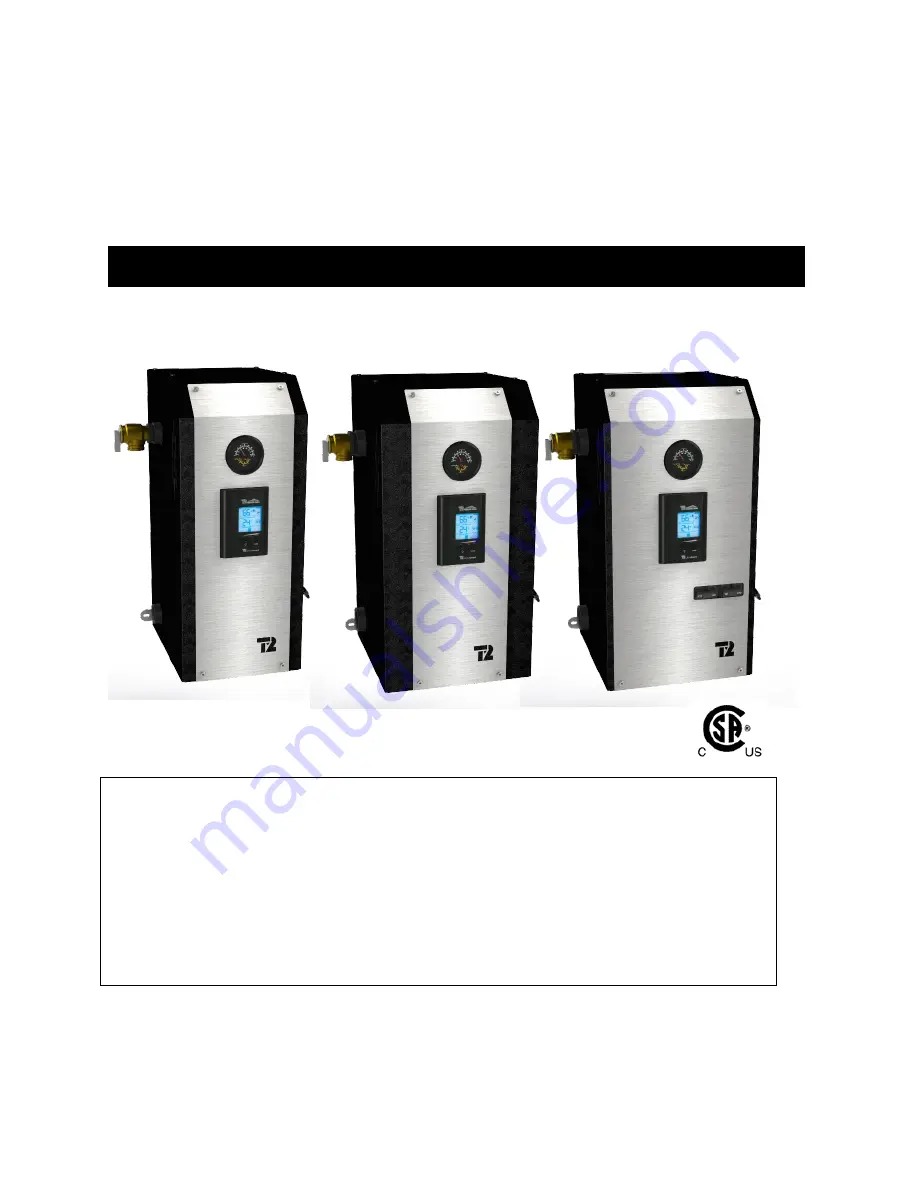
Electric Boilers
BTH ULTRA
Models ranging from 12 kW to 36 kW 208/240 Volts (1 phase)
INSTALLATION & OPERATION MANUAL
THERMO 2000 INC.
Revision : June 2015
Printed In Canada
Your
BTH ULTRA Electric Boiler
has been carefully assembled and factory tested to provide
years of trouble-free service. The following information and safety measures are provided to
enable proper installation, operation, and maintenance of this product.
It is imperative that all persons who are expected to install, operate or adjust this boiler should
read these instructions carefully.
Any questions regarding the operation, maintenance, service or warranty of this electric boiler
should be directed to the supplier.
When all installation steps have been completed, keep this installation manual in a safe place
(close to the boiler) for future reference.