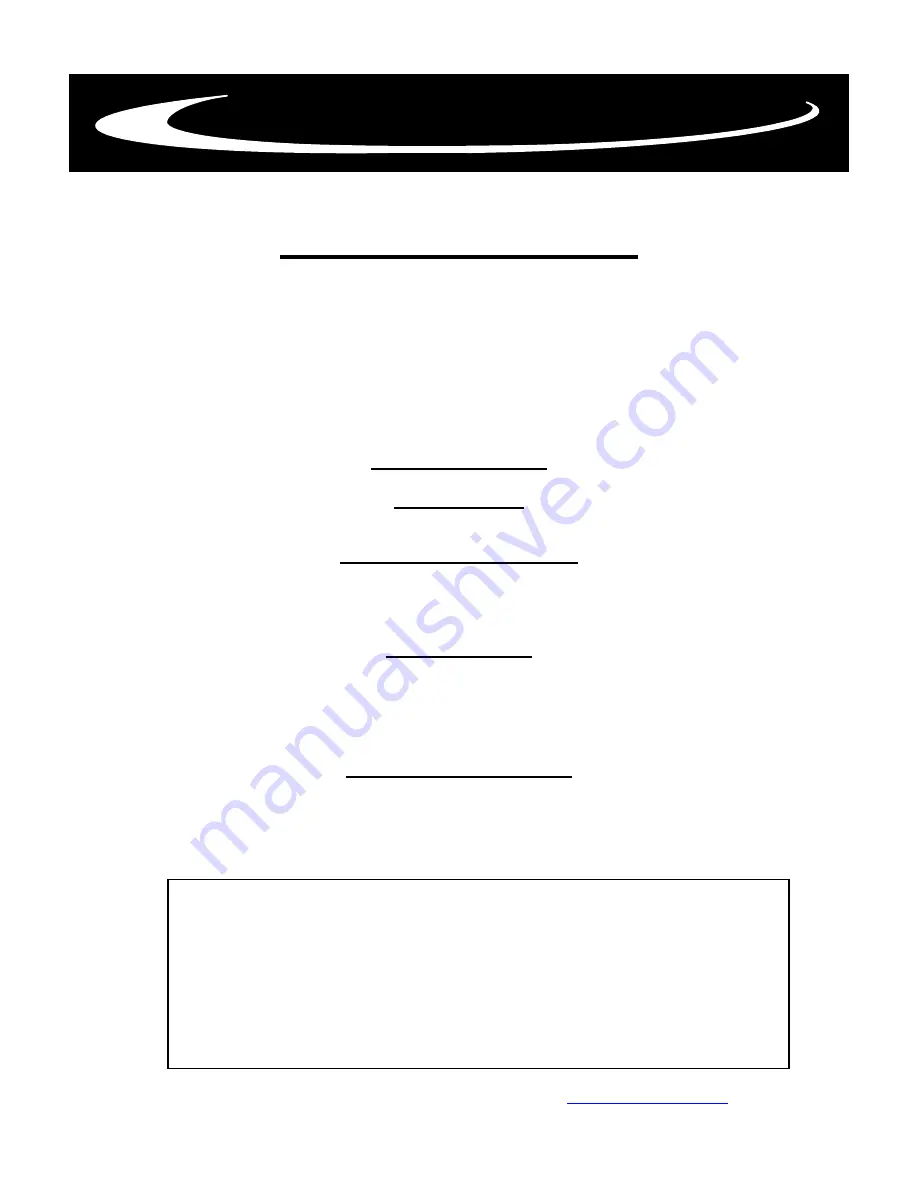
Surface to Surface Inc.
®
Operators Manual
** M2-H **
USE IN CONJUNCTION WITH OEM MANUALS (ENCLOSED)
Unit Serial No. _______________
Hydraulic Motor
SNM2/11C106
Gorman-Rupp® Pump
STS-GR82E2 – Serial No. ________________
Control Valve
Serial No.__________________
Links relating to this Manual
www.stsmixers.com
www.grpumps.com
STS-102 Rev. 08/24/18
www.stsmixers.com
Dealer
Summary of Contents for M2-H
Page 2: ...2 This page left blank intentionally ...
Page 13: ...13 ...
Page 18: ...18 M2 H Identifying Your Machine Components Location of Tags and PIN Plates ...
Page 19: ...19 SECTION II Description Care and Maintenance ...
Page 31: ...31 SECTION III Set up and Installation of Unit in Detail ...
Page 33: ...33 SECTION IV Operating the M2 Unit ...
Page 41: ...41 SECTION V Troubleshooting the M2 Unit ...
Page 44: ...44 SECTION VI Periodic Maintenance Repair Information ...
Page 49: ...49 SECTION VII OEM Repair Information ...
Page 62: ...62 ...
Page 63: ...63 ...
Page 64: ...64 ...
Page 68: ...68 SECTION VIII Parts Manual ...