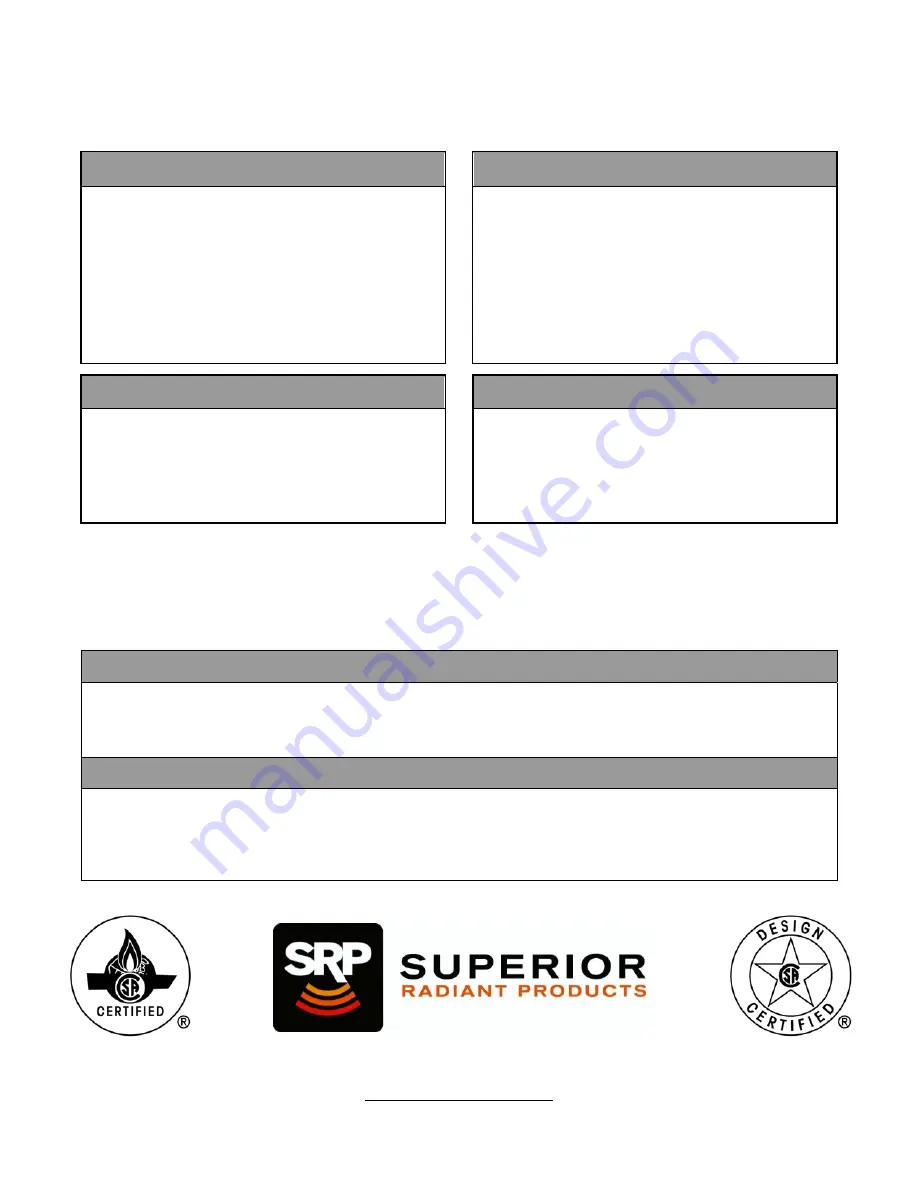
06/14 LT013
Premier VS Infrared Heating System
Installation, Operation and Maintenance Instructions
FOR YOUR SAFETY
CONSIGNES DE SEURITE
If you smell gas:
1. Open windows
2. Don’t touch electrical switches
3. Extinguish any open flame
4. Immediately call your gas supplier
Si vous sentez une odeur de gaz:
1. Ouvrez les fenêtres
2. Ne touchez pas aux interrupteurs
électriques
3. Éteignez toute flamme nue
4. Contactez immédiatement votre
fournisseur de gaz
Installer
Read and thoroughly understand these instructions before attempting any installation.
Owner
Retain this manual for reference.
WARNING
Improper installation, adjustment, alteration, service or maintenance can cause injury, death or
property damage. Read the installation, operating and maintenance instructions thoroughly before
installing or servicing this equipment.
AVERTISSEMENT
Une installation, un réglage, une modification, une réparation ou un entretien incorrect peut entraîner
des dommages matériels, des blessures ou la mort. Lisez attentivement les instructions d’installation,
de fonctionnement et d’entretien avant de procéder à l’installation ou à l’entretien de cet équipement.
563 Barton Street, Stoney Creek, Ontario L8E 5S1
www.superiorradiant.com
FOR YOUR SAFETY
CONSIGNES DE SEURITE
Do not store or use gasoline or other
flammable vapors and liquids in the
vicinity of this or any other appliance.
Il est interdit d’utiliser des liquides
inflammables ou dégageant des vapeurs
inflammables, a proximités de tout
appareil fonctionnent au gaz.
!
!
!
!
!
!