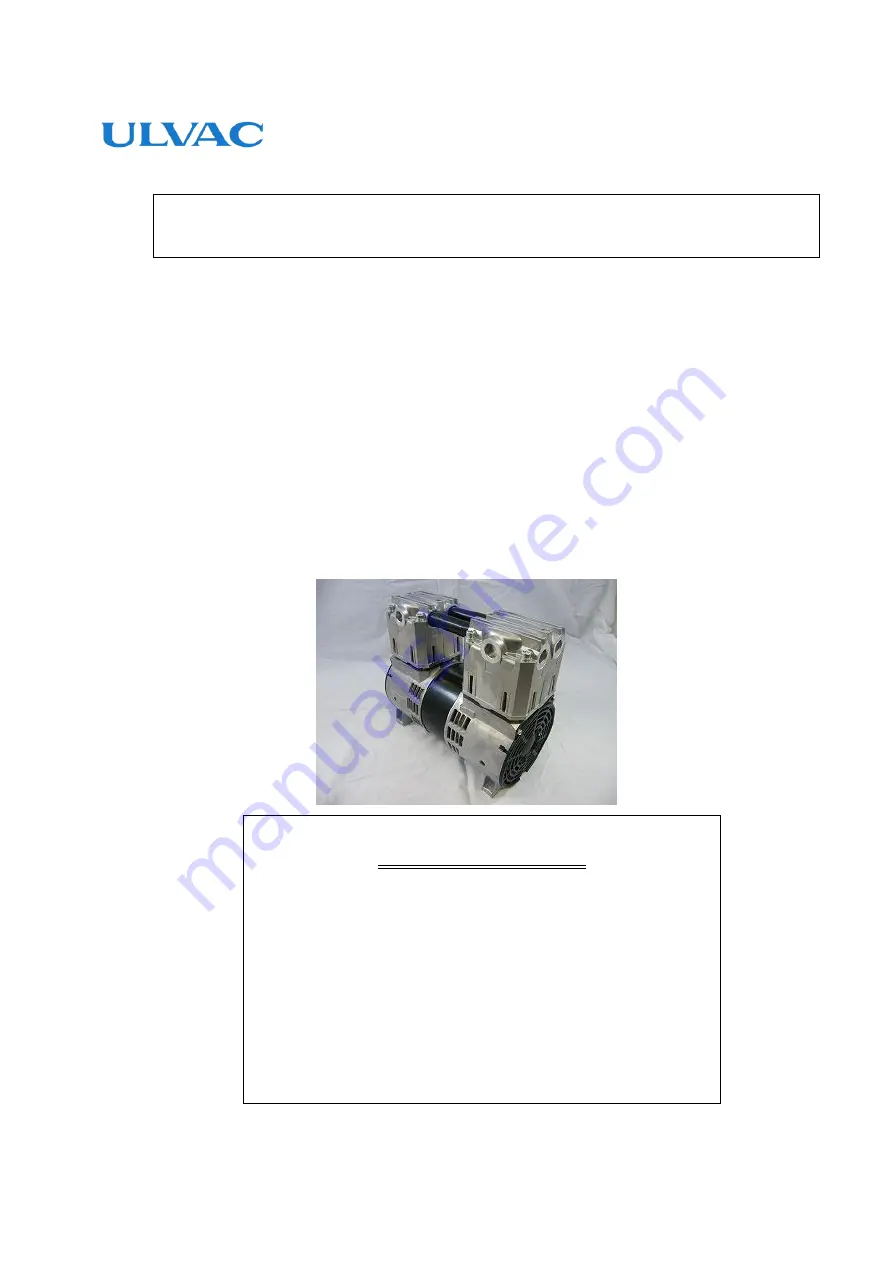
No
.
20025-2-01-5
Original Instructions
INSTRUCTION MANUAL
Oscillating Piston Dry Vacuum Pump
DOP-181S series
Model
DOP-181SA
/
DOP-181SB
DOP-181SC
/
DOP-181SD
DOP-181SE
Request to Users
Please read this manual thoroughly to ensure safe and
effective use of the equipment.
Keep this manual in a safe place.
Due to periodic improvements in performance,
the equipment described in this manual is subject to
changes in dimensions and specifications without prior
notice.
ULVAC
KIKO, Inc.