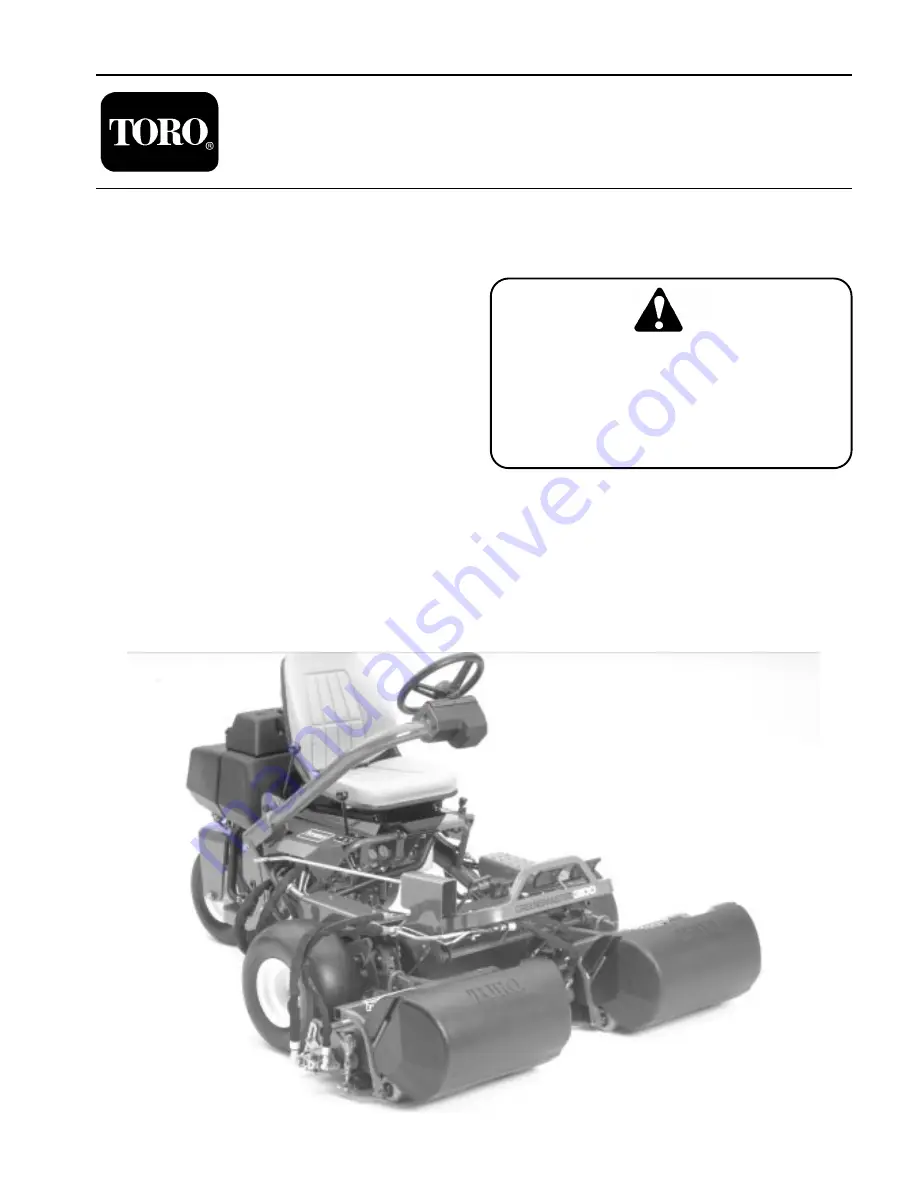
Service Manual
Greensmaster
®
3100/3050
Preface
This publication provides the service technician with
information for troubleshooting, testing, and repair of
m a j o r s y s t e m s a n d c o m p o n e n t s o n t h e
Greensmaster 3100 and 3050.
REFER TO THE TRACTION UNIT, CUTTING UNIT
AND ACCESSORY OPERATOR’S MANUALS FOR
OPERATING, MAINTENANCE AND ADJUSTMENT
INSTRUCTIONS. Space is provided at the end
of Chapter 2 in this publication to insert the Operator’s
Manuals and Parts Catalogs for your machine. Replace-
ment Operator’s Manuals are available by sending com-
plete Model and Serial Number of traction unit and
cutting unit to:
The Toro Company
8111 Lyndale Avenue South
Minneapolis, MN 55420
The Toro Company reserves the right to change product
specifications or this publication without notice.
This safety symbol means DANGER, WARN-
ING, or CAUTION, PERSONAL SAFETY IN-
STRUCTION. When you see this symbol,
carefully read the instructions that follow.
Failure to obey the instructions may result in
personal injury.
NOTE: A NOTE will give general information about the
correct operation, maintenance, service, testing or re-
pair of the machine.
IMPORTANT: The IMPORTANT notice will give im-
portant instructions which must be followed to pre-
vent damage to systems or components on the
machine.
©
The Toro Company - 1991, 1998
, 2002
, 200
4, 2005
Part No. 92784SL, Rev.
E
Summary of Contents for GREENSMASTER 3100
Page 2: ...This page is intentionally blank ...
Page 4: ...This page is intentionally blank ...
Page 8: ...Safety Instructions Page 1 4 Greensmaster 3100 ...
Page 12: ...This page is intentionally blank ...
Page 18: ...Engine Removal and Installation Page 3 6 Greensmaster 3100 ...
Page 34: ...Greensmaster 3100 Page 4 12 4 Hydraulic Schematics Rev E This page is blank ...
Page 69: ...This page is intentionally blank ...
Page 100: ...Repairs Page 4 72 Greensmaster 3100 ...
Page 110: ...This page is intentionally blank ...
Page 130: ...Greensmaster 3100 Page 6 6 Repairs Rev B ...
Page 132: ......
Page 133: ......
Page 134: ......
Page 135: ......
Page 136: ......
Page 137: ......
Page 138: ...Use Loctite 271 on spline nut Rev C ...
Page 139: ......
Page 140: ......
Page 141: ......
Page 142: ......
Page 143: ......
Page 144: ......
Page 145: ......
Page 146: ......
Page 147: ......
Page 148: ......
Page 149: ...Use Loctite 271 on spline nut Rev C ...
Page 150: ......
Page 152: ......
Page 153: ......
Page 154: ......
Page 155: ......
Page 156: ......
Page 157: ......
Page 158: ......
Page 159: ......
Page 160: ...Use Loctite 271 on spline nut threads Rev C ...
Page 161: ......
Page 162: ......
Page 163: ......
Page 164: ......
Page 165: ......
Page 166: ......
Page 167: ......
Page 168: ......
Page 169: ......
Page 170: ......
Page 171: ......
Page 172: ......
Page 173: ......
Page 174: ...Use Loctite 271 on spline nut threads Rev C ...
Page 175: ......
Page 176: ......
Page 178: ......
Page 179: ......
Page 180: ......
Page 181: ......
Page 182: ......
Page 183: ......
Page 184: ......
Page 185: ......
Page 186: ......
Page 187: ......
Page 188: ...Use Loctite 271 on spline nut threads Rev C ...
Page 189: ......
Page 190: ......
Page 191: ......
Page 192: ......
Page 193: ......
Page 194: ......
Page 195: ......
Page 196: ......
Page 197: ......
Page 198: ......
Page 199: ......
Page 200: ......
Page 201: ......
Page 202: ......
Page 203: ...Use Loctite 271 on spline nut threads Rev C ...
Page 204: ......
Page 205: ......
Page 206: ......
Page 207: ......
Page 208: ......
Page 209: ......
Page 210: ...This page is intentionally blank ...
Page 233: ...This page is intentionally blank ...