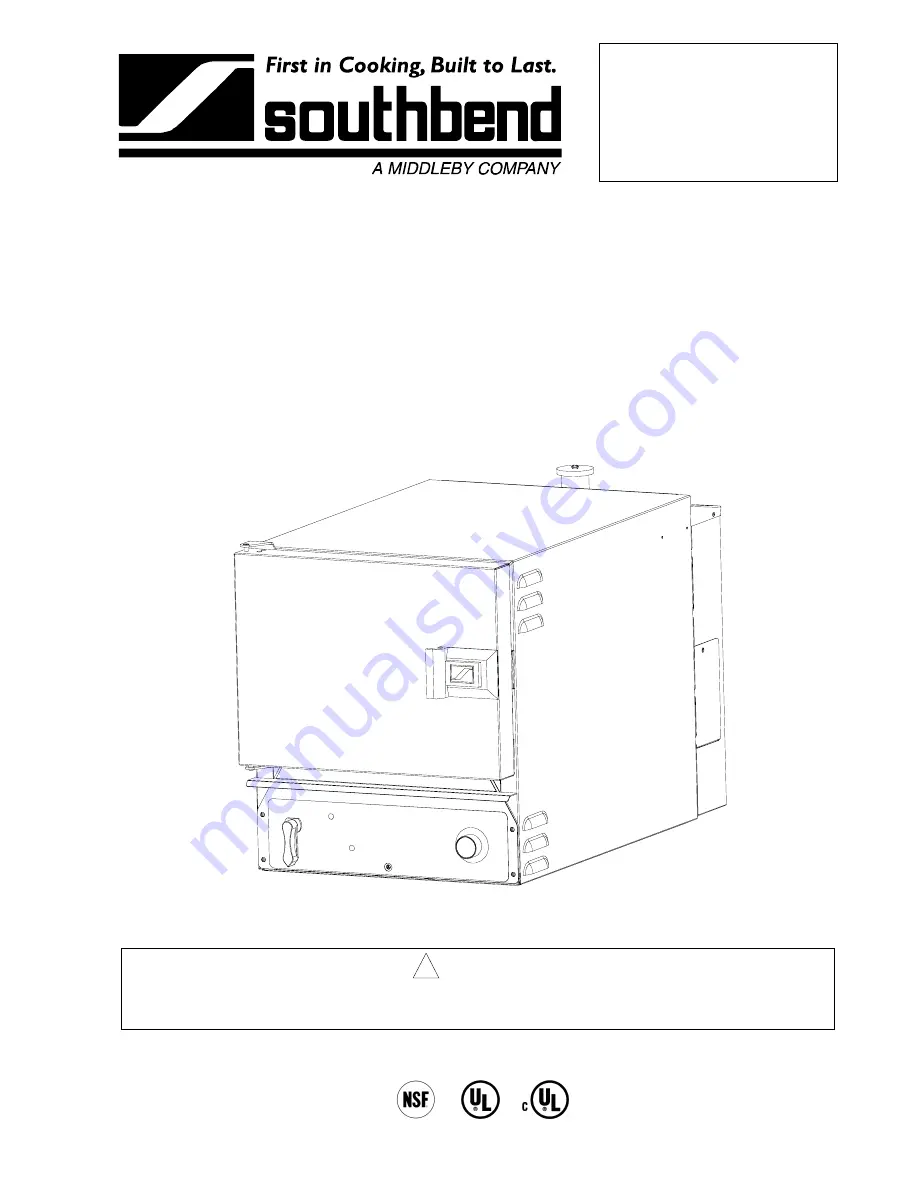
M
ANUAL
1183437
$18.00
COUNTERTOP STEAMER
MANUAL SECTION ST
OPERATOR’S MANUAL
Super Simple Steam
SEZ Series Countertop Steamers
For Models SEZ/3 & SEZ/5 Built After February 15, 2001
Model SEZ/3
!
WARNING
Improper installation, operation, service, or maintenance can cause property damage, injury, or death.
Read this manual thoroughly before installing and operating this equipment.
1100 Old Honeycutt Road, Fuquay-Varina, NC 27526
(800) 348-2558 or (919) 552-9161
•
FAX (800) 348-2558 or (919) 552-9798
IMPORTANT FOR FUTURE REFERENCE
Please complete this information and retain this
manual for the life of the equipment:
Model #: __________________________
Serial #: __________________________
Date Purchased: ___________________