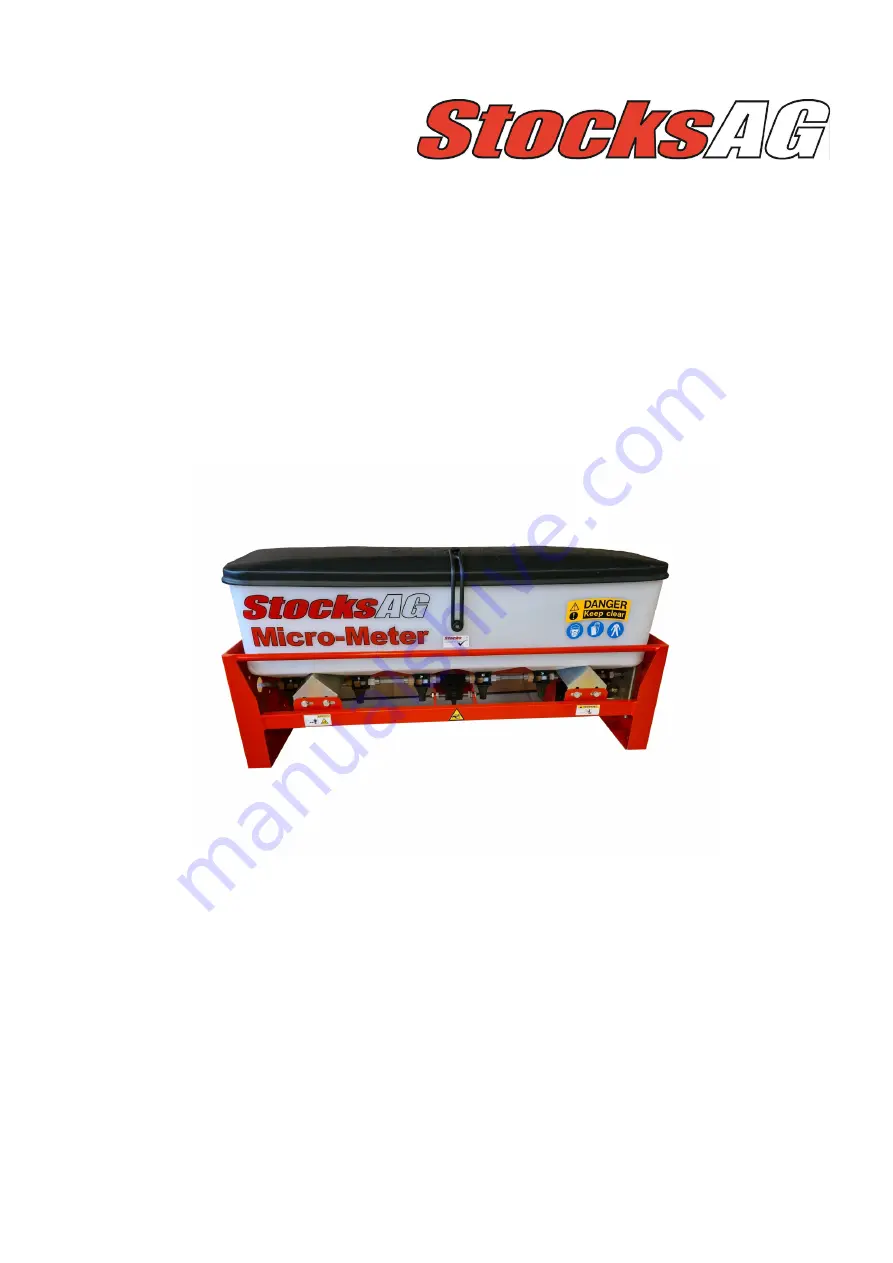
Original Instructions, Revision 1 August 2020
MICRO METER
i
-
CON
Original Operating Manual and parts list
Read carefully before installation and
operation
This document must not be copied duplicated or distributed without prior consent .
All and patent rights apply
STOCKS AG LIMITED, CROMWELL ROAD, WISBECH, CAMBRIDGESHIRE, UK.
Tel: 00 44 (0) 1945 464 909 Email: sales@stocks
-
ag.co.uk www.stocks
-
ag.co.uk