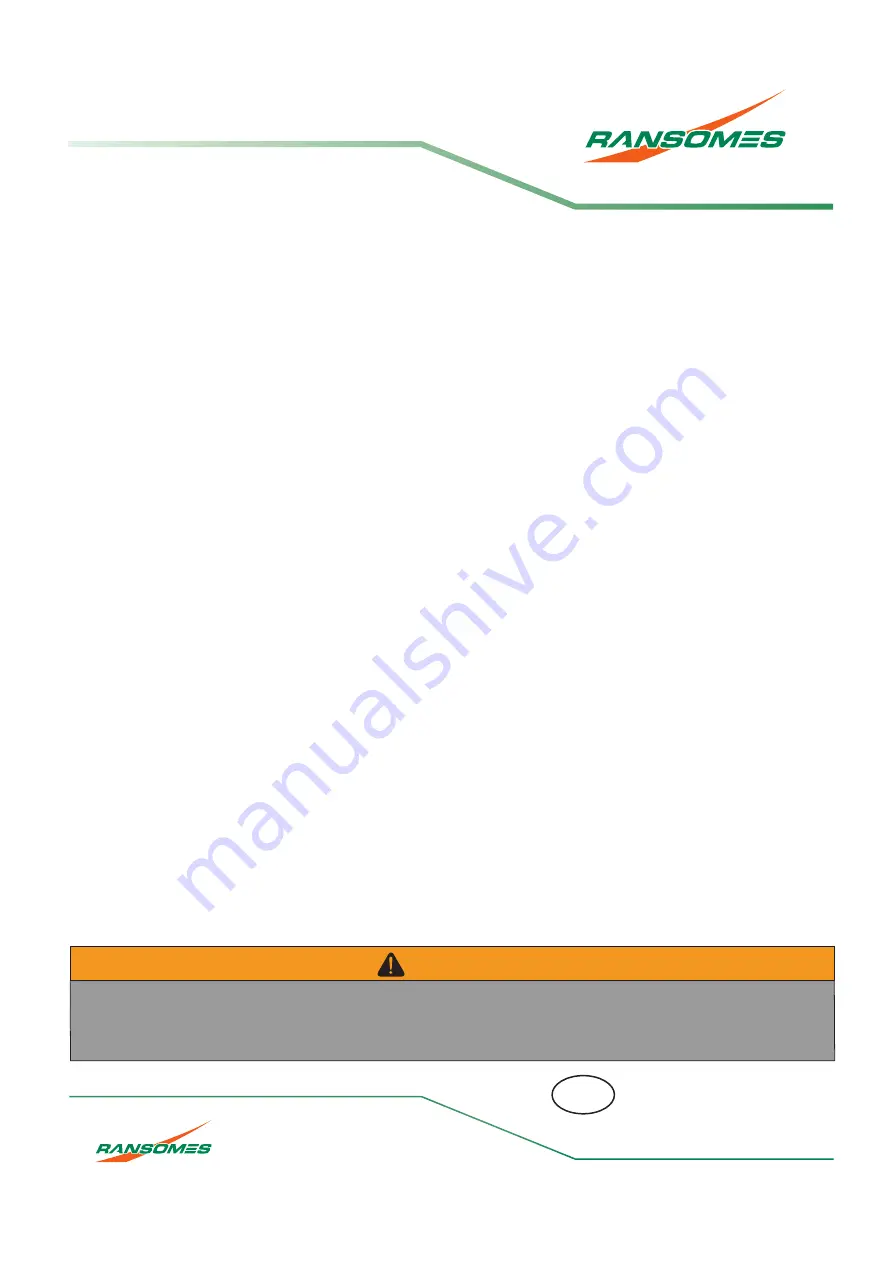
®
®
RJL 100 January 2021
Safety, Operation & Maintenance Manual
Ransomes HR380 Ride on Rotary & Flail Mower
Kubota D1803 - CR - E5
With ROPS Series: MV
Product code: 10007167
10023750-GB (Rev.A)
WARNING
WARNING: If incorrectly used this machine can cause severe injury. Those who use and maintain this
machine must be trained in its proper use, warned of its dangers and must read the entire manual
before attempting to set up, operate, adjust or service the machine.
GB
United
Kingdom