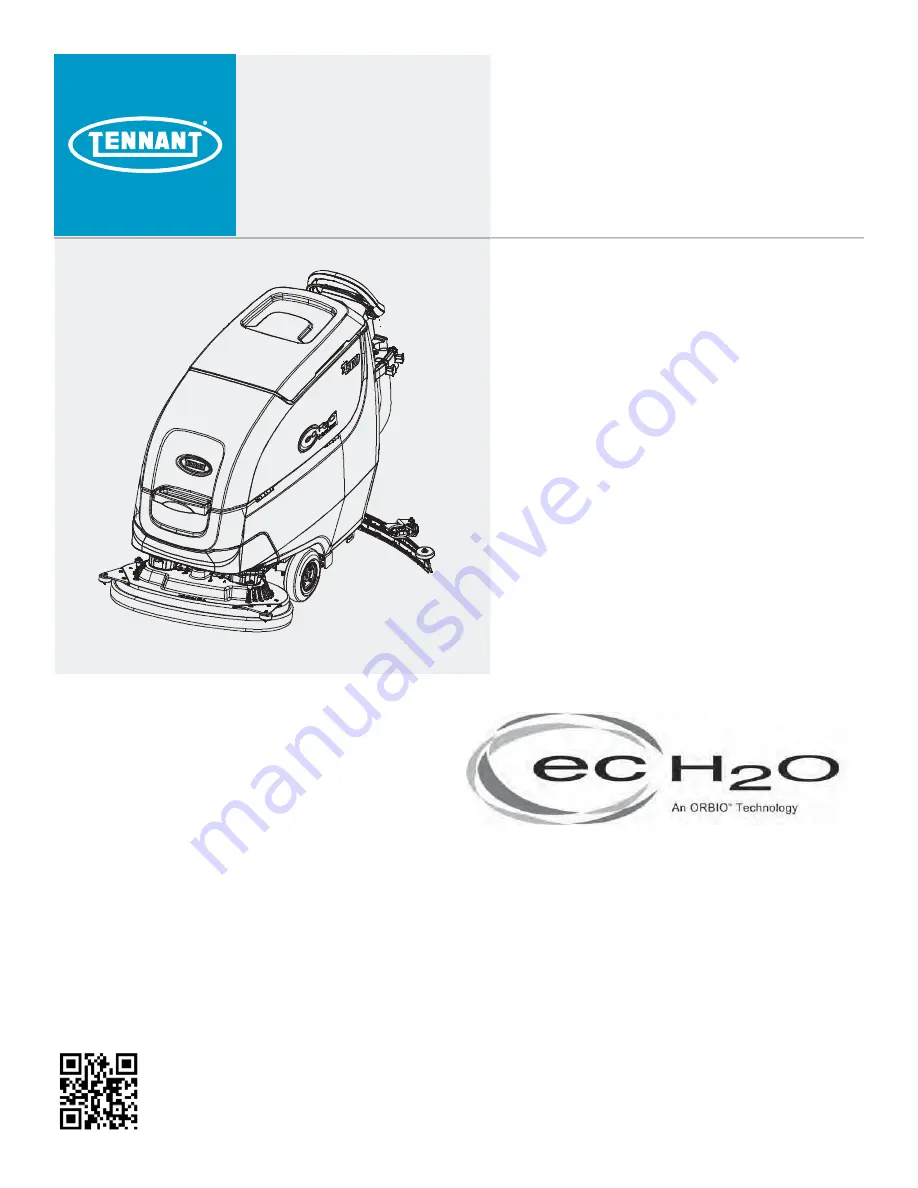
T500
(Battery)
Automatic Floor Scrubber
Service Information Manual
9015504
Rev. 01 (1-2018)
*9015504*
North America / International
For the latest Parts Manuals and other
language Operator Manuals, visit:
www.tennantco.com/manuals
Hygenic
®
Fully Cleanable Recovery Tank
Tennant True
®
Parts
IRIS
®
a Tennant Technology
Pro-Panel™ Controls
Insta-Fit™ Adapter
Smart-Fill™Automatic Battery Watering
Summary of Contents for t500
Page 5: ...5 T500 9015504 01 2018 CONTENTS ...
Page 55: ...55 T500 9015504 01 2018 TROUBLESHOOTING ...
Page 89: ...89 T500 9015504 01 2018 SERVICE 9 Cycle the key switch to save selections ...
Page 111: ...111 T500 9015504 01 2018 SERVICE ...
Page 117: ...117 T500 9015504 01 2018 SERVICE ...
Page 146: ...146 T500 9015504 01 2018 SERVICE ...