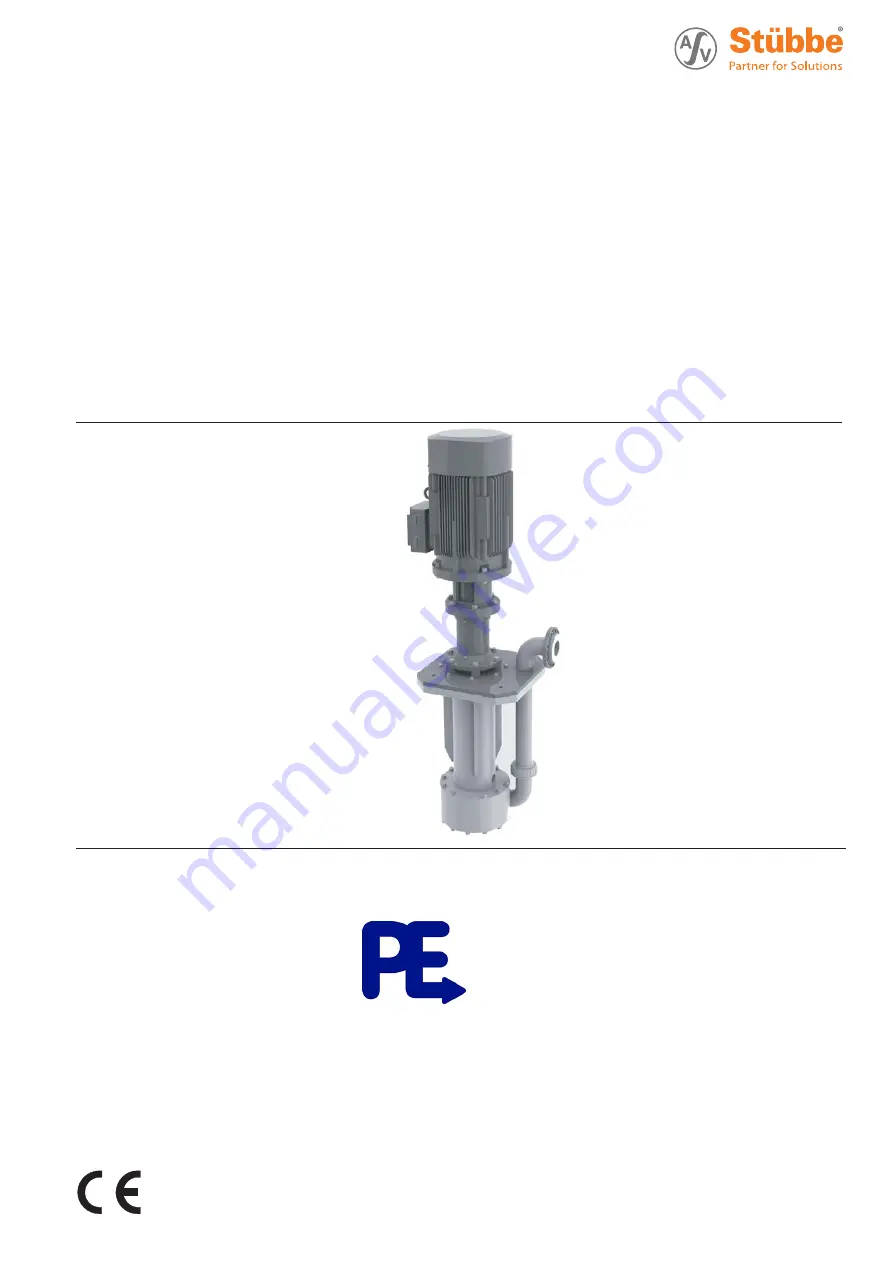
Plastic
Sump Pump
Original Operating Manual
Series ETL
Version
BA-2015.09.17
Print-No.
300 106
TR MA DE Rev002
We reserve the right to make technical changes.
Read carefully before use.
Save for future use.
Distributed in the UK by.....
Pump Engineering Limited.
Unit B1, Riverside Industrial Estate,
Littlehampton, West Sussex, BN17 5DF, United Kingdom
Tel: 01903 730900 Fax: 01903 730234
email: [email protected] Web: www.pumpeng.co.uk