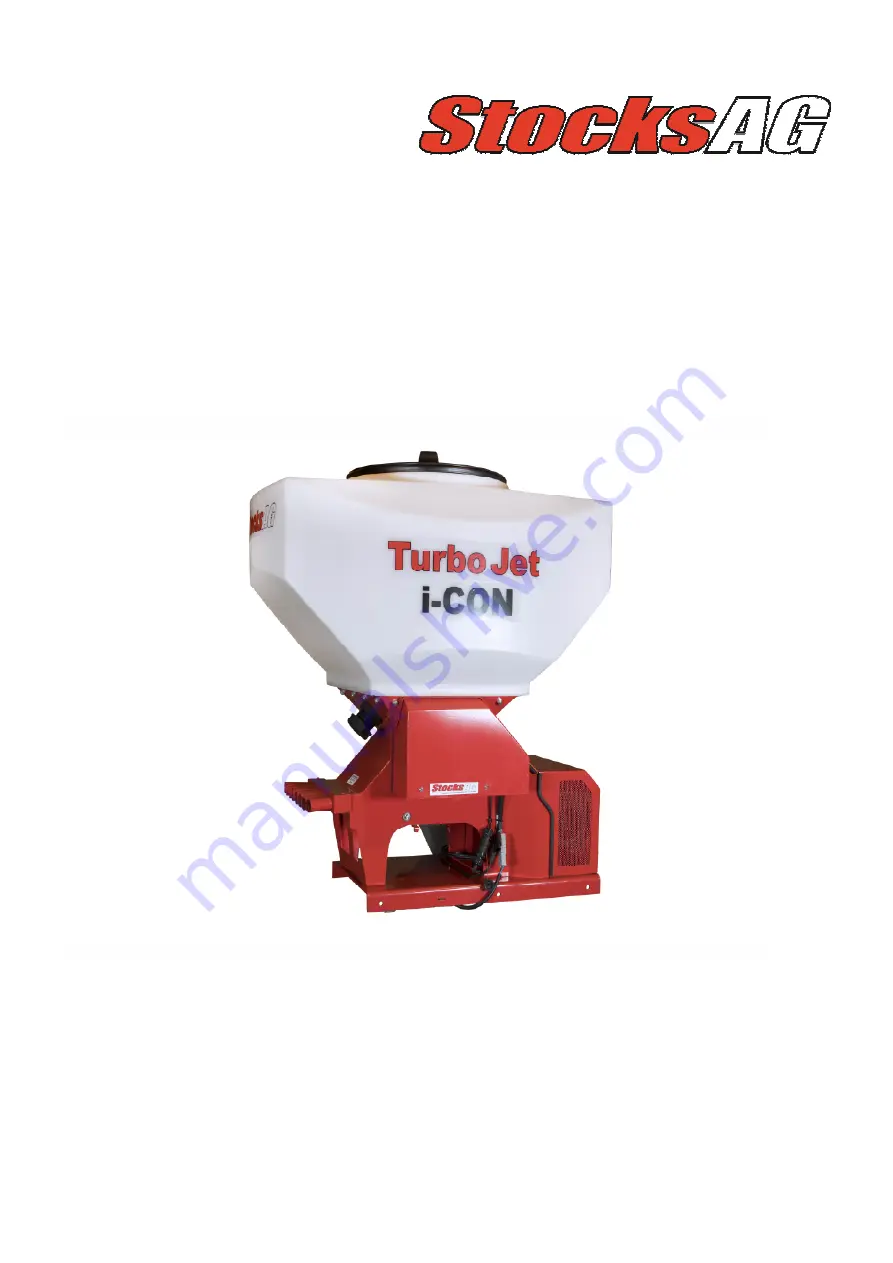
Turbo Jet 8 & 10 i-CON
Original Operating Manual
and Parts List
Read carefully before installation
and operation
This document must not be copied duplicated or distributed without prior consent .
All and patent rights apply
STOCKS AG LIMITED, CROMWELL ROAD, WISBECH, CAMBRIDGESHIRE, UK.
Tel: 00 44 (0) 1945 464 909 Fax: 00 44 (0) 1945 464985 www.stocks-ag.co.uk
Original Instructions, Revision 1 August 2020
Summary of Contents for Turbo Jet 10 i-CON
Page 22: ...22 22 Parts drawing 5 ...
Page 26: ...26 26 Feed roller kits ...
Page 29: ...29 29 Notes page ...
Page 30: ...30 ...