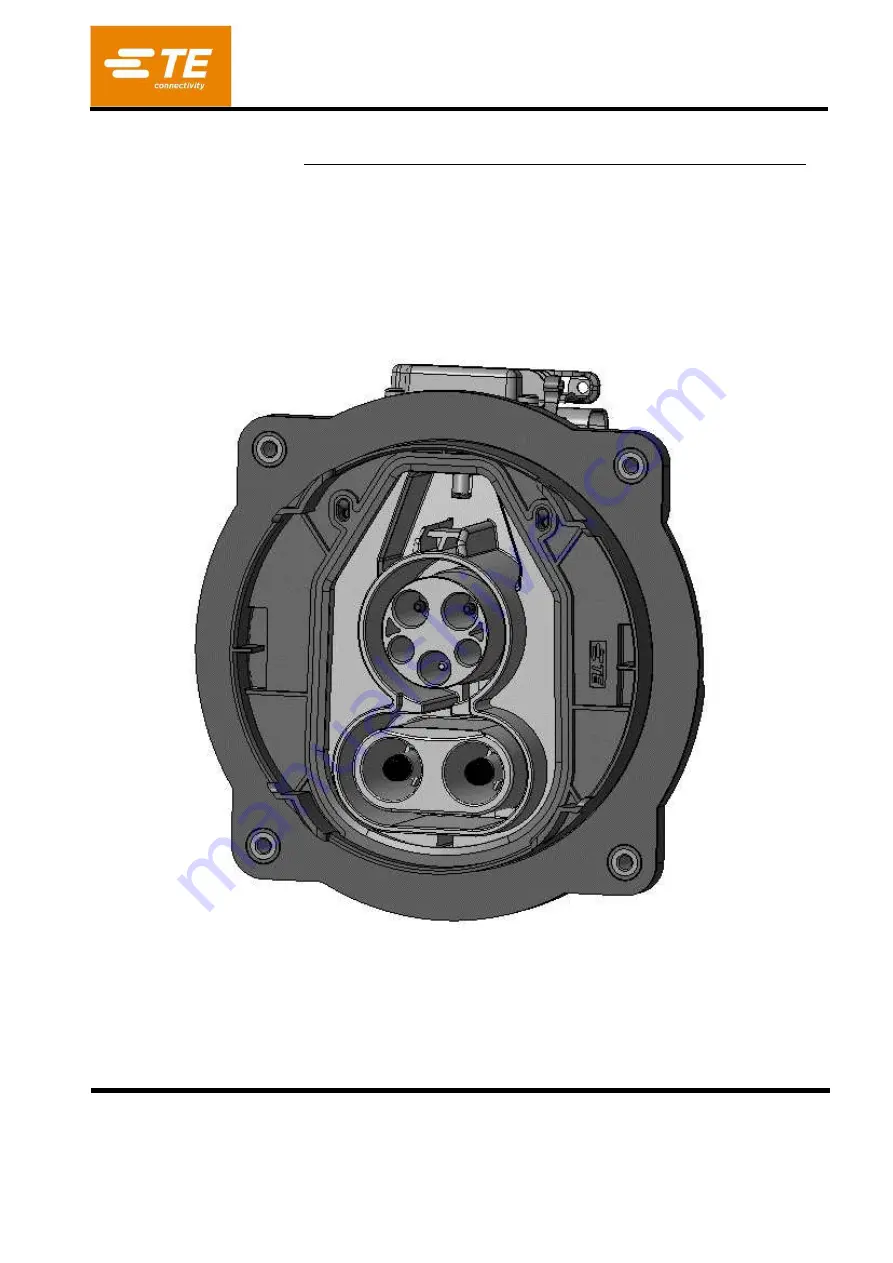
1
of 36
© 2020 TE Connectivity family of companies
All Rights Reserved
| Indicates Change
*Trademark. TE Connectivity, TE connectivity (logo), and TE (logo) are trademarks. Other logos, product, and/or company names may be trademarks of their respective owners.
Application
Specification
114-94438 REV C1
18JUN2020
Class 1
VEHICLE CHARGE INLET CCS1
acc. IEC62196-3 / SAE J1772
Summary of Contents for CCS1
Page 26: ...114 94438 REV C1 26 of 36...