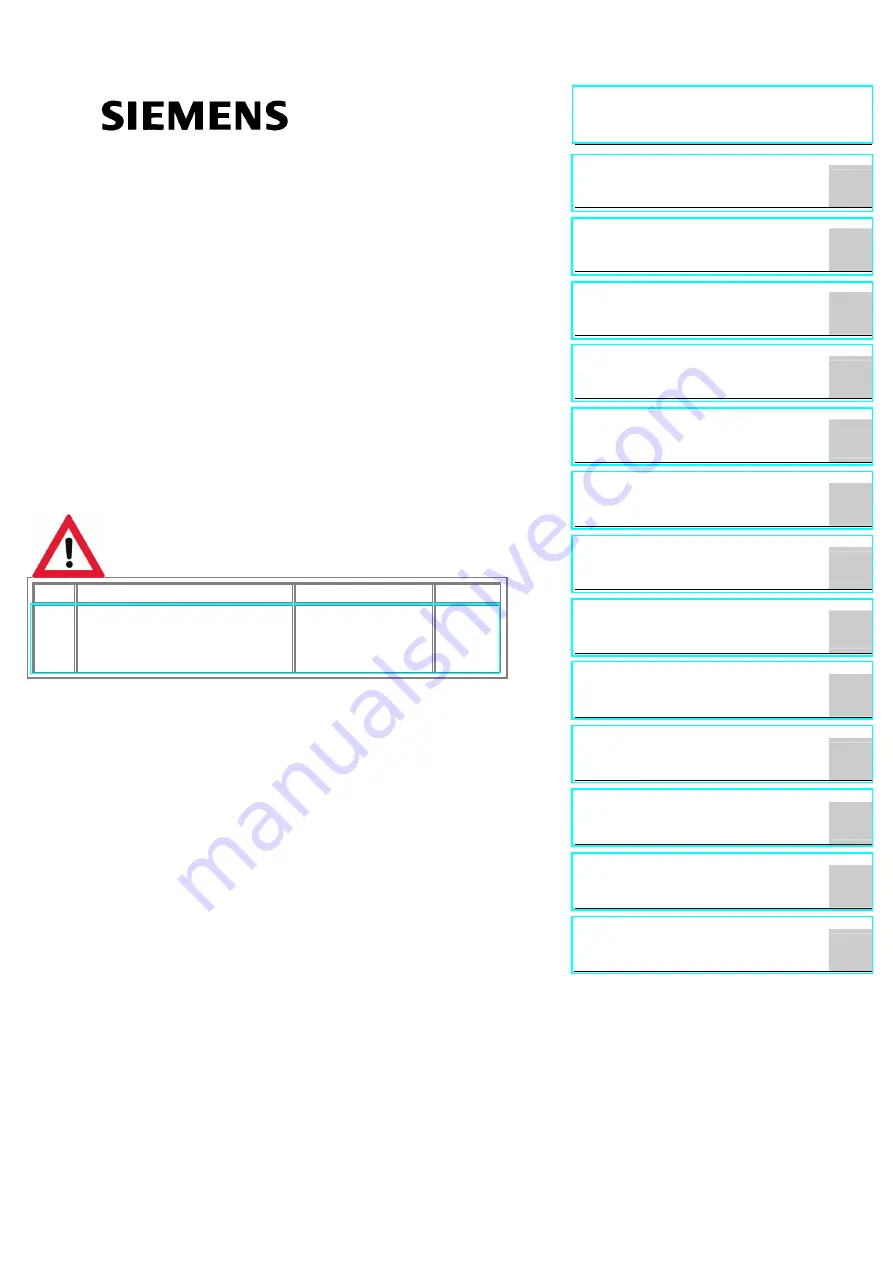
SIMATIC Distributed I/O fail-safe engineering ET 200pro Distributed I/O System - Fail-Safe Modules
______________
______________
______________
______________
______________
______________
______________
______________
______________
______________
______________
______________
______________
SIMATIC
Distributed I/O fail-safe engineering
ET 200pro Distributed I/O System -
Fail-Safe Modules
Operating Instructions
05/2007
A5E00394073-02
The following supplement is part of this documentation:
No.
Product Information
Drawing number
Edition