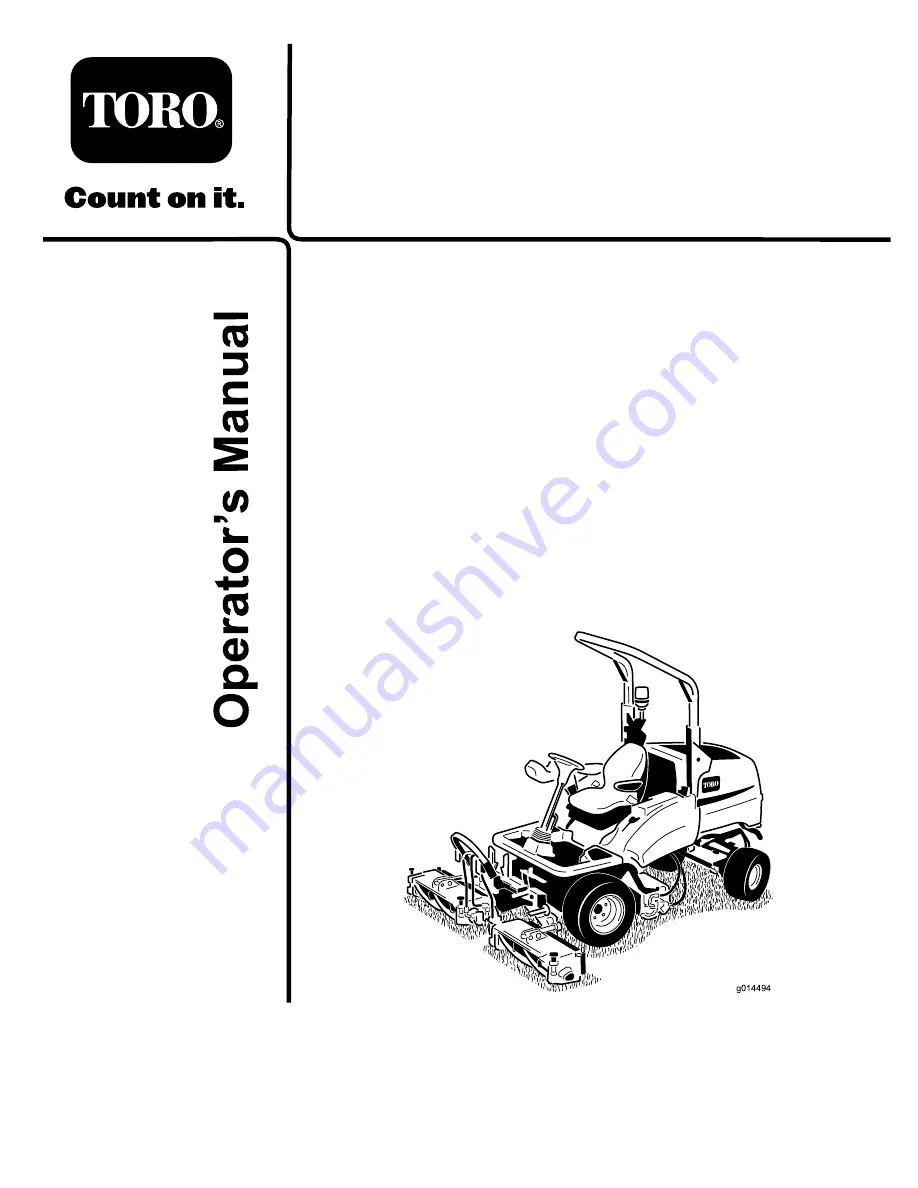
Form No. 3365-917 Rev B
CT2120 Compact Triple
2-Wheel Drive Turf Mower
CT2140 Compact Triple 4-Wheel
Drive Turf Mower
Model No. 30655—Serial No. 310000001 and Up
Model No. 30656—Serial No. 310000001 and Up
g014494
To register your product or download an
Operator's Manual
or
Parts Catalog
at no charge, go to www.Toro.com.
Original Instructions (EN)
Summary of Contents for CT2120 30655
Page 55: ...Schematics Showing Beacon Lights Aux Power Connector g014756 55 ...
Page 61: ...Notes 61 ...
Page 62: ...Notes 62 ...