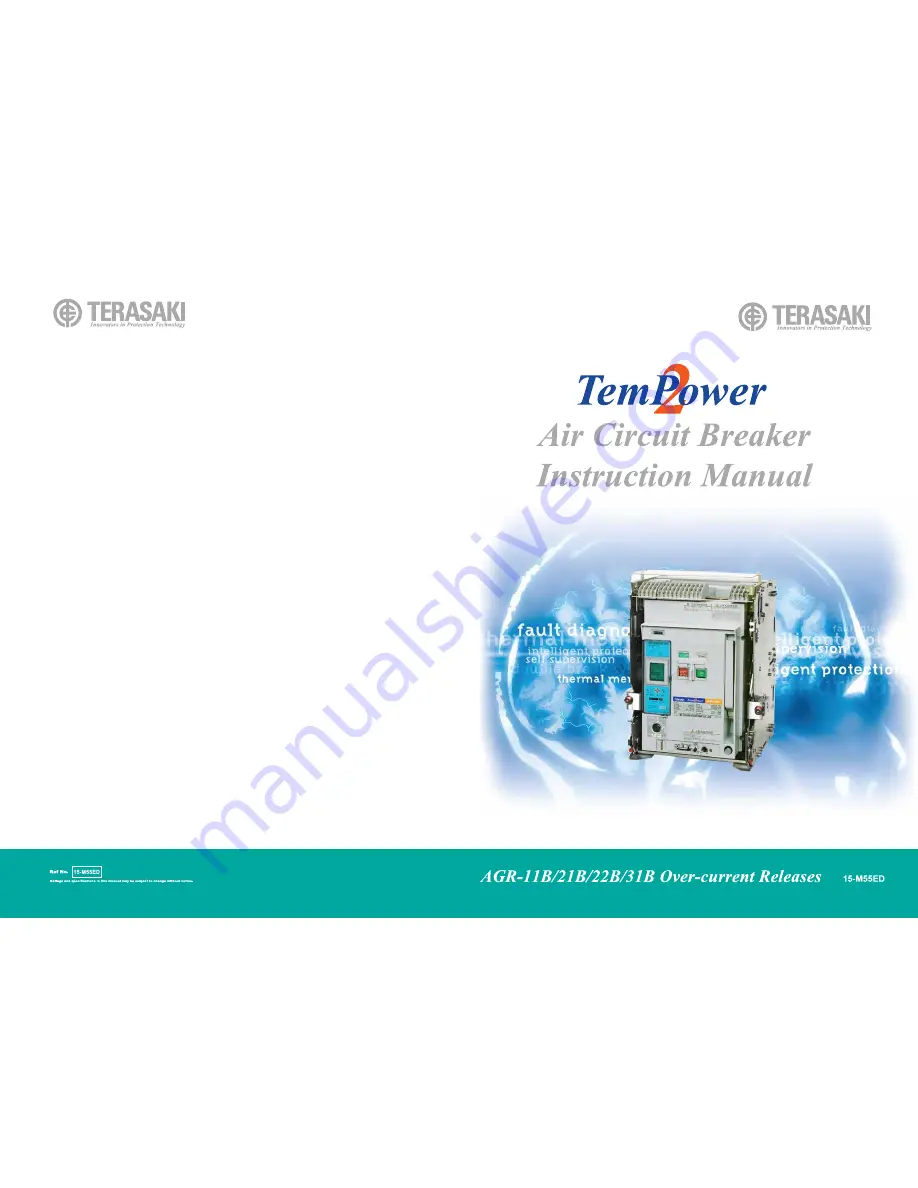
TERASAKI ELECTRIC (EUROPE) LTD.
80 Beardmore Way, Clydebank Industrial Estate,
Clydebank, Glasgow, G81 4HT, Scotland (UK)
Telephone: 44-141-941-1940
Fax:
44-141-952-9246
Email:
[email protected]
http://www.terasaki.com
TERASAKI MIDDLE EAST
Saif Zone Q3-168, PO Box 120860
Sharjah, UAE
Telephone: 971-56-676-4825
Fax:
976-655-78141
Email:
[email protected]
http://www.terasaki.com
TERASAKI ELECTRIC (EUROPE) LTD.
(FILIALE ITALIA)
Via Ambrosoli, 4A-20090, Rodano, Milano, Italy
Telephone: 39-02-92278300
Fax:
39-02-92278320
Email:
[email protected]
http://www.terasaki.it
TERASAKI ELECTRIC (EUROPE) LTD.
(SUCURSAL EN ESPAÑA)
Pol. Ind. Coll de la Manya, C/Cal Ros dels Ocells 5
08403 Granollers , (Barcelona) España
Telephone: 34-93-879-60-50
Fax:
34-93-870-39-05
Email:
[email protected]
http://www.terasaki.es
TERASAKI ELECTRIC (EUROPE) LTD.
(FILIAL SVERIGE)
Snickarvägen 2, SE-132 38 SALTSJÖ-BOO, Sweden
Telephone: 46-8-556-282-30
Fax:
46-8-556-282-39
Email:
[email protected]
http://www.terasaki.se
TERASAKI CIRCUIT BREAKERS (S) PTD. LTD.
17 Tuas Street, Singapore, 638454
Telephone: 65-6744-9752
Fax:
65-6748-7592
Email:
tecs@paci
fi
c.net.sg
TERASAKI ELECTRIC CO., LTD.
Head Office & Circuit Breaker Division
6-13-47 Kamihigashi, Hirano-ku,
Osaka 547-0002, Japan
Telephone: 81-6-6791-2763
Fax:
81-6-6791-2732
Email:
[email protected]
http://www.terasaki.co.jp
TERASAKI ELECTRIC (M) SDN, BHD.
Lot 3, Jalan 16/13D, 40000 Shah Alam,
Selangor Darul Ehsan, Malaysia
Telephone: 60-3-5549-3820
Fax:
60-3-5549-3960
Email:
TERASAKI DO BRASIL LTDA.
Rua Cordovil, 259-Parada De Lucas,
21250-450, Rio De Janeiro-R.J., Brazil
Telephone: 55-21-3301-9898
Fax:
55-21-3301-9861
Email:
[email protected]
http://www.terasaki.com.br
TERASAKI ELECTRIC (CHINA) LTD.
72 Paci
fi
c Industrial Park, Xin Tang Zengcheng,
Guangzhou 511340, China
Telephone: 86-20-8270-8556
Fax:
86-20-8270-8586
Email:
TERASAKI ELECTRIC GROUP SHANGHAI
REPRESENTATIVE OFFICE
Room No. 1405-6, Tomson Commercial Building,
710 Dong Fang Road, Pudong, Shanghai,
200122, China
Telephone: 86-21-58201611
Fax:
86-21-58201621
Email: