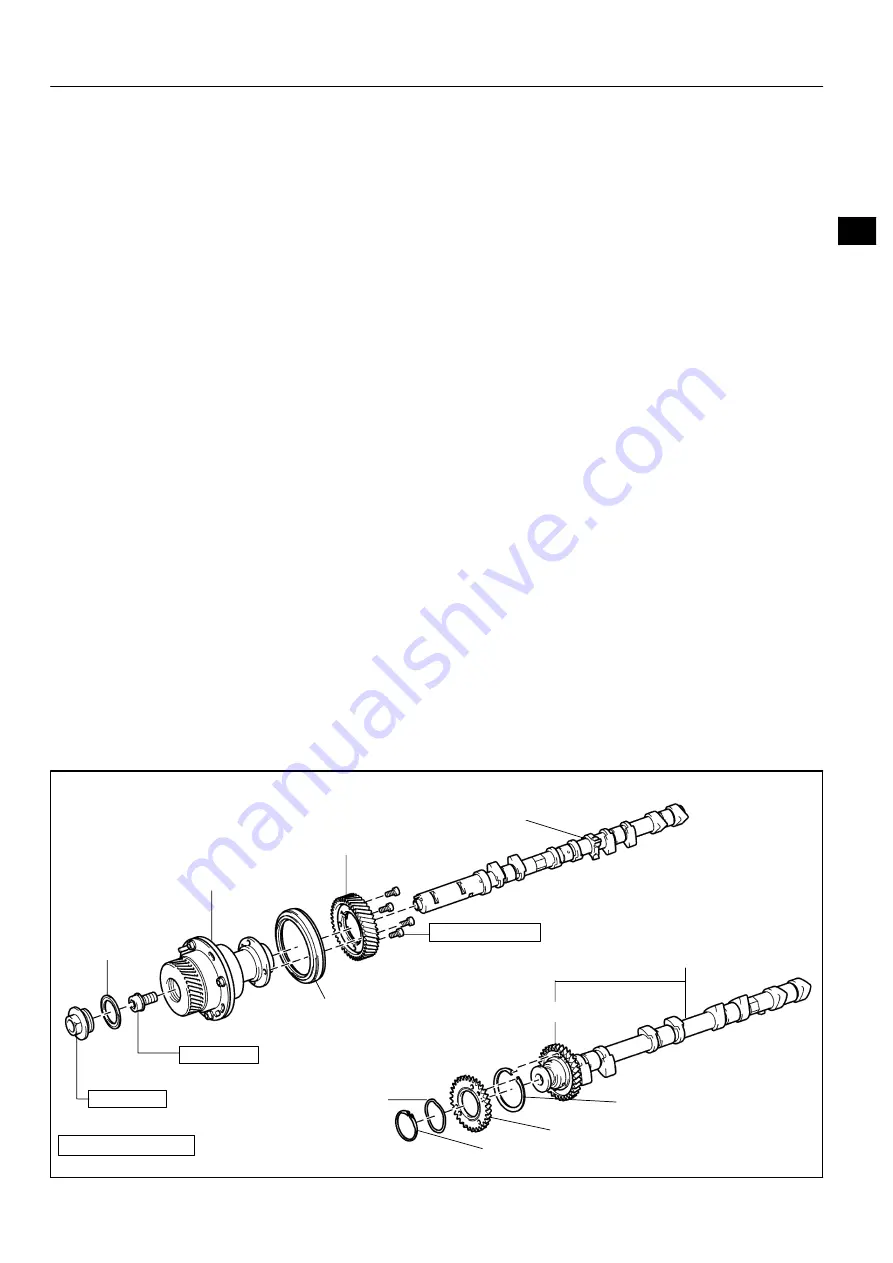
010B2
−
19
A54988
N·m (kgf·cm, ft·lbf) : Specified torque
z
Non
−
reusable part
Camshaft Timing Tube Assy
Camshaft Drive Gear
Seal Washer
z
Camshaft Setting Oil Seal
No. 2 Camshaft,
No. 4 Camshaft Sub
−
assy
Wave Washer
Camshaft Driven Main Gear
Snap Ring
Camshaft Timing Gear
Bolt Washer
Screw Plug
78 (790, 58)
15 (150, 11)
7.5 (80, 66 in.·lbf)
Camshaft Sub Gear
Camshaft,
No. 3 Camshaft Sub
−
assy
OVERHAUL
−
INTRODUCTION
HOW TO USE THIS MANUAL
01
−
1
1CD
−
FTV ENGINE REPAIR MANUAL (RM1046E)
HOW TO USE THIS MANUAL
GENERAL INFORMATION
1.
GENERAL DESCRIPTION
(a)
This manual is made in accordance with SAE J2008.
(b)
Generally, repair operations can be separated in the following 3 main processes:
1. Diagnosis
2. Removing and Installing, Replacing, Disassembling, Installing and Checking, Adjusting
3. Final Inspection
(c)
This manual explains the 1st process of ”Diagnosis” (placed in the ”Diagnostics” section), the 2nd pro-
cess of ”Removing and Installing, Replacing, Disassembling, Installing and Checking, Adjusting”, but
the 3rd process of ”Final Inspection” is omitted.
(d)
The following essential operations are not written in this manual. However, these operations must be
done in the practical situation.
(1)
Operation with a jack or lift
(2)
Cleaning of a removed part when necessary
(3)
Visual check
2.
INDEX
(a)
An alphabetical INDEX is provided as a section on the end of the book to guide you to the item to be
repaired.
3.
PREPARATION
(a)
Use of special service tools (SST) and special service materials (SSM) may be required, depending
on the repairing condition. Be sure to use SST and SSM when they are required and follow the working
procedure properly. A list of SST and SSM is in the Preparation section of this manual.
4.
REPAIR PROCEDURES
(a)
Component drawing is placed under the title when necessary.
(b)
Illustrations are placed as ”disassembled parts drawing” so that it enables you to understand the fitting
condition of the components.
(c)
Non
−
reusable parts, grease applied parts, precoated parts and tightening torque are specified in the
components drawing.
Example: