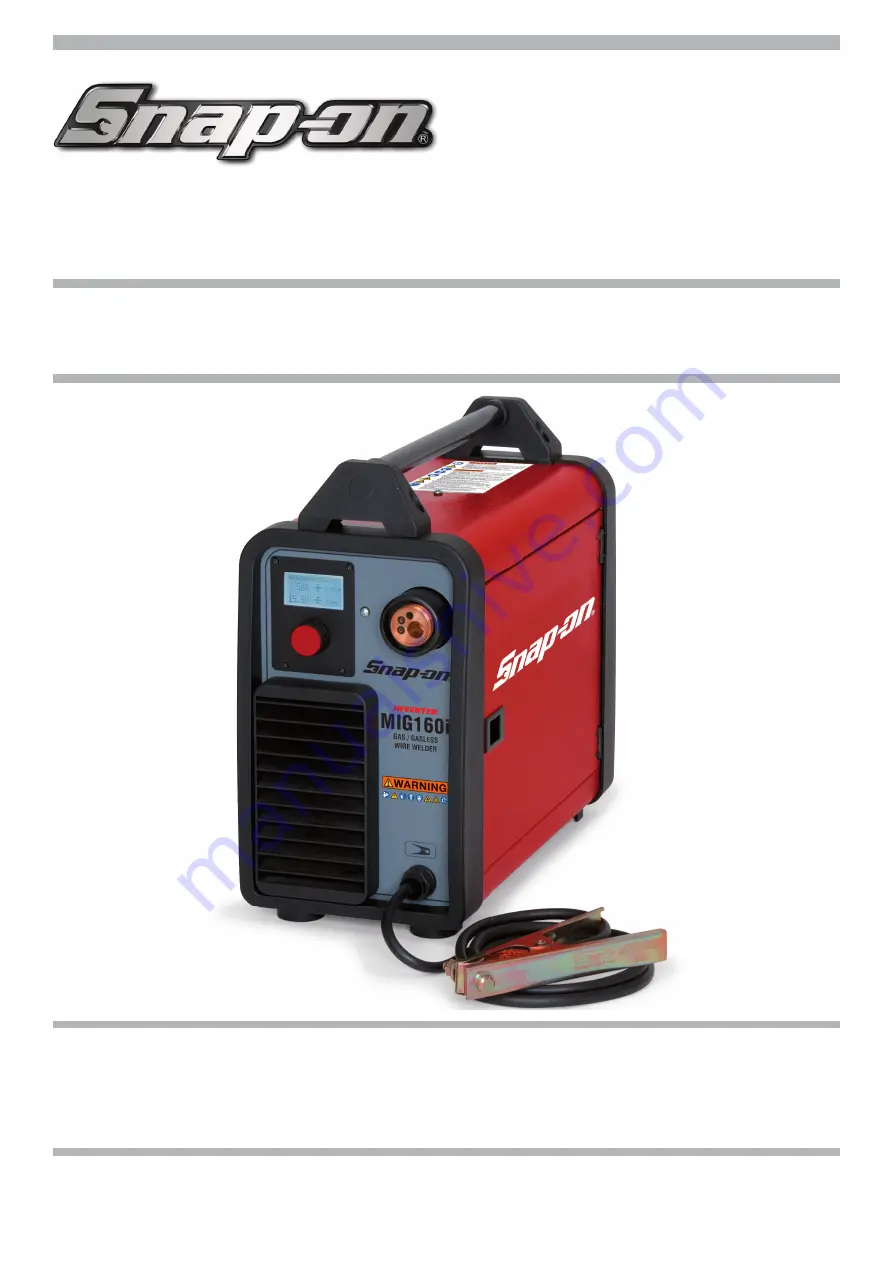
160 AMP MIG WELDER
MIG160i
The MIG160i is a single-phase synergic inverter power source for MIG welding. This versatile
power source is suitable for various applications from general repairs to specifi c material types
used in the body shop industry. Welds a variety of material types and thicknesses such as steel,
stainless-steel, aluminum, high strength and boron steels. Preset synergic curves automatically
provide proper settings for individual situations and reduce set up times.
INTRODUCTION
form WC 6000
3.300.048/B
INSTRUCTION MANUAL FOR WIRE WELDING MACHINE
Summary of Contents for MIG160i
Page 14: ...14 REPLACEMENT PARTS PARTS LIST ...
Page 16: ...16 WIRING DIAGRAM ...