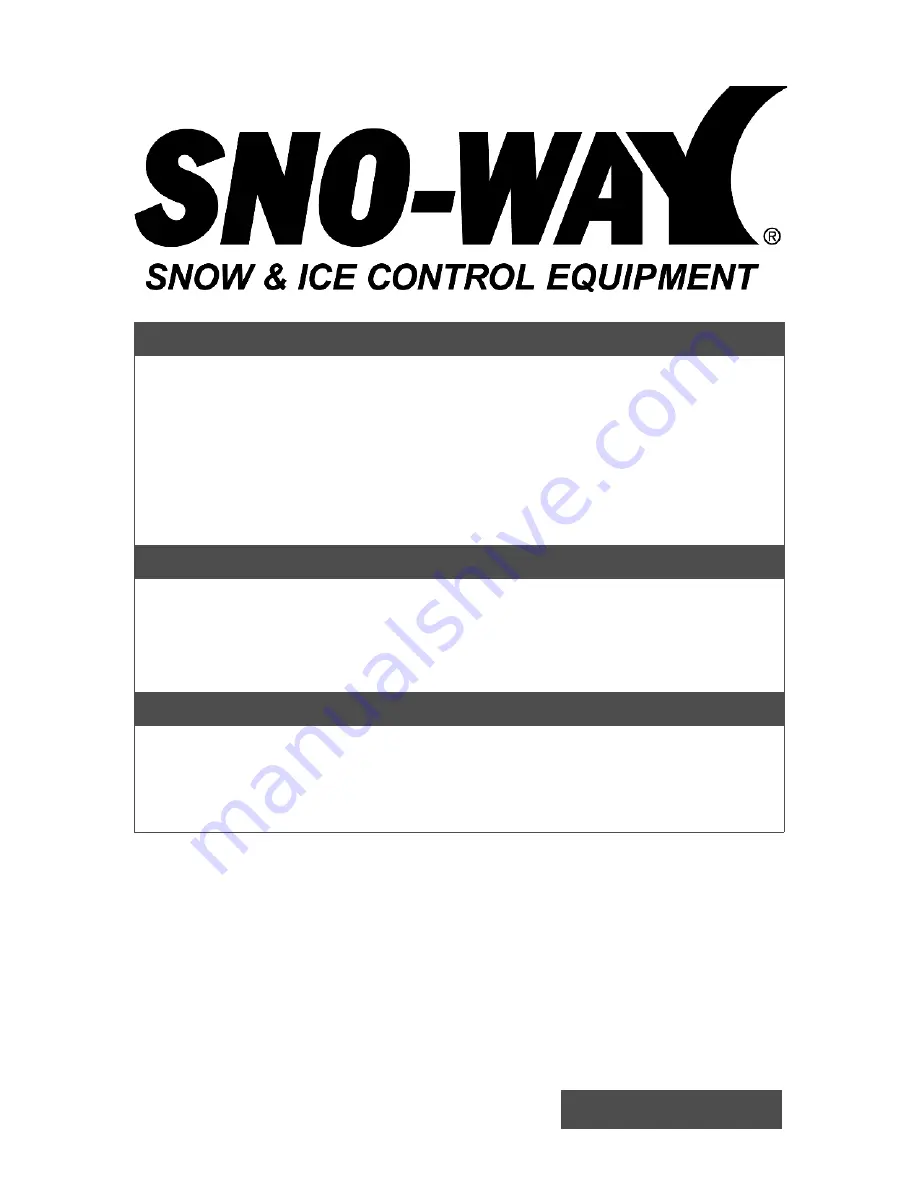
97102169A
INSTALLATION &
OWNER’S MANUAL
26V SERIES SNOW PLOW
WITH SERIAL NUMBERS AFTER:
26V100000
Sno-Way
®,
Down Pressure
®
and EIS
®
are registered trademarks of Sno-Way International, Inc.
ProControl
™
, MegaBlade
™
, V-Wing
™
, Revolution
™
and MaxAdjust
™
are trademarks of Sno-Way
International, Inc.
©2019 Sno-Way
®
International
Summary of Contents for 26V Series
Page 34: ...33 MAIN WIRING HARNESS SCHEMATIC EIS Energy Interruption SystemTM ...
Page 36: ...35 NOTES ...
Page 37: ...36 NOTES ...