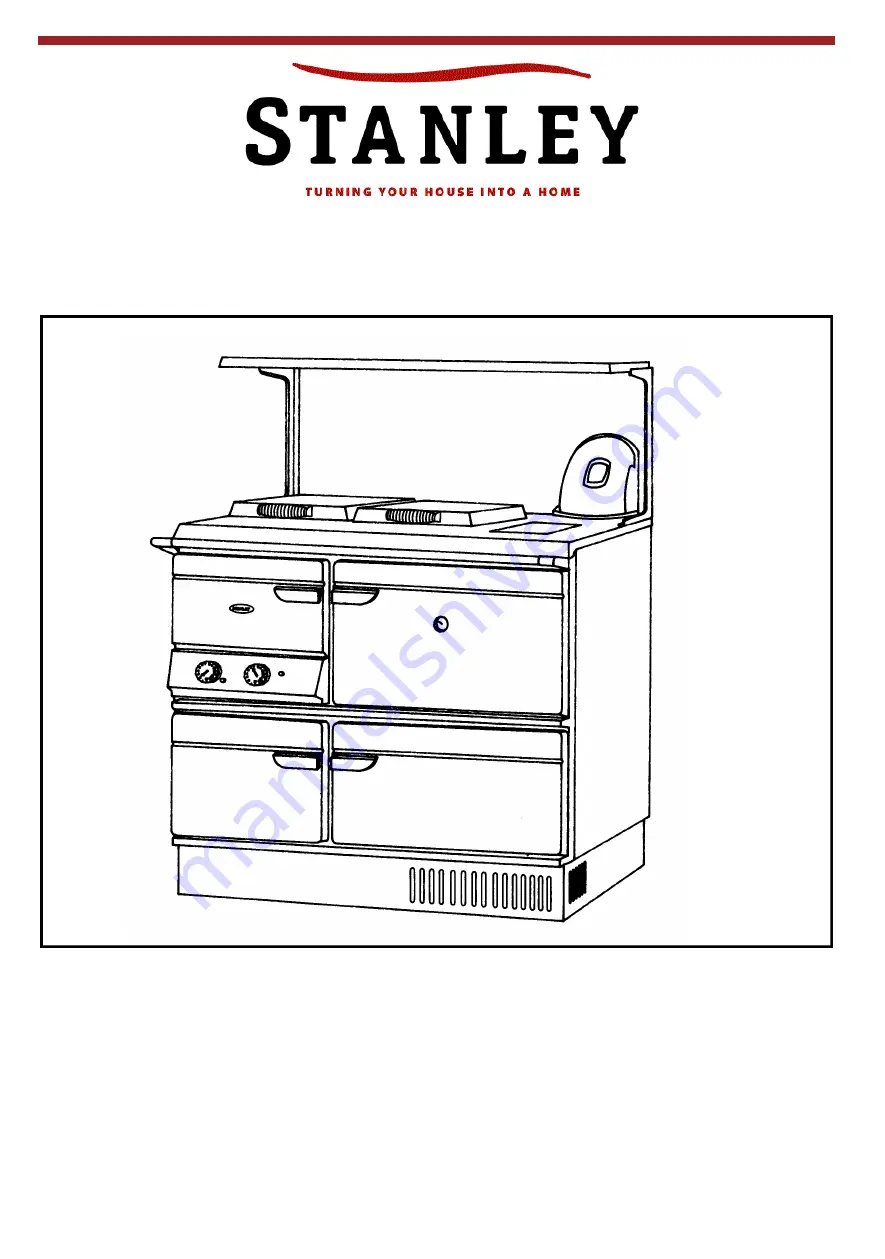
Donard 60 Oil fired Cooker
To ensure safety, satisfaction and reliable service,
this quality Cooker should be installed by a competent
person.
The provision of a Central Heating facility, requires that the hot water supply system involved,
conforms fully to good plumbing practice and established standards.
Installation and Operating Instructions
To be left with end user.
(SUPER STAR 60 K OIL FIRED COOKER)