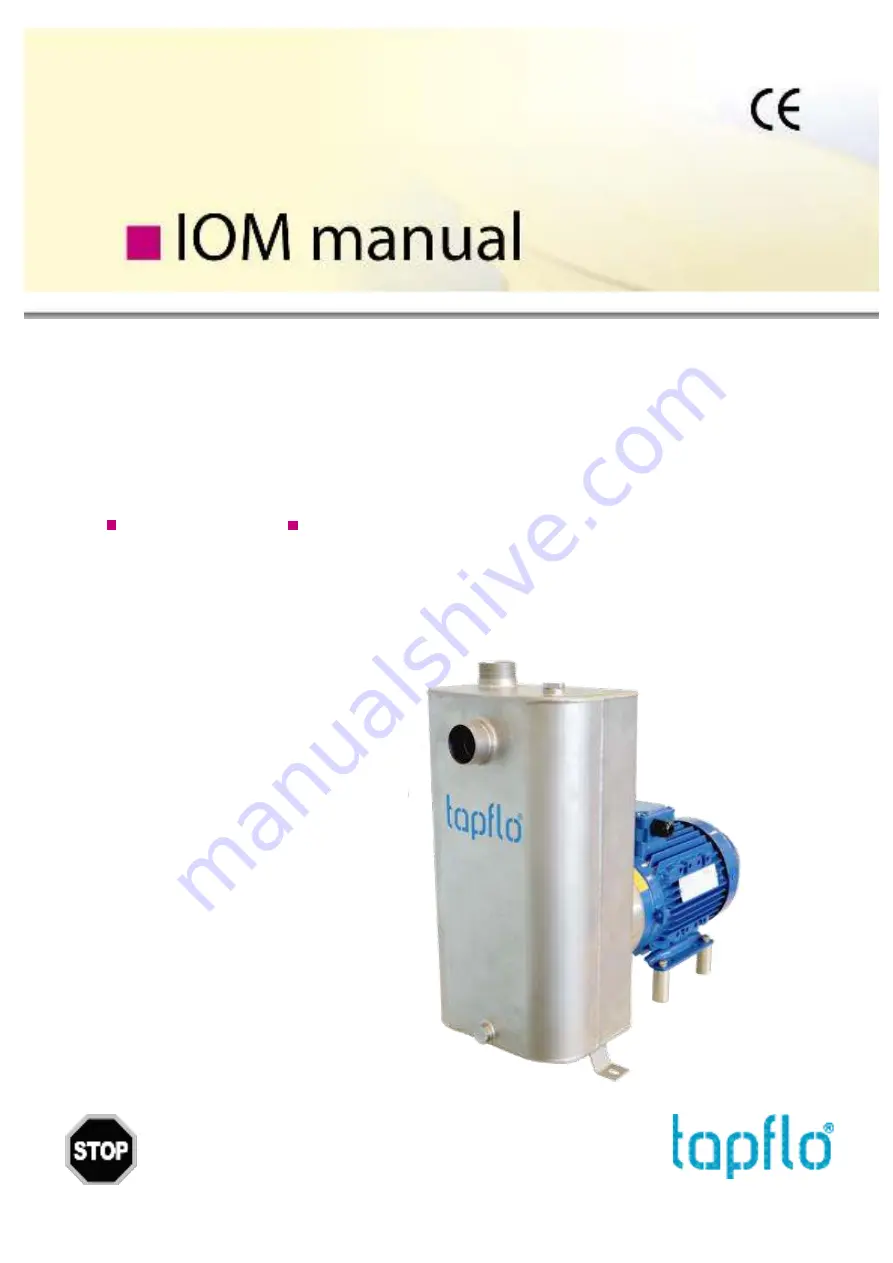
Read this instruction manual carefully,
before you install and operate the pump.
2014 rev. 1
Instructions for installation, start up, operation and maintenance.
Self-priming CTS H pumps in electro polished AISI 316L stainless steel.
Self-priming CTS I pumps in glass blasted AISI 316L stainless steel.
Pump models:
CTS I
CTS H
With 2900 rpm motor:
With 2900 rpm motor:
CTS I CC-22
CTS H CC-22
CTS I CE-22
CTS H CE-22
CTS I DD-40
CTS H DD-40
CTS I DF-40
CTS H DF-40
CTS I EF-55
CTS H EF-55
CTS I EG-55
CTS H EG-55
CTS I EF-75
CTS H EF-75
CTS I EG-75
CTS H EG-75