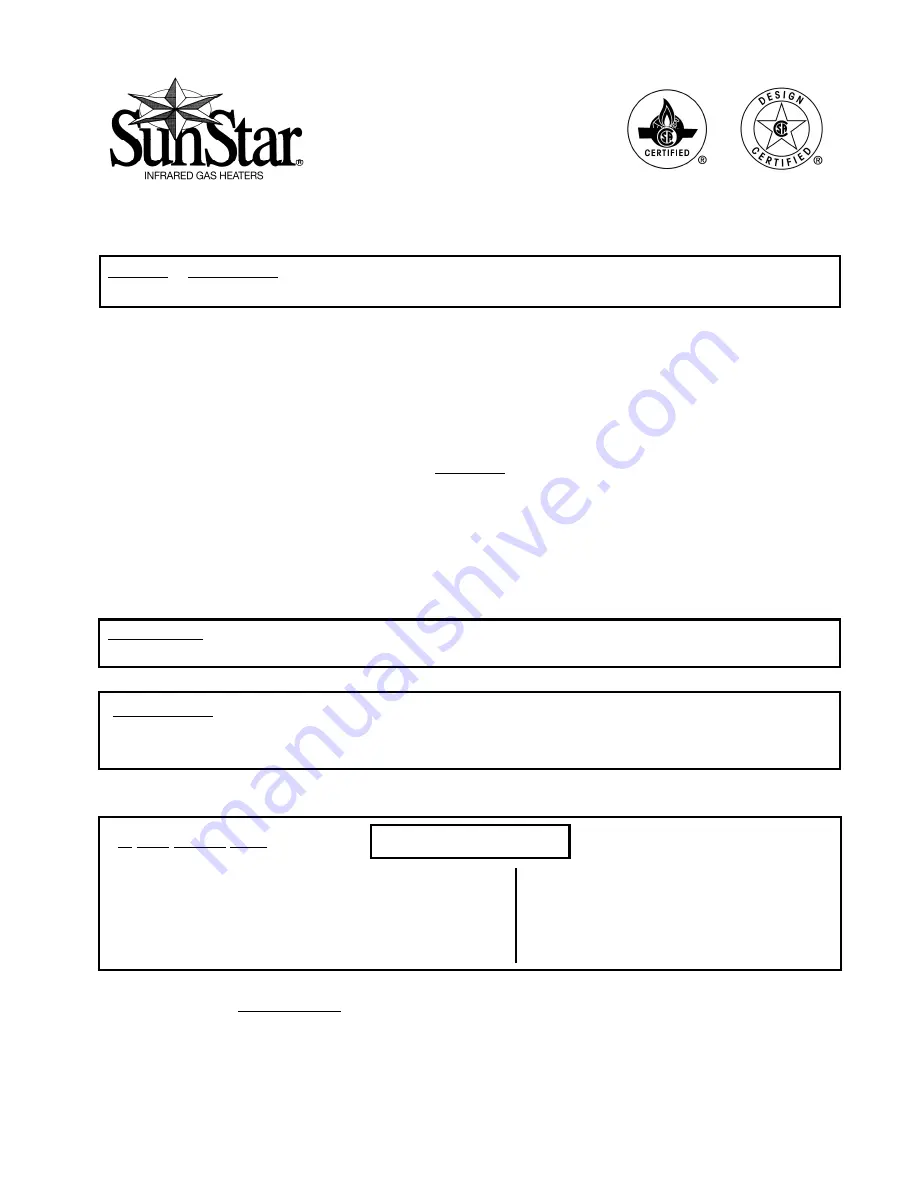
Form 43343320
Aug 2012
INSTALLATION AND OPERATION INSTRUCTIONS
OWNER / INSTALLER: For your safety this manual must be carefully and thoroughly read and
understood before installing, operating or servicing this heater.
INFRARED RADIANT TUBE HEATER
Single Stage Push Through System (Positive Pressure)
Models:
SPS SERIES:
(40, 50, 75, 100, 125, 150, 175, 200) – N5/L5
SPU SERIES:
(40, 50, 75, 100, 125, 150, 175, 200) – N5/L5
!INSTALLER:
This manual is the property of the owner. Please present this manual to the
owner when you leave the job site.
▲WARNING:
Improper installation, adjustment, alteration, service, or maintenance can
cause property damage, injury or death. Read the installation, operation and maintenance
instructions thoroughly before installing or servicing this equipment.
IF YOU SMELL GAS:
FOR YOUR SAFETY
FOR YOUR SAFETY
FOR YOUR SAFETY
FOR YOUR SAFETY
!
!
!
!
DO NOT
DO NOT
DO NOT
DO NOT try to light any appliance.
!
!
!
!
DO NOT
DO NOT
DO NOT
DO NOT touch any electrical switch; DO NOT
DO NOT
DO NOT
DO NOT use any
telephone in your building.
!
!
!
!
IMMEDIATELY
IMMEDIATELY
IMMEDIATELY
IMMEDIATELY call your gas supplier from a neighbor's
telephone. Follow the gas supplier's instructions. If you
cannot reach your gas supplier, call the fire department.
DO NOT
DO NOT
DO NOT
DO NOT store or use gasoline or other
store or use gasoline or other
store or use gasoline or other
store or use gasoline or other
flammable vapors and liquids in the vicinity of
flammable vapors and liquids in the vicinity of
flammable vapors and liquids in the vicinity of
flammable vapors and liquids in the vicinity of
this or any other appliance.
this or any other appliance.
this or any other appliance.
this or any other appliance.
!IMPORTANT:
!IMPORTANT:
!IMPORTANT:
!IMPORTANT: SAVE THIS MANUAL FO
SAVE THIS MANUAL FO
SAVE THIS MANUAL FO
SAVE THIS MANUAL FOR FUTURE REFERENCE.
R FUTURE REFERENCE.
R FUTURE REFERENCE.
R FUTURE REFERENCE.
Manufactured for:
SUNSTAR HEATING PRODUCTS, INC.
SUNSTAR HEATING PRODUCTS, INC.
SUNSTAR HEATING PRODUCTS, INC.
SUNSTAR HEATING PRODUCTS, INC.
Post Office Box 36271 (28236) • 306 West Tremont Avenue (28203) • Charlotte, North Carolina
Phone (704) 372-3486 • Fax (704) 332-5843 • www.sunstarheaters.com • email: [email protected]