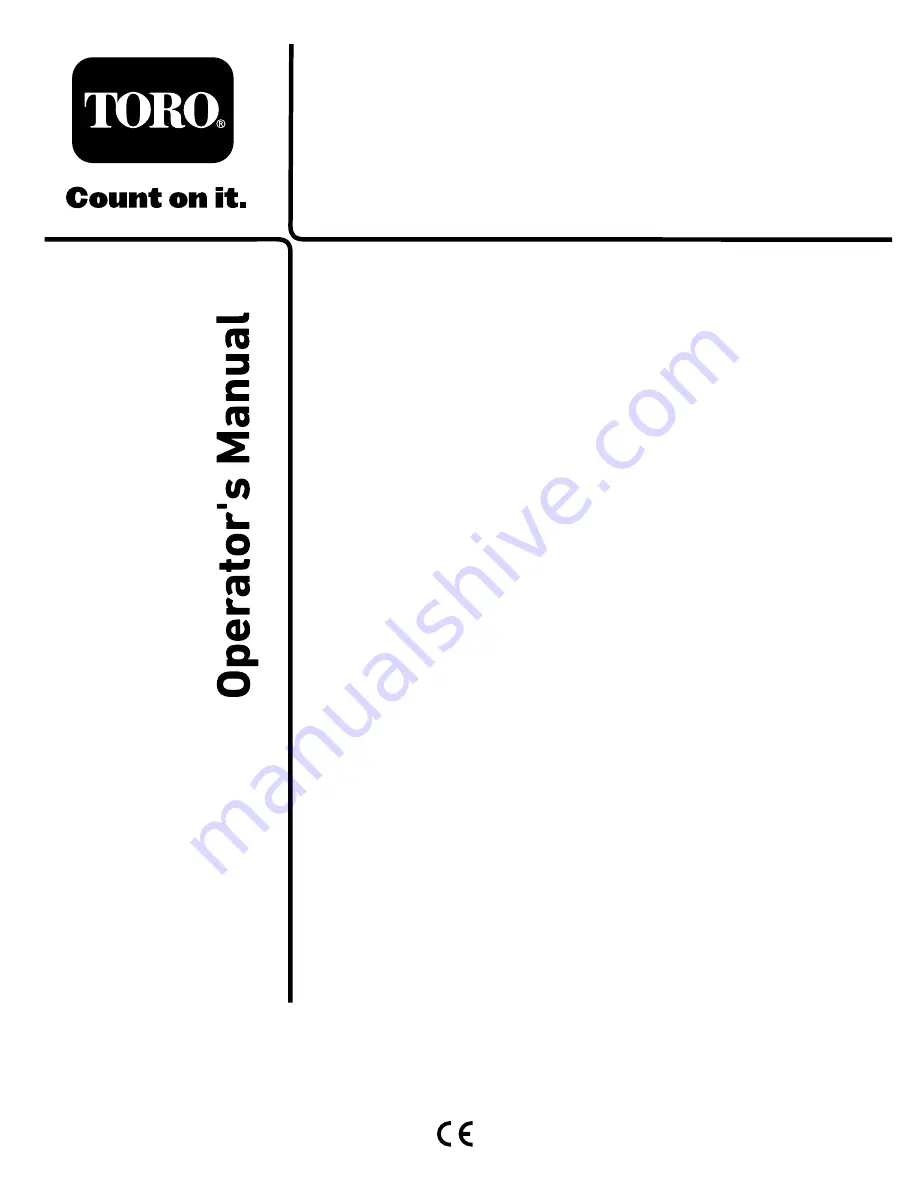
Form No. 3393-413 Rev B
MK3 200mm (8in) or 250mm
(10in) Cutting Unit
Model No. 02800—Serial No. 315000001 and Up
Model No. 02801—Serial No. 315000001 and Up
Model No. 02802—Serial No. 315000001 and Up
Model No. 02810—Serial No. 315000001 and Up
Model No. 02811—Serial No. 314000001 and Up
Model No. 02812—Serial No. 315000001 and Up
Register at www.Toro.com.
Original Instructions (EN)
*3393-413* B