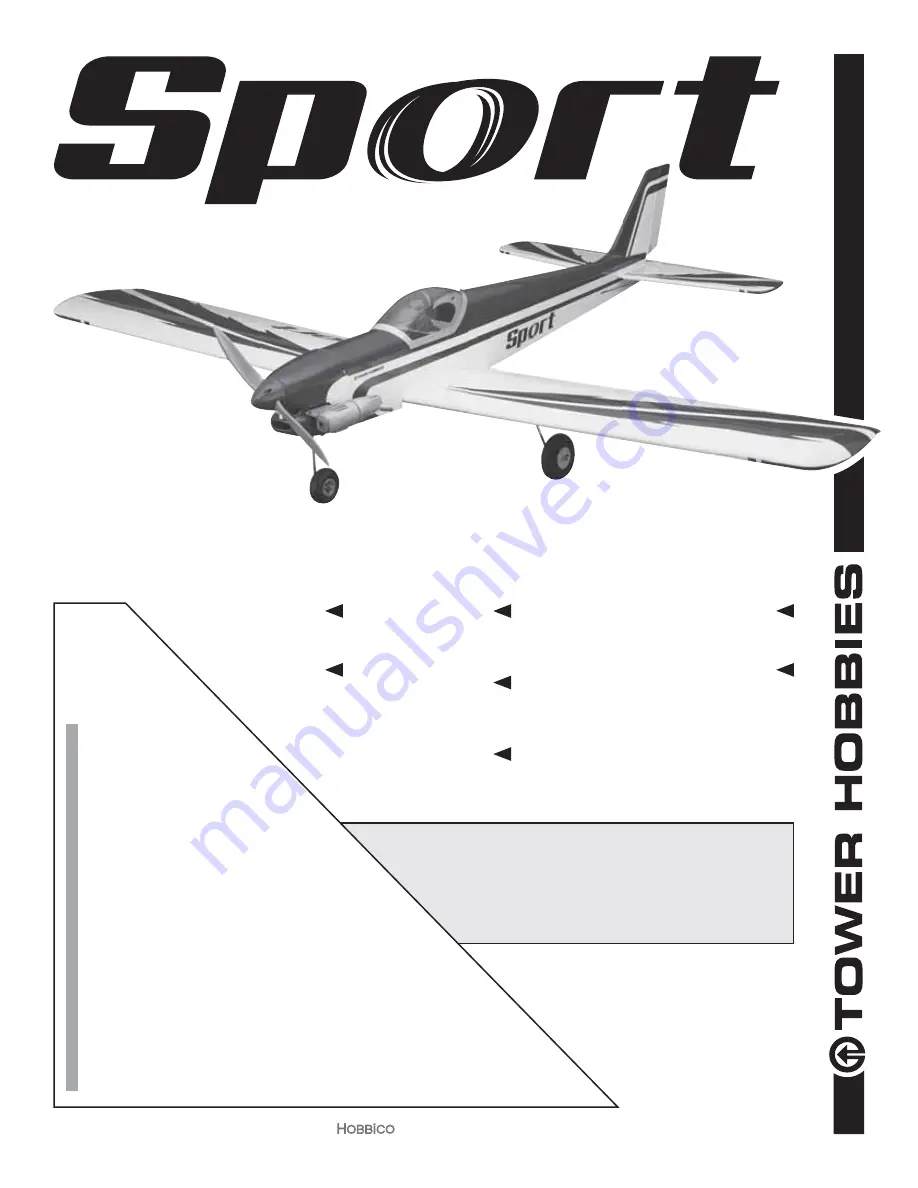
1
READ THROUGH THIS MANUAL
BEFORE STARTING CONSTRUCTION.
IT CONTAINS IMPORTANT INSTRUCTIONS
AND WARNINGS CONCERNING THE
ASSEMBLY AND USE OF THIS MODEL.
Tow e r
Hobbies
®
guarantees
this kit to be
free from defects
in both material and
workmanship at the
date of purchase. This
warranty does not cover any
component parts damaged by
use or modification. In no case shall
Tower Hobbies’ liability exceed the
original cost of the purchased kit. Further,
Tower Hobbies reserves the right to change
or modify this warranty without notice.
In that Tower Hobbies has no control over the final
assembly or material used for final assembly, no
liability shall be assumed nor accepted for any damage
or injury resulting from the use by the user of the final
user-assembled product. By the act of using the user-assembled
product, the user accepts all resulting liability.
If the buyer is not prepared to accept the liability associated with the
use of this product, the buyer is advised to return this kit immediately in
new and unused condition to the place of purchase.
To make a warranty claim send the defective part or item to Hobby Services at
the address below: (Visit hobbyservices.com for more information.)
Hobby Services • 3002 N. Apollo Dr. Suite 1 • Champaign IL 61822 • USA
Include a letter stating your name, return shipping address, as much contact information as
possible (daytime telephone number, fax number, e-mail address), a detailed description of
the problem and a photocopy of the purchase receipt. Upon receipt of the package the problem
will be evaluated as quickly as possible.
WA
R
R
A
N
TY
TOWA2030
©
2016 Tower Hobbies.
®
A subsidiary of Hobbico, Inc.
®
®
TOWER HOBBIES
Champaign, Illinois
(217) 398-8970 ext. 6
RADIO
4 – 5 channel
4 – 5 servos
WINGSPAN
60.2 in [1529mm]
WEIGHT
72 – 76 oz. [2041– 2155g]
WING AREA
592.8 sq in [38.24 dm
2
]
LENGTH
48.7 in [1237mm]
I N S T R U C T I O N M A N U A L
WING LOADING
17.49 – 18.46 oz/ft
2
[53 – 56 g/dm
2
]
POWER
.46 – .55 cu in [7.5 – 9.0cc] 2-stroke glow,
.70 cu in [11.5cc] 4-stroke glow,
Motor: 1.65" [42mm] 925W,
Castle Creations Edge Lite 75 ESC (not included)
ESC: 60A - 4S (not included)