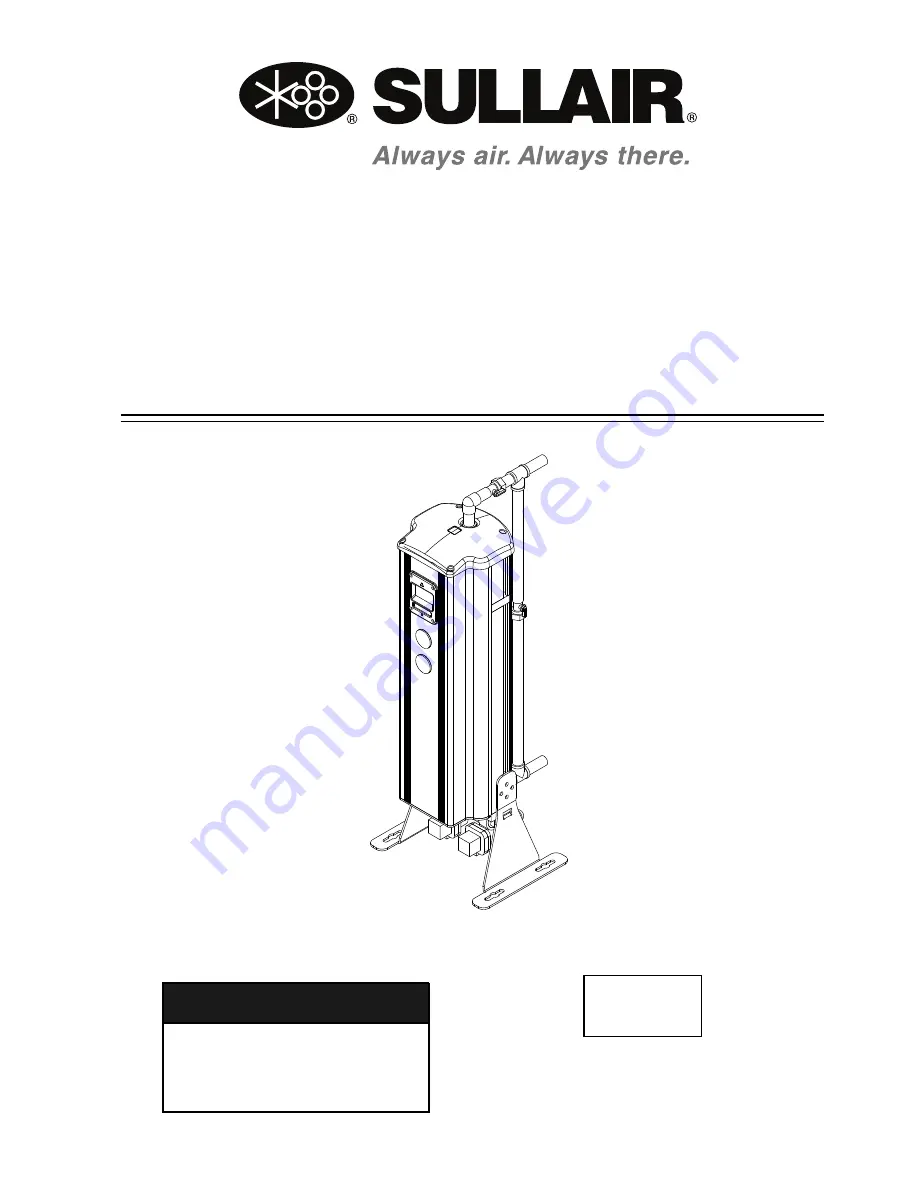
Failure to follow the instructions
and procedures in this manual or,
misuse of this equipment will
VOID its warranty!
WARRANTY NOTICE
PART NUMBER:
KEEP FOR
FUTURE
REFERENCE
USER/SERVICE MANUAL
©
SULLAIR CORPORATION
The information in this manual is current
as of its publication date, and applies to
compressor
serial number
:
and all subsequent serial numbers.
02250194-767 R00
M
ODULAR
R
EGENERATIVE
D
RYERS
DMD S
ERIES
(DMD-3
TO
DMD-240)
0611MD0001
Summary of Contents for DMD Series
Page 10: ...10 NOTES ...
Page 12: ...12 NOTES ...
Page 16: ...16 NOTES ...
Page 19: ...SECTION 4 DMD MODULAR REGENERATIVE DRYER 19 4 1 P I DMD 3 60 02250195 322 ...
Page 20: ...DMD MODULAR REGENERATIVE DRYER SECTION 4 20 4 2 P I DMD 75 120 02250196 454 ...
Page 21: ...SECTION 4 DMD MODULAR REGENERATIVE DRYER 21 4 3 P I DMD 180 02250196 455 ...
Page 22: ...DMD MODULAR REGENERATIVE DRYER SECTION 4 22 4 4 P I DMD 240 02250196 456 ...
Page 30: ...30 NOTES ...
Page 34: ...34 NOTES ...
Page 37: ...DMD MODULAR REGENERATIVE DRYER SECTION 7 37 7 1 DMD3 DMD5 DMD10 ...
Page 38: ...SECTION 7 DMD MODULAR REGENERATIVE DRYER 38 7 2 DMD15 DMD20 DMD25 DMD30 ...
Page 39: ...DMD MODULAR REGENERATIVE DRYER SECTION 7 39 7 3 DMD40 DMD50 DMD60 ...
Page 40: ...DMD MODULAR REGENERATIVE DRYER SECTION 7 40 7 4 DMD75 DMD100 DMD120 ...
Page 41: ...SECTION 7 DMD MODULAR REGENERATIVE DRYER 41 7 5 DMD180 ...
Page 42: ...DMD MODULAR REGENERATIVE DRYER SECTION 7 42 7 6 DMD240 ...
Page 44: ...44 NOTES ...
Page 45: ...NOTES 45 ...