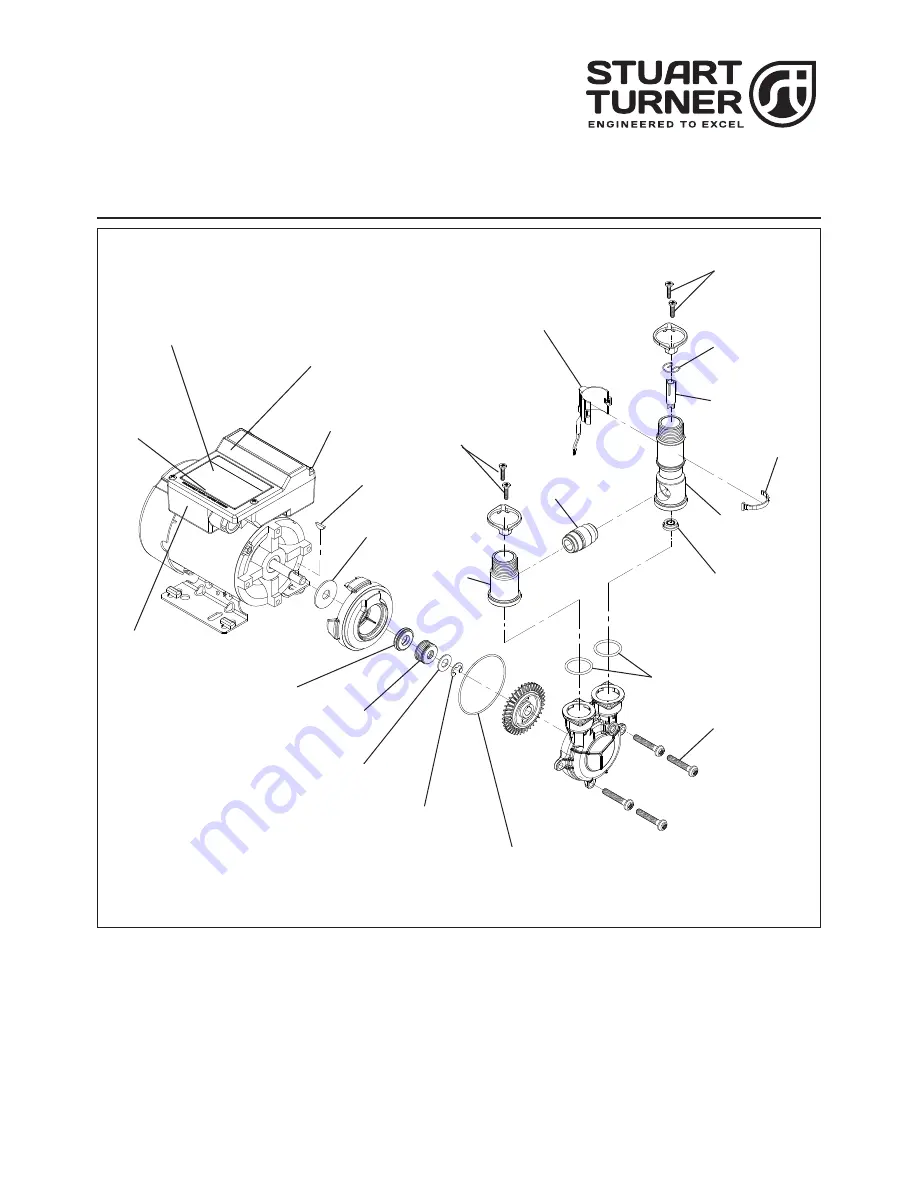
Cont ...
INSTALLATION INSTRUCTIONS
SERVICE KIT -
FLOMATE, MBF 12 (Pre-November 2017) Part No.
28457
Note: 1) Items 16, 23, 24 are pre-assemble parts, see relevant section for detailed instructions.
2) See relevant section for detailed instructions.
Fig. 1
20 (Section 3)
Capacitor (not shown)
17 (Section 5)
PCB
(not shown)
19 (Section 3 & 5)
Adhesive foam pad
(not shown)
1 (Section 1)
Woodruff key
7 (Section 1)
‘O’-ring (ID 66.4)
5 (Section 1)
Washer (OD ¾)
8 (Section 1)
Screws M6 x 35 mm
6 (Section 1)
Circlip
4 (Section 1)
Rotary seal
3 (Section 1)
Seal
counterface
18 (Section 4)
Strainer relief bush
(not shown)
21 (Section 4)
Reed switch
12 (Section 2)
Screws (M4 x 16 mm)
16 (Section 2)
Non return
valve assembly
13 (Section 2 & 4)
Reed switch tie wrap
10 (Section 2)
Clip
11 (Section 2)
Magnetic float
14 (Section 2)
Flow regulator
15 (Section 2)
‘O’-ring (ID 24.6)
12
23 (Section 2)
Inlet assembly
2 (Section 1)
Thrower
22 (Sections 3, 4 & 5)
Screws (K40 x 16 mm)
24 (Section 2)
Outlet assembly