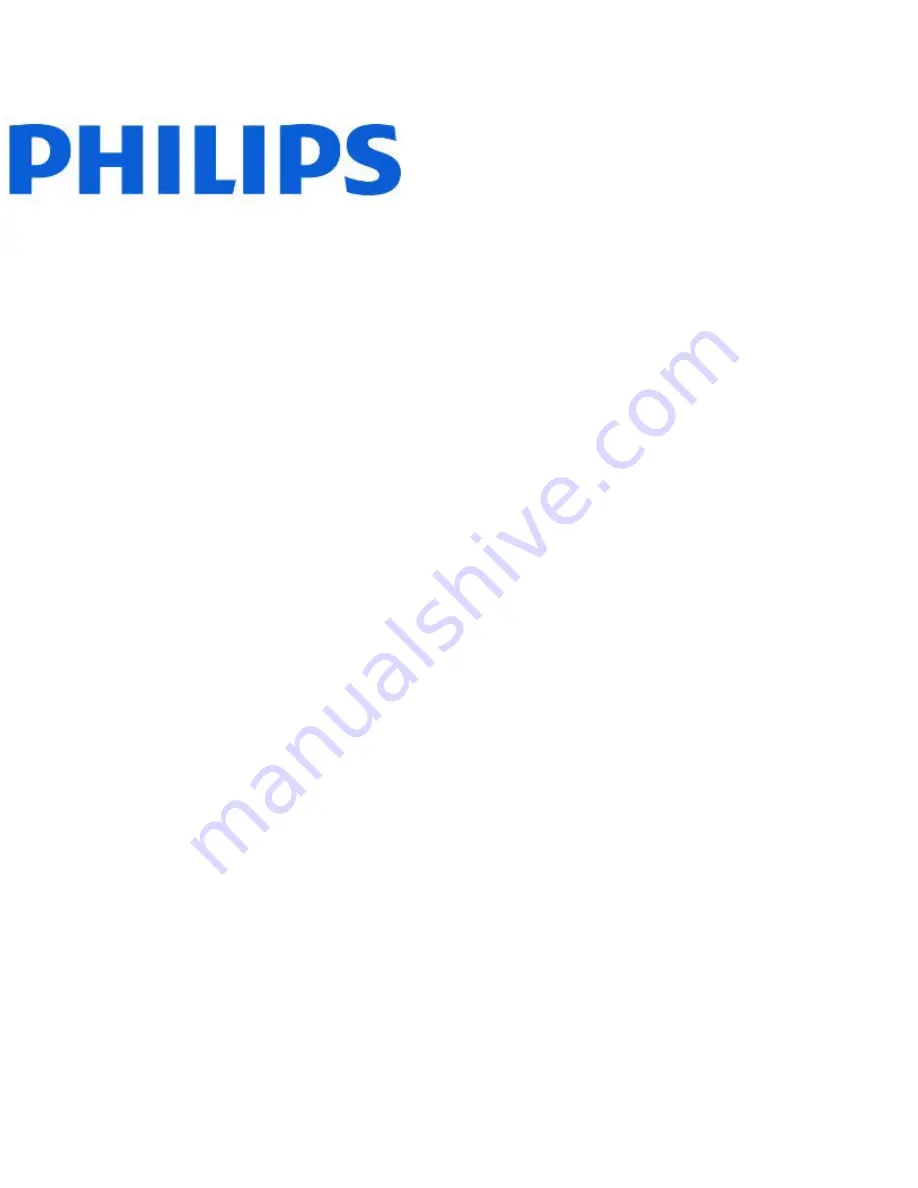
Legal Notice:
Use of the document and the information contained in it is strictly reserved for current Philips
personnel and Philips customers who have a current and valid license from Philips for use by
the customer’s designated in-house service employee on equipment located at the
customer’s designated site. This document and the information contained in it is proprietary
and confidential information of Philips Healthcare ("Philips") and may not be reproduced,
copied in whole or in part, adapted, modified, disclosed to others, or disseminated without
the prior written permission of the Philips Legal Department. This document is intended to
be (a.) used by customers and is licensed to them as part of their Philips equipment
purchase or (b.) used to meet regulatory commitments as required by the FDA under 21
CFR 1020.30 (and any amendments to it) and other local regulatory requirements. Use of
this document by unauthorized persons is strictly prohibited.
This document must be returned to Philips when the user is no longer licensed and in any
event upon Philips’ first written request. PHILIPS PROVIDES THIS DOCUMENT WITHOUT
WARRANTY OF ANY KIND, EITHER IMPLIED OR EXPRESSED, INCLUDING, BUT NOT
LIMITED TO, THE IMPLIED WARRANTIES OF MERCHANTABILITY AND FITNESS FOR A
PARTICULAR PURPOSE. Philips has taken care to ensure the accuracy of the information
contained within this document. However, Philips assumes no liability for errors or
omissions, and reserves the right to make changes without further notice to any products
herein to improve reliability, function, or design. Philips may make improvements or changes
in the product(s) described in this document at any time.
CSIP Level 0
© 2013 Koninklijke Philips N.V.
All rights reserved.
Summary of Contents for FVX325
Page 3: ......
Page 11: ...TRACKMASTER viii FVX TMX Series Service Manual August 2006...
Page 15: ...TRACKMASTER 1 4 FVX TMX Series Service Manual August 2006...
Page 19: ...TRACKMASTER 3 2 FVX TMX Series Service Manual August 2006 Power Supply Relay Board Detail...
Page 31: ...TRACKMASTER 4 12 FVX TMX Series Service Manual August 2006...
Page 90: ...TRACKMASTER August 2006 FVX TMX Series Service Manual 8 9 FVX Series TMX Series...
Page 92: ...TRACKMASTER August 2006 FVX TMX Series Service Manual 8 11 FVX Series TMX Series...
Page 102: ...TRACKMASTER August 2006 FVX TMX Series Service Manual 8 21 FVX Series...
Page 104: ...TRACKMASTER August 2006 FVX TMX Series Service Manual 8 23 TMX Series...
Page 106: ...TRACKMASTER August 2006 FVX TMX Series Service Manual 8 25 FVX TMX Series...
Page 108: ...TRACKMASTER August 2006 FVX TMX Series Service Manual 8 27 FVX Series...
Page 110: ...TRACKMASTER August 2006 FVX TMX Series Service Manual 8 29 TMX Series...
Page 113: ...TRACKMASTER 8 32 FVX TMX Series Service Manual August 2006 FVX Series...
Page 115: ...TRACKMASTER 8 34 FVX TMX Series Service Manual August 2006 TMX Series...
Page 126: ...TRACKMASTER August 2006 FVX TMX Series Service Manual 10 3 Power Supply Board FG302...
Page 127: ...TRACKMASTER 10 4 FVX TMX Series Service Manual August 2006...
Page 139: ...TRACKMASTER 11 12 FVX TMX Series Service Manual August 2006...
Page 158: ...TRACKMASTER August 2006 FVX TMX Series Service Manual 13 17 FVX325 Series Frame Assembly...
Page 160: ...TRACKMASTER August 2006 FVX TMX Series Service Manual 13 19 FVX325 Series Final Assembly...
Page 169: ...TRACKMASTER 13 28 FVX TMX Series Service Manual August 2006 TMX Series w CE Option 317 01784...
Page 171: ...TRACKMASTER 13 30 FVX TMX Series Service Manual August 2006 TMX425 Series Frame Assembly...
Page 175: ...TRACKMASTER 13 34 FVX TMX Series Service Manual August 2006 TMX425 Series Final Assembly...
Page 197: ...TRACKMASTER 14 22 FVX TMX Series Service Manual August 2006...
Page 205: ...TRACKMASTER 15 8 FVX TMX Series Service Manual August 2006...